Things don’t fall from the sky without a damn good reason. US lawyers Baum Hedlund, who specialize in litigation concerning transport accidents, lists human errors as the main reasons (53 percent) for aircraft crashes, followed by manufacturing defects (20 percent) and poor maintenance.
Take a Boeing 737, for example, that in 2011 lost a section of its roof while in flight. Test showed the Southwest Airlines 737-300 had “invisible” fatigue cracks in a metal joint and followed a 1988 incident when the roof of an Aloha Airlines 737 was ripped open and a flight attendant sucked out.
Metal fatigue is a fact of life across industries manufacturing items as varied as automobiles, wind turbines, household electrical appliances and bridges.
It has been fingered for a Norwegian oil rig failure in the North Sea (1980) that suffered the snapping of support cable, leading to the death of 120 workers; the Eschede train disaster (1998) that was caused by a carriage wheel shearing off and dislodging in the chassis, leading to a derailment and the collapse of a bridge over a roadway (101 deaths); and the mid-air breakups of two De Havilland Comet aircraft weeks apart in 1954 (46 deaths).
Then there is the Ponte Morandi bridge collapse in Genoa (2018); the Mianus River Bridge failure (1983) in Connecticut; the failure of a bridge in Latchford, Ontario (2003); and the San Francisco-Oakland Bay bridge in 2009. And a lot more.
It is a huge problem that scientist Kheang Khauv recognized when working with the Australian Department of Defence in the early 2000s, seeing the potential to produce a highly accurate, portable and compact alternative to using traditional mechanical strain gauges to test for metal fatigue.
Khauv’s Australian-based company is 1Millikelvin – the name refers to a tiny level of temperature – that is refining metal fatigue hunting using tiny infrared cameras to detect temperature changes in materials.
1Millikelvin’s technology is called MiTE – Microbolometer Thermoelastic Evaluation. It is in simple terms “stress imaging” and works by taking the images from the cameras combined with data processing tools to identify critical stress hot spots.
Minute changes of temperature in aircraft wings, refrigerator hinges, bridge cable pins and so on, can directly indicate changes in structural load which can betray the presence of metal fatigue and therefore warn of potential metal collapse and disaster.
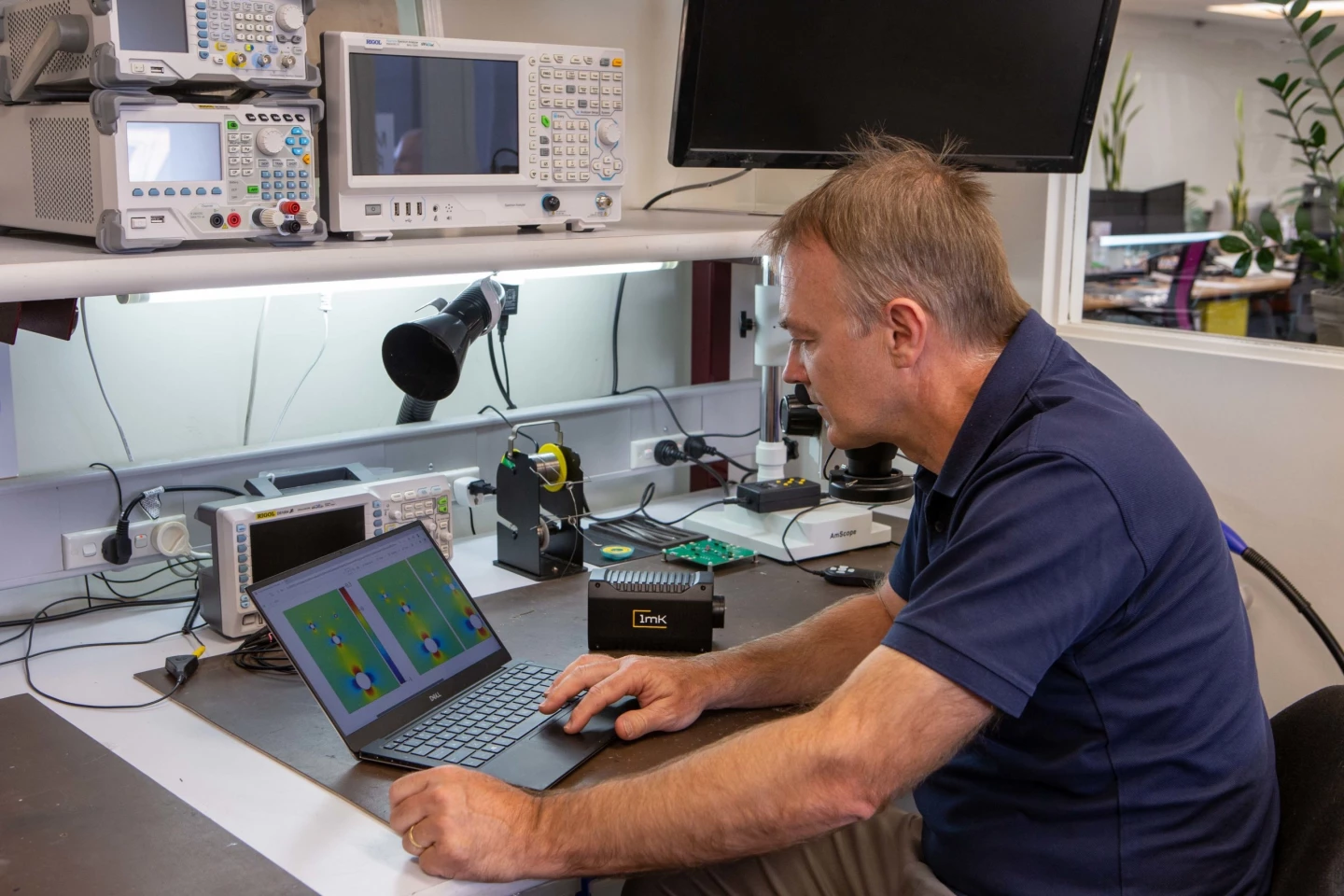
Khauv, now the managing director of 1Millikelvin, told NewAtlas that his company takes the raw data from the cameras (which are made by FLIR) and delivers the stress images as precise information that identifies structural loads and provides alerts of stress hotspots.
The camera’s small size makes the system portable while also lowering the cost of a technology that is generally regarded as being very expensive to buy and operate.
“Previously to resolve temperature changes of even 20 millikelvin required a big, bulky defence- or scientific-grade machine costing close to a $1 million, which only a scientist could operate,” says Khauv.
MiTE, once fully commercialized, is expected to cost between one-fifth and one-tenth of its nearest competitors.
Currently, the most common method of determining stress is by using mechanical strain gauges.
“The downside is they provide only a limited picture of the stresses, especially in complex structural components, and can’t image the stress, which means many stress hotspots can go undetected,” he says.
MiTE came about when Khauv was with global thermo-imaging company FLIR (only recently sold to Teledyne Technologies) and through working with the Department of Defence, he learnt the military-related applications of highly-sensitive infrared measuring equipment.
After leaving FLIR in 2014, Khauv started with LRM Technologies and incorporated thermo-imaging hardware with his own software in LRM’s spin-off business, 1Millikelvin.
“In 2016 we went to the Department of Defence and signed a formal agreement to commercialize the stress-imaging concept,” he says.
“Defence came up with the core algorithms and proof-of-concept and we identified the bigger picture of how the technology could be used elsewhere and in a form that is easy to use.”
He says that a few planets had to align for the technology to work. There was the agreement with Defence, and also the arrival of cost-effective and very small cameras onto the market.
“Without the small cameras, the cost to get a system going was so large that it could outweigh the benefits,” he says.
Compact and numerous cameras can be placed over the subject – such as an aircraft fuselage or wing – and data can be collected from different points as the part is subjected to stress forces.
The ramifications are huge. Khauv says the 1Millikelvin technology shows what complex parts will do when placed under stress and, importantly, before they are deployed in the field.
“In the future we see new aircraft designs using this system,” he says. “Aircraft manufacturers mostly rely on conventional single point strain gauges to determine stresses which, because of limitations in this old sensor technology, leaves many blind spots. Our system can provide high-fidelity stress imagery of a complex 3D part. We can move through an aircraft, covering parts sequentially or – given enough cameras – inspect and monitor them all at the same time.”
Khauv says a forerunner of his technology has already been used to analyze stresses in a Lockheed Martin F-35 aircraft.
The same scenario for the device can be applied to buildings and bridges that can be tested in-situ for stress zones.
“Now, for us, we have to inform people that this stress imaging capability exists,” he says. "We know that the technology works in aerospace and aviation but we want people to know that the technology is applicable to other fields, including for example to check train tracks and rollercoasters."
Khauv says that collaboration was vital for 1Millikelvin to succeed.
“Without it we would only have a great idea and nothing more, commercially speaking,” he says.