The Scottish company behind a novel heavy-lift utility UAV that uses an internal combustion engine and hydraulic motors has now frozen design plans and is preparing for production following successful flight tests in Denmark.
As we explained back in 2022, "gasoline engines, with their weird, peaky torque curves, aren't nearly responsive enough to keep a multicopter balanced against rapidly changing winds." Flowcopter's solution to this problem is to use an internal combustion engine to drive a hydraulic transmission system that in turn spins the rotor blades.
"This transmission technology gives the drone a high power to weight ratio allowing higher payloads to be delivered for longer distances," the company's Rob Menzies told us. "It also provides a high level of control to each of the four propellers."
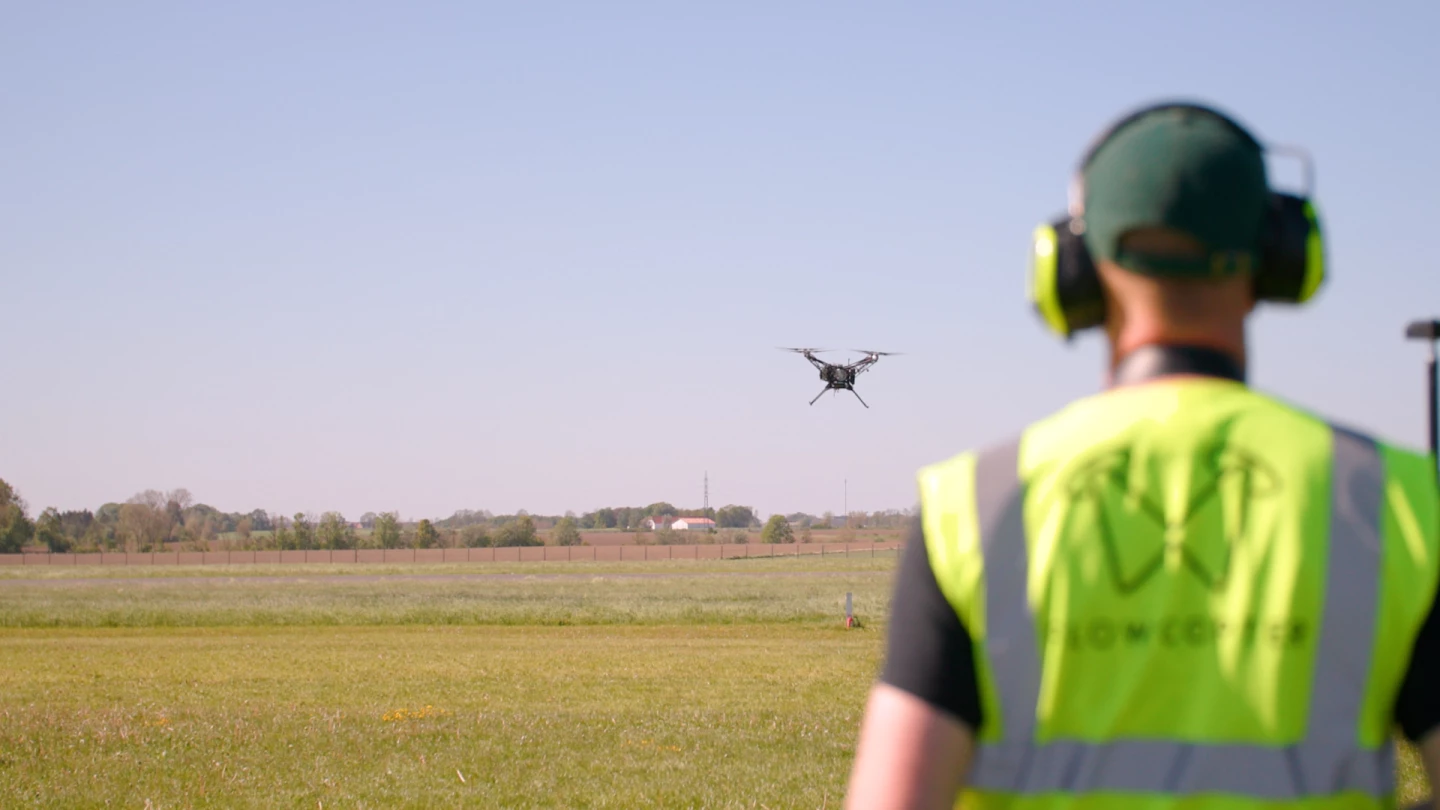
The original aim was to build a utility Unmanned Aerial Vehicle (uUAV) capable of flying for six hours on one tank of gasoline while hauling payloads of up to 150 kg (330 lb). Menzies told us that the FC100 that's just undergone successful flight testing at the Hans Christian Andersen Airport in Odense, Denmark, had a maximum take-off weight of 450 kg (992 lb) – including a payload of 100 kg (220 lb) – and a range of 100 km (62 miles).
This uUAV was part of an initial production run of three, with one already having been sold to "a major aerospace OEM." The next phase is already underway and will result in a heavy-lift multirotor capable of hauling a 200-kg (440-lb) payload – and it's this design that will "be the basis of our production run moving forward."
Larger aircraft are in the pipe too – with a variant able to heft more than 350 kg (771 lb) on track for development by the end of this year. In the meantime, Flowcopter is looking to secure flight test authorization for a UK demo by June. The video below has more.
Source: Flowcopter