Steel or cement, plastics or carbon fiber, silicon or graphene: Whether in construction, aerospace or electronics, picking the right material for the job involves choosing the best fit among a limited number of options, which often leads to tricky compromises. Now, a development at the Masdar Institute in the United Arab Emirates could mark a paradigm shift toward designing and 3D printing high-performance materials with features that are custom-designed to fit a specific application.
Rather than creating entirely new materials, Professor Rashid Abu Al-Rub and his team focused on changing the internal geometric structure of familiar plastics, metals, ceramics and composites. Tweaking materials from the ground up allowed the scientists to control their mechanical, thermal and electrical properties in unique ways, even bucking some established trends.
Density and strength, for instance, usually go hand in hand. Strong materials like metals and alloys tend to be heavy, while foams and other lightweight composites are normally much weaker. Changing the internal structure, however, can lead to materials that are both strong and light at the same time by being airy rather than solid, and by deriving their strength from their shape alone. This is the same principle that gives the Eiffel Tower structural strength through the arrangement of its metal struts, despite the structure being 90 percent air.
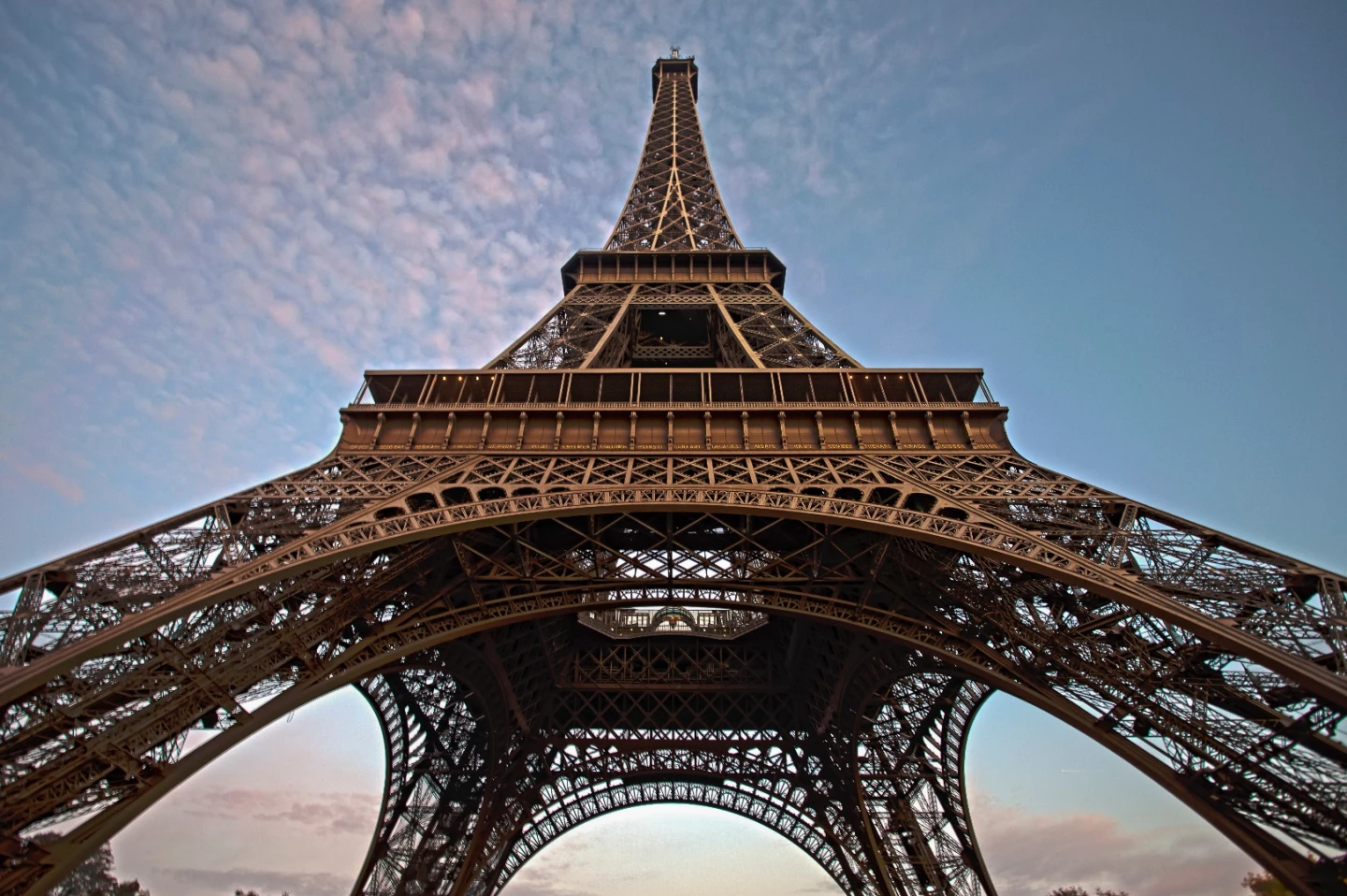
Abu Al-Rub and colleagues built a computer model that can generate thousands of geometric arrangements, or "architectured foams," for a given material. Each design gives rise to a different set of thermal, electrical and mechanical properties solely through implementing a different geometry. More importantly, the model can be directed to find the arrangement that maximizes certain properties to fit a desired application.
The structures are very complex, so they couldn't be produced through conventional manufacturing methods. Luckily, however, recent technological advances have made it possible to 3D print these structures even though, in some cases, their features might be only a few nanometers (billionths of a meter) in size.
According to the researchers, the combined ability to design custom properties into a material and then manufacture it through 3D printing could disrupt the future of material design.
"Currently, people design materials based on a material's existing chemistry, structure and its corresponding properties," says Abu Al-Rub. "Our vision for material design instead looks first at the desired properties you are targeting in a material for a product application and then applies our proprietary design methods to optimize the structure and its internal geometry so that it will give you those desired properties."
Applications could range from the aerospace industry, which would take advantage of the high strength and low weight of the nanoengineered materials, to fields that would take advantage of the materials' porosity, such as water desalination or gas filtration.
"This is elegant work which combines computational and experimental techniques to develop models that can predict the electrical properties of nano composites created by 3D printing," Dr. Thomas Webster, Professor of Chemical Engineering at Northeastern University, who was not involved in the study, told Gizmag.
The principal value of this work, Webster tells us, is in the development of computer models that, while not perfect, can give a fairly accurate prediction of the conductivity of a composite material based on its architecture even before it's 3D-printed.
The researchers are now looking for industry partners to bring this idea closer to commercialization.
The study has been featured in several peer-reviewed journals, including Composites Science and Technology.
Source: Masdar Institute