A team at MIT has genetically modified bacteria cells and developed a new 3D printing technique to create a "living tattoo" that can respond to a variety of stimuli.
Electronic tattoos and smart ink technologies are showing exciting potential for reframing how we think of wearable sensor devices. While many engineers are experimenting with a variety of responsive materials the MIT team wondered if live cells could be co-opted into a functional use.
The first step was to look at what organic cells could be utilized, and it turned out that the strong cell walls of bacteria were the best target for use as they could survive the force of a 3D printer's nozzle. Bacteria also proved to be perfectly compatible with the hydrogels needed for accurate 3D printing.
To test out the technique the team created a 3D-printed patch of bacteria cells on an elastomer layer designed to resemble a tree. The bacteria in each branch of the tree was engineered to respond to a different chemical stimuli. When the patch was tested on a human hand that had been applied with different target chemicals the bacteria successfully illuminated its branches when sensing the corresponding chemical.
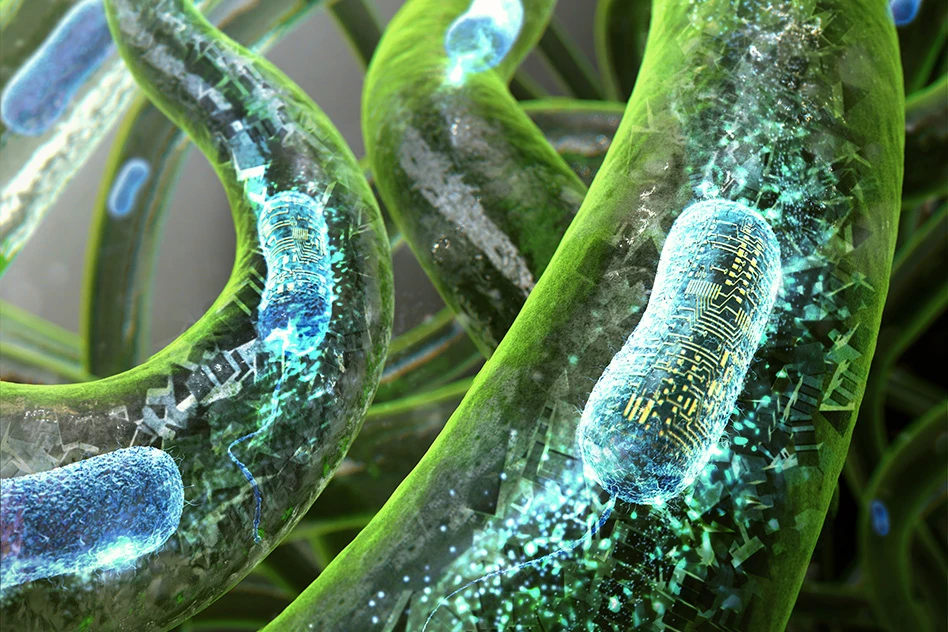
The ultimate outcomes for the technology are incredibly futuristic, with the team suggesting the technique could conceivably lead to the development of a kind of "living computer." Complex structures could be created that contain many different types of engineered cells that communicate with each other in the same way as transistors on a microchip.
"This is very future work, but we expect to be able to print living computational platforms that could be wearable," say Hyunwoo Yuk, a graduate student at MIT and one of the co-authors on the study.
More immediate, pragmatic uses include the development of warning stickers that contain cells engineered to respond to a certain environment or chemical stimuli, or health-monitoring wearables that activate signals in accordance with a specific temperature or pH change.
The study was published in the journal Advanced Materials.
Take a closer look at the technology in the video below.
Source: MIT