Driverless vehicle systems are used in factories the world over, but traditional setups require the installation of special railings or magnetic guides. A fleet of self-driving electric cars don't need any such help to navigate Nissan's Oppama plant, where they tow fully-built cars around the factory complex.
Each self-driving Leaf is fitted with an array of cameras and laser sensors, set up to detect lane markings and curbs, as well as hazards like cars, people and machinery. Data from these sensors is cross-referenced with map information, allowing the car to calculate its own position within the factory complex.
Having been fed a destination, the car will automatically navigate, traveling under the factory speed limit and automatically coming to a halt when an obstacle is detected. When the path is clear, it will take off again.
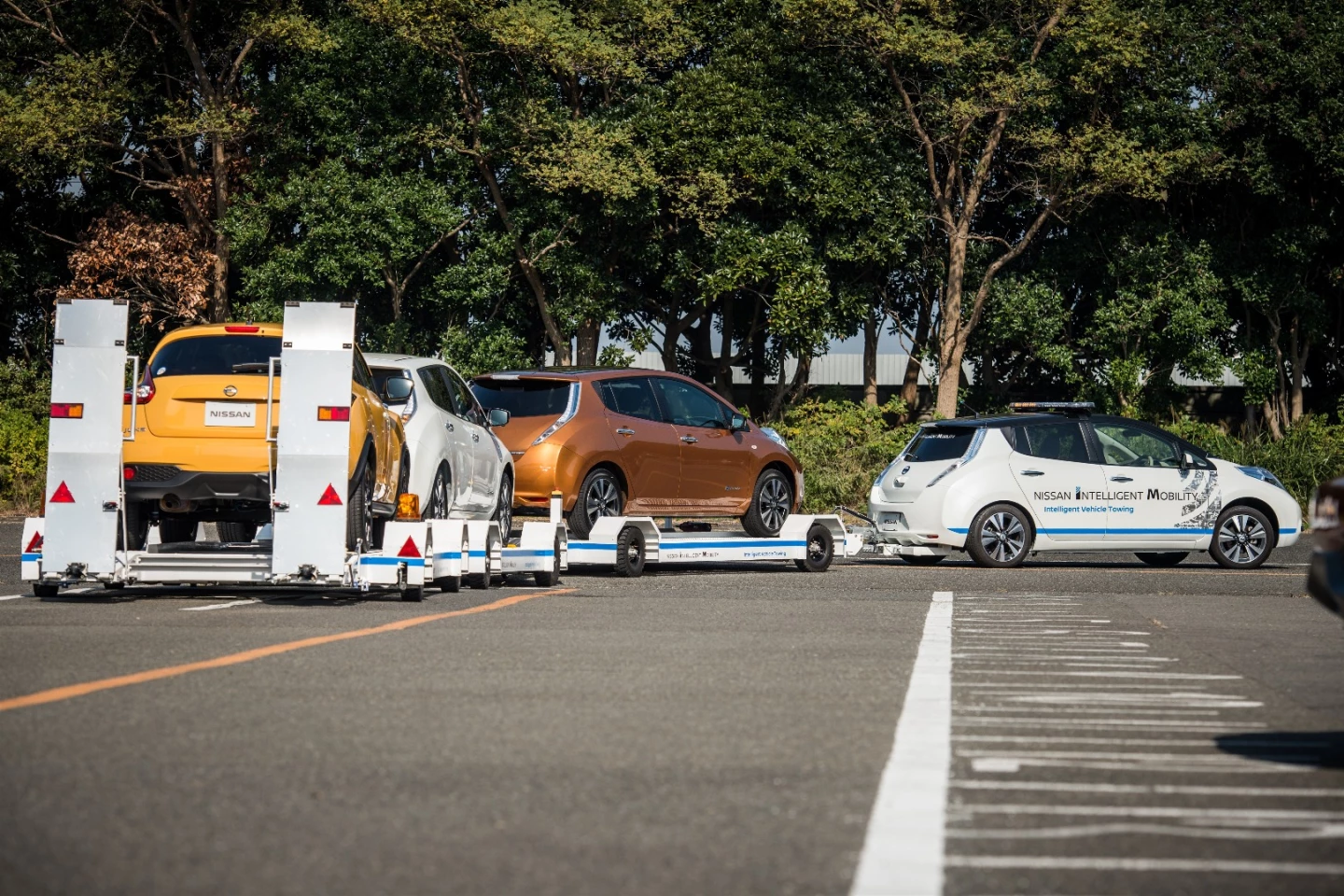
When routes need to be changed, or the layout of the factory complex is altered, the towing route can be modified through software, rather than requiring expensive changes to railing or magnetic strips on the ground. The self-driving tow cars are all linked to a central traffic control system, which keeps an eye on where they're heading, how fast they're going and how much battery they have left.
If two members of the fleet arrive at the same intersection, the system works out which one should be given priority, and cars can be shut down remotely in an emergency.
When it's completely up-and-running, Nissan says the Intelligent Vehicle Towing program will have a big impact on efficiency at the Oppama plant. The system has been subjected to 1,600 test runs in the past 12 months, and is likely to be rolled out at other Nissan plants if it proves successful.
Take a look at the Intelligent Vehicle Towing program in action in the video below:
Source: Nissan