NASA engineers are using a 3D laser printing system to produce intricate metal parts such as rocket engine components for its next-generation Space Launch System (SLS). The method called “selective laser melting “ (SLM) promises to streamline fabrication and significantly reduce production costs.
Rocket engines are as complex as precision watches, but watches don’t have to deal with highly corrosive or cryogenic liquids, gases hot enough to melt steel, or destructive stresses and vibrations. Rocket engines have to do all this the first time they’re used and they have to fit a great deal of gear into a very cramped space. Fabricating the parts for these engines is an exacting, time consuming and expensive task. Since many of their components are very intricate, making them is just the sort of job for 3D printers.
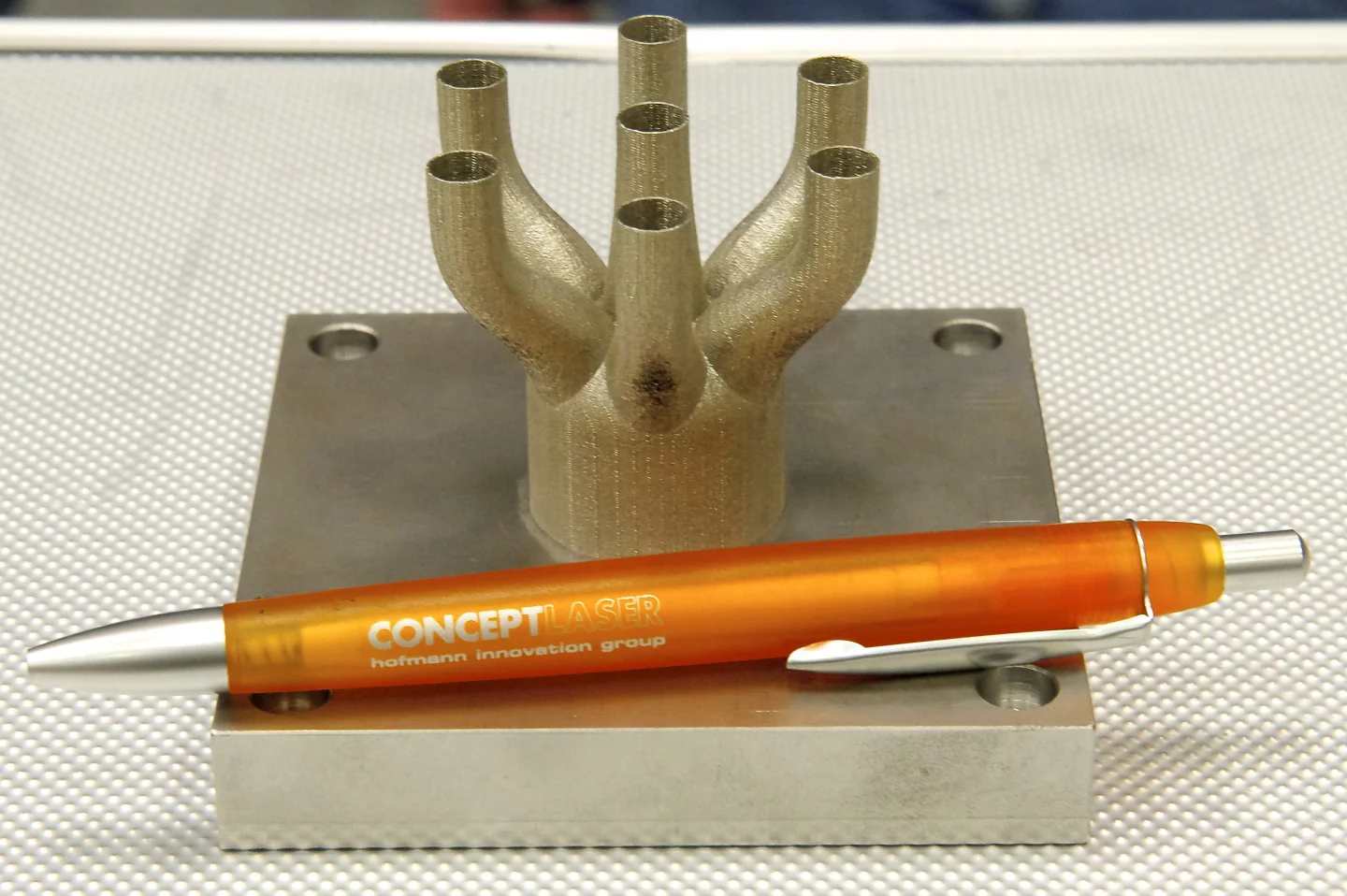
For the SLS, NASA is using an M2 Cusing Machine built by Concept Laser, which is a division of Hoffman Innovation Group of Lichtenfels, Germany. The M2 is similar in principle to other 3D printers, but instead of causing polymers to set, the M2 works in stainless steel, hot-worked steel, aluminum, titanium and nickel alloy by means of a 200 W fiber laser.
"Basically, this machine takes metal powder and uses a high-energy laser to melt it in a designed pattern," says Ken Cooper, advanced manufacturing team lead at the Marshall Center. "The laser will layer the melted dust to fuse whatever part we need from the ground up, creating intricate designs. The process produces parts with complex geometries and precise mechanical properties from a three-dimensional computer-aided design."
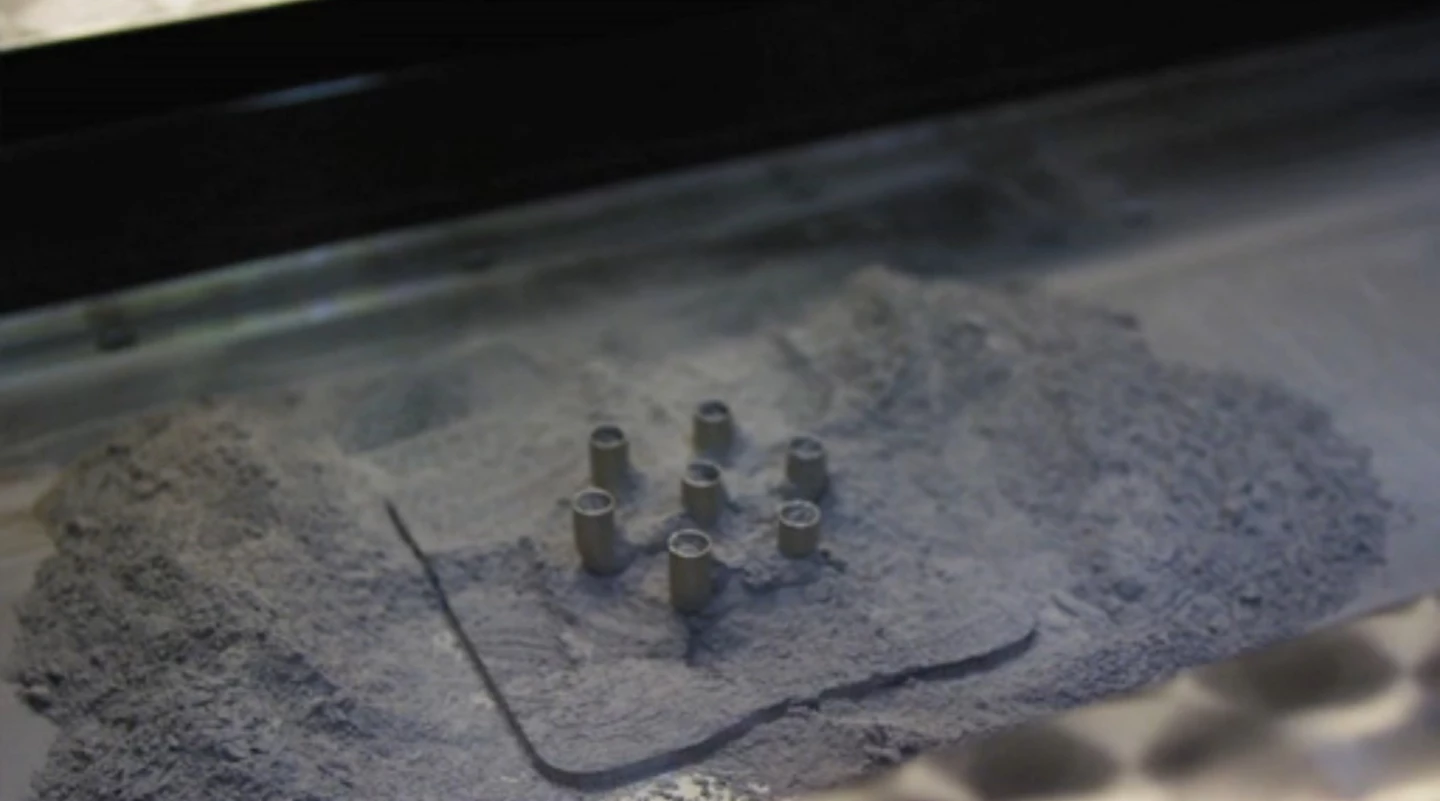
This method allows parts that once had to be built in simple sub-stages and then stuck together to be made in one go, which eliminates many fabrication problems and can reduce costs by as much as half. It also improves safety because metal powders like titanium burn in air, so the M2 is designed to fabricate the parts in a neutral atmosphere without supervision.
"This process significantly reduces the manufacturing time required to produce parts from months to weeks or even days in some cases," said Andy Hardin, the integration hardware lead for the Engines Office in SLS. "It's a significant improvement in affordability, saving both time and money. Also, since we're not welding parts together, the parts are structurally stronger and more reliable, which creates an overall safer vehicle."
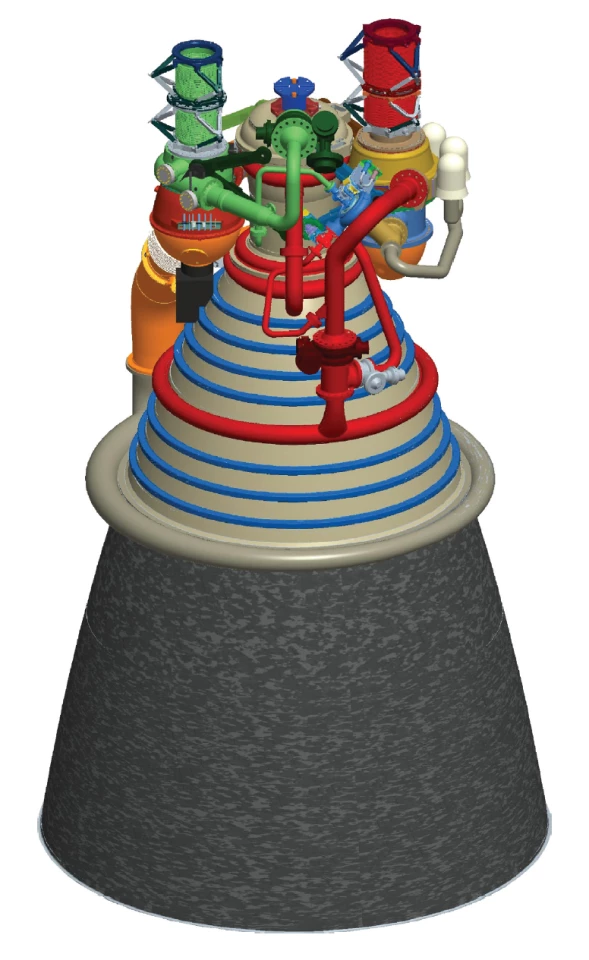
NASA plans to use the M2 to print engine parts for the J-2X engine, which is intended for the upper stage of the SLS. These parts will undergo structural and hot-fire tests and, if successful, will one day boost astronauts into space on missions to the Moon and beyond.
The first SLS unmanned developmental flight is targeted for the end of 2017.
Source: NASA