A first-of-its-kind 3D-printed concrete bridge has been unveiled in Venice, Italy. The bridge is a demonstration of a new 3D printing method resulting in a structure requiring no mortar or steel reinforcement.
The bridge was developed as part of a collaboration between ETH Zurich and Zaha Hadid Architects’ Computation and Design Group. The unreinforced structure was created by 3D-printing concrete blocks using a novel type of concrete ink produced by a company called Holcim.
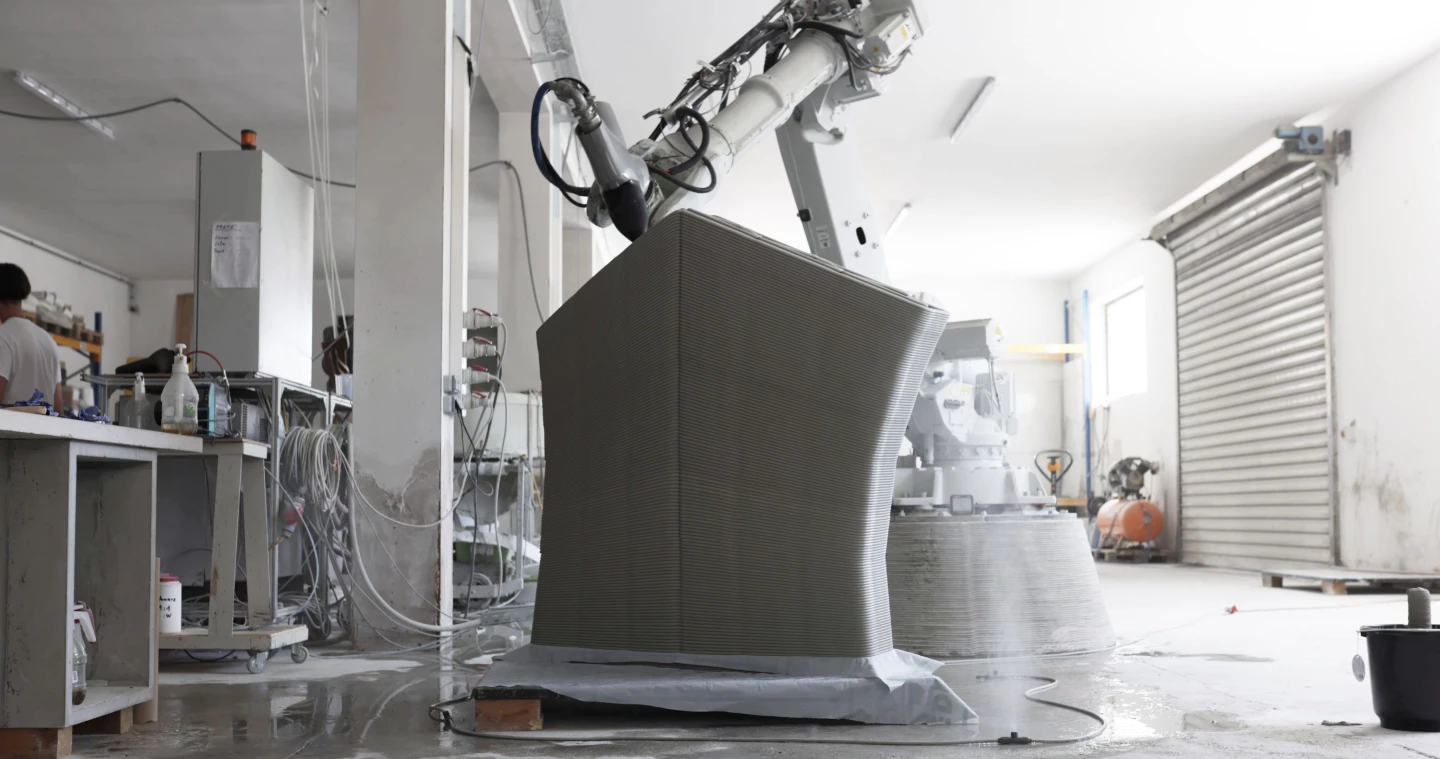
“This precise method of 3D concrete printing allows us to combine the principles of traditional vaulted construction with digital concrete fabrication to use material only where it is structurally necessary without producing waste,” explains Philippe Block, a researcher from ETH Zurich.
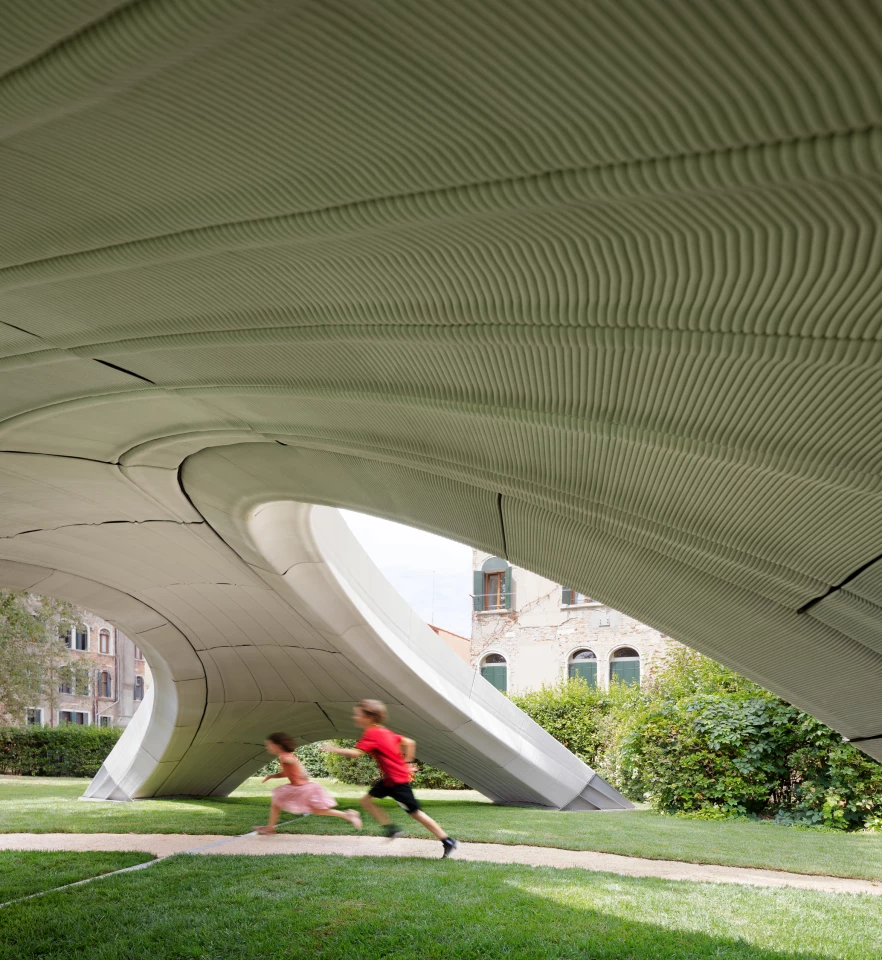
Shajay Bhooshan, from Zaha Hadid Architects, says the project is a fusion of ancient architectural techniques and modern computational design. The entire structure, dubbed Striatus, is held together through compression, with no reinforcements.
“Striatus stands on the shoulders of giants: it revives ancestral techniques of the past, taking the structural logic of the 1600s into the future with digital computation, engineering and robotic manufacturing technologies,” says Bhooshan.
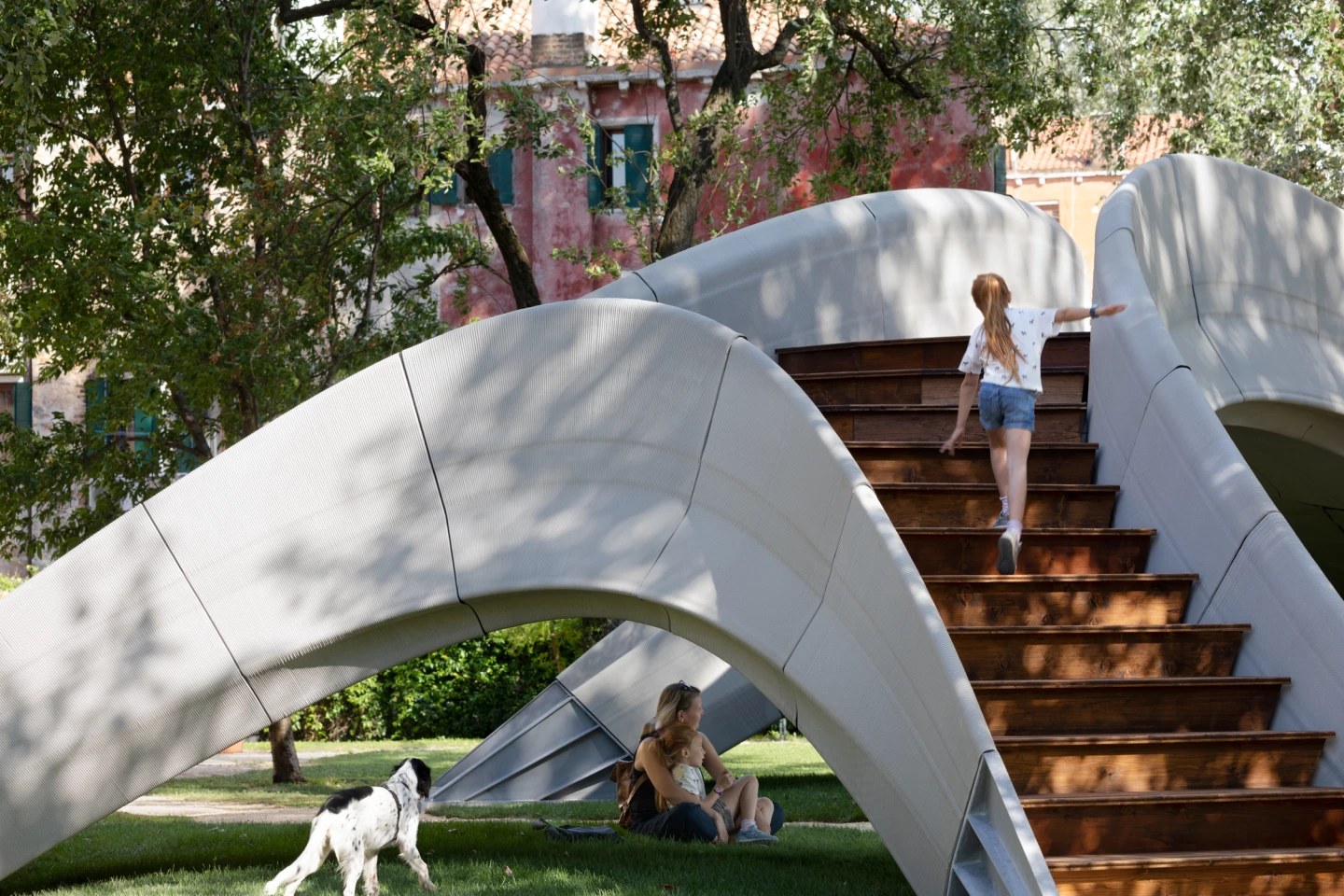
The structure can easily be dismantled and reassembled in a different location but is currently sitting at the Giardini della Marinaressa as part of the Venice Architecture Biennale. It will be there until November 2021.
The structure comes hot on the heels of another 3D-printed bridge recently installed over a canal in Amsterdam. That 3D-printed steel bridge was initially built in a factory in 2018 before being transported by boat and installed by crane into position this month.
Sources: ETH Zurich, Striatus Bridge