A research team from the Department of Energy’s Oak Ridge National Laboratory (ONRL) has created a new model for how we can connect the way we power our homes and vehicles. Dubbed AMIE (Additive Manufacturing Integrated Energy), the platform features special technology that allows a bi-directional flow of energy between a dwelling and a vehicle. In other words, the house can fuel the car and the car can fuel the house. What's more, ORNL used 3D printing technology to build the dwelling and the vehicle, before successfully trialing the new energy system.
"Inthe AMIE demonstration project, we are trying to illustrate what ourfuture might look like if we shared our energy streams for buildingsand transportation, using additive manufacturing as a tool to driverapid innovation," ORNL’s Roderick Jackson, who led the AMIEdemonstration project, told Gizmag. "The challenges we facecan’t wait for the innovation cycles that currently exist for ourbuildings and vehicles energy ecosystem. These challenges includeelectricity outages caused by extreme weather events, energy povertyaround the globe, and intermittent renewable generation."
AMIEboasts the world's very first working level 2 (6.6 kW) bi-directionalpower system. The building is fitted with a flexible 3.2 kW solarphotovoltaic system, which is then paired with electric vehiclebatteries, providing renewable power generation and storage. Energycan flow in either direction between the house and the vehicle via awireless transfer system. This also means the vehicle can power the house when the sun has gone down or during cloudy periods.
"Inone-direction, AMIE can charge the car battery and in the otherdirection, the car can power AMIE," said Jackson. "Theefficiency of the bidirectional wireless power transfer (BWPT) systemis roughly around 85 percent. BWPT uses a resonant technology that allowshigher efficiencies through larger gaps."
ORNLworked alongside architectural studio Skidmore, Owings & Merrillto construct the 210 sq ft (19.5 sq m) building. The single-room structure wasbuilt using 3D-printed parts and features curved lines and costeffective vacuum insulated panels. The home is equipped with a micro-kitchen concept, developed by GE FirstBuild, and the rooftopphotovoltaic system is paired with batteries from a previouslyused Fiat 500e.
"One of the interesting energy saving features is novel modified atmosphere insulation (MAI) panels developed by NanoPore that are about seven times more energy efficient than traditional wall insulation," revealed Jackson.
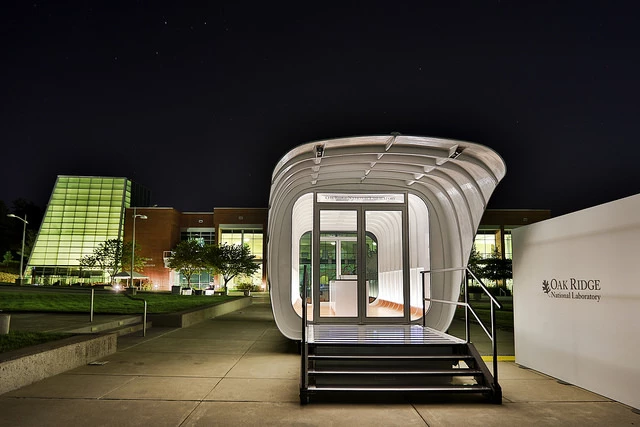
Carbonfiber-reinforced ABS plastic composite material was used to printapproximately 80 percent of the house components and 30 percent of the vehicle's.The fact that the team could build the structure using 3D technologymeant design elements could be tested and trialed without losing timeor momentum. It also meant they could create curved shapes andperfectly fitting bespoke elements without the limitations oftraditional building techniques.
"Ourability to test design form and fit at scale and in real time enabledan 'innovation on the fly' process that could revolutionize how weapproach building construction and design," ORNL's Director ofEnergy and Transportation Science Division, Johney Green Jr, told Gizmag.
The3D-printed utility vehicle features an electric hybrid power-train, which makes use of natural gas to extend its range. Thanks to creating the vehiclewith 3D-printed components, theappearance of the vehicle can be modified with new body parts as desired.
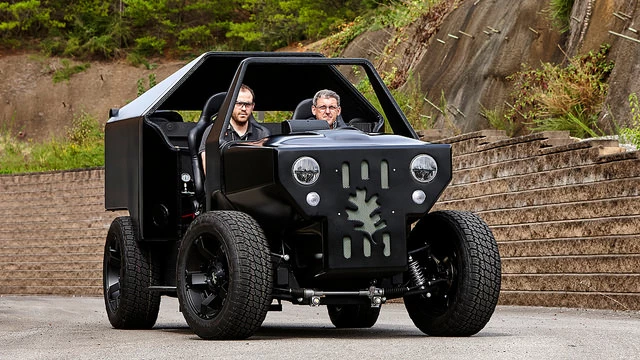
Althoughthe weight of the vehicle is currently close to 4,010 lb (1,819 kg), additionalresearch will go into developing a lightweight version. ORNL is alsohoping to trial external combustion engines such as the Stirlingengine; high efficiency internal combustion engines with bio-fuels,hydrogen fuel cells and advanced energy storage units, such as flowbatteries and consumable batteries.
"Theenergy generator used in the current configuration is a very smallinternal combustion engine natural gas generator," said Green."This small 5.5 kW engine/generator is an example of the extremedownsizing possible with range extended electric vehicleconfigurations. In addition to range extension for the printedutility vehicle, the engine/generator is ideally sized for providingpower to small buildings such as the printed AMIE house."
It should also be noted that the current prototype was not designed aroundoptimum speed or performance, but more to demonstrate the capabilitiesof AMIE.
"Theprinted utility vehicle is currently configured with a 14 kWh battery, which with the current weight allows an all-electric rangeof 35 miles for city driving and a top speed suited for highway use(~60 mph)," continued Green. "We could configure the vehicle tohave different performance characteristics. The range of thevehicle depends upon how much fuel is carried on board and thespeed of the vehicle depends upon the power-train configuration."
ORNL is currently considering the option of making the plans open sourceand there is already talk of an AMIE 2.0, incorporating improvements andlessons learnt from AMIE 1.0.
"Wehave not finalized any plans to put the design files in the publicdomain, but that is something worth considering," said Jackson."We hope that this project inspires others to ask 'what if' and use technology to drive innovation."
Thevideo below illustrates the ideas and technology behind ORNL's AMIEdemonstration.
Source: Oak Ridge National Laboratory