Electric vehicles powered by renewable energy sources are hitting the roads in greater numbers every year, but the transition away from gas guzzlers is going to take a while. In the meantime, scientists are working on ways to clean up existing fossil fuels, and a new refining process developed at Caltech uses a potassium catalyst to reduce the amount of sulfur in gasoline and diesel to a fraction of their current levels.
Sulfur is naturally present in crude oil, and although the refining process reduces its levels, some of it still ends up in the resulting fuel. When that fuel is burned, sulfur dioxide (SO2) is released into the atmosphere, where it's considered an indirect greenhouse gas. Companies like Boeing and Audi are working on cleaning up their act by developing their own alternative "green diesel" fuels.
The US Environmental Protection Agency (EPA) has implemented regulations over the years to reduce the amount of sulfur permissible in gasoline and diesel fuels, with the latest rules, which came into force at the start of this year, capping the average annual amount of sulfur at 10 parts per million (ppm). Doing so helps make existing vehicles significantly more environmentally friendly.
"Using lower-sulfur gasoline in cars currently on the road will reduce as much pollution as taking 33 million cars off the road," Paul G. Billings, senior vice president of the American Lung Association, said in 2013. "This pollution triggers asthma attacks, worsens lung and heart health and can even lead to early death."
The Caltech team boasts that its new process can reduce sulfur levels down to just 2 ppm, well under the EPA-enforced cap. Better yet, it works using elements that are cheap and abundant, as opposed to other catalysts that require rare-Earth metals like platinum.
The original discovery was made a few years ago, while the team was using platinum as a catalyst to break carbon-oxygen bonds. Running a control test without the catalyst, the researchers were surprised to find that the required chemical reactions were somehow still occurring. After a few more tests, the team realized that a potassium salt called potassium tert-butoxide was responsible.
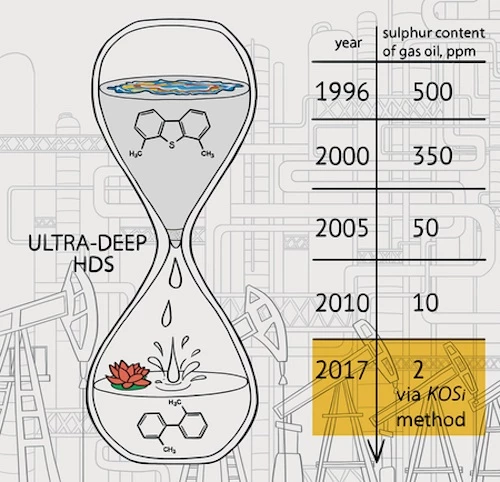
Building on this discovery, the new process is called the KOSi method, named for the elemental symbols of the catalyst's ingredients: potassium (K), oxygen (O) and silicon (Si). All of these elements are easy and inexpensive to obtain, and the end result is highly effective at removing sulfur from carbon compounds in diesel fuel.
"We were really surprised how well the potassium salt worked," says Anton Toutov, lead author of the study. "The sulfur is contained in small organic molecules, and this process just rips it right out."
The team tested the process on refined diesel samples provided by BP, a mix considered to be high quality commercially-available fuel, containing sulfur levels of 8 ppm. The KOSi method reduced the sulfur content to an even cleaner 2 ppm. When tested on diesel with a far higher amount of sulfur, the process still managed to bring the levels down to these record lows.
"We simulated a high-sulfur oil and eliminated almost all of the sulfur through a simple chemical process," says Toutov. "The next step is figuring out how to streamline the process and make it work on an industrial scale."
The team is currently getting to work on that goal, and apparently have "a number of ideas in mind" about how to achieve that, such as sourcing and recycling waste products from other industries. Toutov is co-founding a new company called Fuzionaire to bring the technique to market, which could become a standard step in the oil refinery process to remove the last lingering traces of sulfur from fuel.
The research was published in the journal Nature Energy.
Source: Caltech