At the Land Forces conference in Adelaide, Australia, earlier this month, a development in military tech was presented that brings auto-camouflaging tanks a step closer to reality. To find out more about the technology behind the idea, we asked Peter Murphy from the University of South Australia, who was involved in the research, a single question as part of our regular One Big Question series:
What goes into making a color-changing military tank?
The concept of color-changing tanks, able to change their camouflage pattern in real time in the battlefield to adapt to changing surroundings, is one of the holy grails of modern military deception. Even in the modern theatre of war, preventing initial detection by the human eye is the primary goal in deceiving the enemy.
The limitation of present camouflage technology is that it is generally a static system that has been painted onto the structure it is protecting. Such camouflage patterns come in a variety of forms to typically suit either woodland, desert or snow-based environments. Adaptive camouflage would have the capability to work across all of these environments, much like a chameleon or octopus is able to change color to suit the surroundings it is in.
A group of researchers from the University of South Australia's (UniSA) Future Industries Institute has been working in partnership with scientists from Australia's Defence Science & Technology Group (DST Group) on developing adaptive camouflage using materials known as conducting polymers.
These materials are effectively plastics that conduct electricity. By applying a very thin coating of these materials to a surface and surrounding them with an electrolyte, it is possible to make them change color when a voltage is applied to them. By using conducting polymers with varying chemical structures, different color changes can be achieved.
The conducting polymers and electrolyte are housed in a transparent sandwich-like structure (the electrochromic cell) that is sealed around the edges. The faces of the cell can be made out of various materials ranging from glass, to polycarbonate or even PET (polyethylene terephthalate) – the material previously used to make overhead transparency sheets.
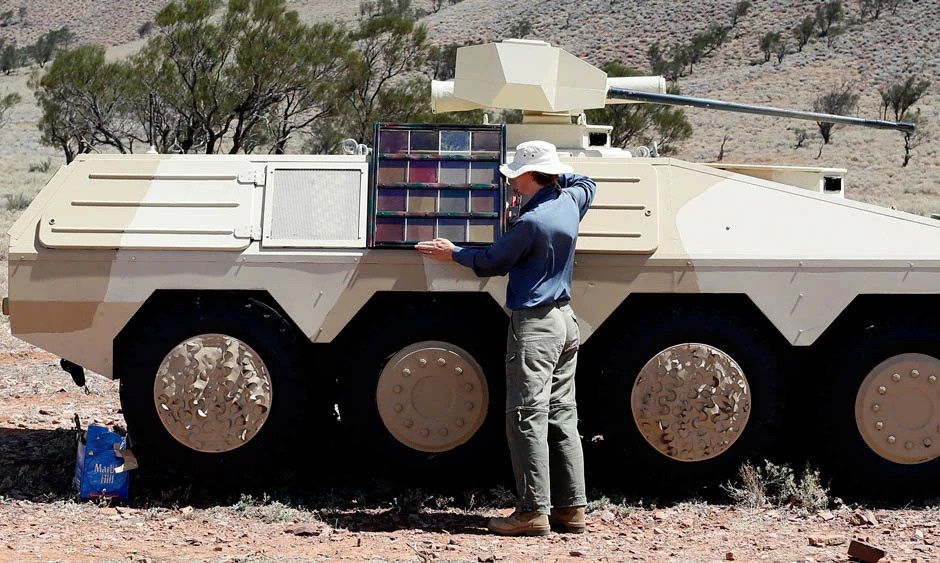
Key to making this technology work in the real world is to ensure that the electrochromic cells are robust and lightweight. It is not unreasonable to expect the electrochromic cells to function in the temperature range from -40 to 80 degrees Celsius (-40 to 176 degrees Fahrenheit), which is the requirement for parts produced for the automotive industry. The electrochromic cells also need to be able to survive shock, abrasion damage and be stable in UV light.
The current research at UniSA is focussed on developing lightweight flexible electrochromic cells up to 20 x 20 cm (7.9 x 7.9 in). These cells are able to be fixed to the outside of a tank (using strong double-sided adhesive) and are wired together and connected to a battery for power supply.
In a fully functioning system, you would use cameras that would automatically sense the surroundings/background and then adjust the electrochromic camouflage cells to suit. The color change could occur over a timeframe ranging from a few seconds to several tens of seconds. The rate of color change can be adjusted to the level required – that is, it can be increased or decreased according to the speed of the vehicle. A total color change can be achieved in as little as one second if required.
Using this technology, the color-change pattern is determined by the coating process used to fabricate the cells. It is highly likely that a robotic spray-coating process would be used to produce the electrochromic cells at a commercial level. Such a process is amenable to producing both block color patterns and also complex patterned cells.
In reality, the ability to produce complex patterns is likely to be most useful, as it would allow a degree of complexity to the patterns that would aid with the deception process. Our most recent prototype cells indeed focus on producing complex patterns, with changes in color and color intensity within a cell.
To date we have only tested small arrays of the cells (such as those shown in the photo above) and have recently completed transitioning the technology from glass to polycarbonate cells – halving the weight of the system. The next stage of the project will see the technology evolve to fully flexible cells able to be bent over an edge or corner as you would find on vehicles.