In a field where highly complex machinery often pulls the strings of highly complex maneuvers, a system that relies on a single ball to get around is certainly at the simpler end of the spectrum. Ten years ago we were introduced to such an idea, and now the team behind the original Ballbot is back with an even less complicated system. The upgraded machine is dubbed SIMbot and uses an experimental induction motor rather than a mechanical drive system for mobility, resulting in a robot with minimal moving parts.
The original Ballbot was invented by Professor Ralph Hollis, a robotics researcher at Carnegie Mellon University. The tall and slender robot was battery operated and omnidirectional, a set of characteristics its creator says lends itself particularly well to working with people in busy environments.
Because of its slender form and great agility, the robot can roll through doorways, in between furniture and can quite easily be moved out of the way when needed. A few years ago, a company spun out of Carnegie Mellon sought to make use of these capabilities with a version called mObi, eyeing hospitals and offices as its first port of call. The machine has also inspired a number of ballbots around world from roboticists in Japan, Switzerland and Spain.
But ballbots have relied on mechanical parts to move the ball at its base and keep the robot upright. Described as an "inverse mouse-ball drive," this sees motors actuate rollers that press against the ball, move it in the required direction and keep it from tipping over. These act on information gathered by internal sensors that track the robot's balance.
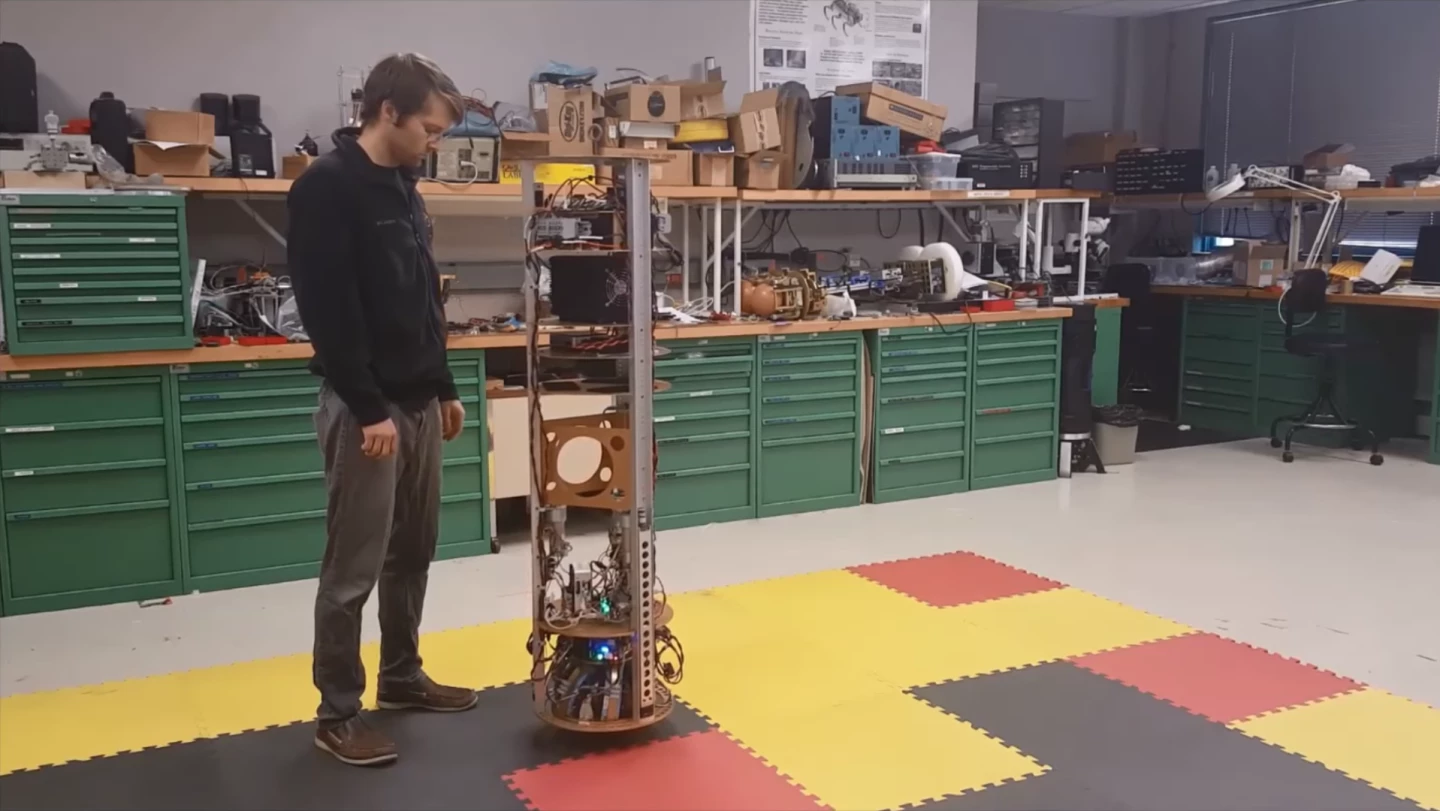
"But the belts that drive the rollers wear out and need to be replaced," says Michael Shomin, a Ph.D. student in robotics at Carnegie Mellon. "And when the belts are replaced, the system needs to be recalibrated."
So the team explored more mechanically simplistic means of keeping the ballbot on the move. This led them to induction motors, which are motors that use magnetic fields to induce an electrical current and generate torque rather than relying on electrical connections. They are actually fairly commonplace and can be found in ceiling fans, industrial machinery and Elon Musk's Hyperloop plans.
But applying the technology to a spherical form is a challenge. While the team says progress has been made in this area before with spherical induction motors (SIMs) that can move back and forth a few degrees, their design, combined with advanced software and mathematics, allows for a spherical motor that can spin freely in any direction.
The SIM rests on a hollow iron ball inside a copper shell. Six laminated steel stators sit alongside the ball and produce traveling magnetic waves, guiding the ball in that direction. By altering the currents produced by the stators, the SIMbot can be steered in different directions.
Replacing the belt drives with electric currents cuts down on friction and makes the machine more efficient, but it may also make for more reliable ballbots that require less routine maintenance. And because of the shift away from mechanical components, it may also make them cheaper in the long run.
"This motor relies on a lot of electronics and software," says Hollis. "Electronics and software are getting cheaper. Mechanical systems are not getting cheaper, or at least not as fast as electronics and software are."
You can see the SIMbot in action in the video below.
Source: Carnegie Mellon University