Hypersonic aircraft that fly many times the speed of sound might one day carry people from the US to Australia in just a few hours, but with all that velocity comes a hell of a lot of heat. One way scientists hope to prevent them overheating is by having the propellant do double duty as a coolant, keeping aircraft at safe operating temperatures as they blaze across the sky. Newly developed 3D-printed catalysts could be the missing piece to this puzzle, with lab tests showing how they can trigger the necessary chemical reactions for highly efficient heat absorption.
While the frigid temperatures of high-altitude are enough to keep commercial aircraft from overheating, it is a different story for planes traveling at hypersonic speeds of more than 6,100 km/h (3,790 mph), where friction between the aircraft and outside air generates tremendous amounts of heat. Since the 1960s, studies have explored the idea of tackling this problem through what are known as endothermic fuels, which would act as both the propellant and the aircraft's primary coolant.
In this scenario, a heat exchanger of some kind would capture heat from warming parts and transfer it to a cool hydrocarbon fuel. As that fuel warms up and hits a certain temperature, it triggers chemical reactions that break the hydrocarbons apart into simpler units, which can then be used for propulsion.
“Fuels that can absorb heat while powering an aircraft are a key focus for scientists, but this idea relies on heat-consuming chemical reactions that need highly efficient catalysts,” says first author Roxanne Hubesch, from Australia's RMIT University. “Additionally, the heat exchangers where the fuel comes in contact with the catalysts must be as small as possible, because of the tight volume and weight constraints in hypersonic aircraft.”
In search of a solution to this problem, Hubesch and her colleagues used 3D printing to produce lattice structures made of metal alloys that were coated in synthetic minerals called zeolites. The team describes these as miniature chemical reactors, and put them through laboratory tests designed to mimic the extreme temperature and pressure fuels endure at hypersonic speeds. This revealed that as the structures heated up, some of metal, most likely chromium, migrates into the zeolite framework, resulting in "unprecedented catalytic activity."
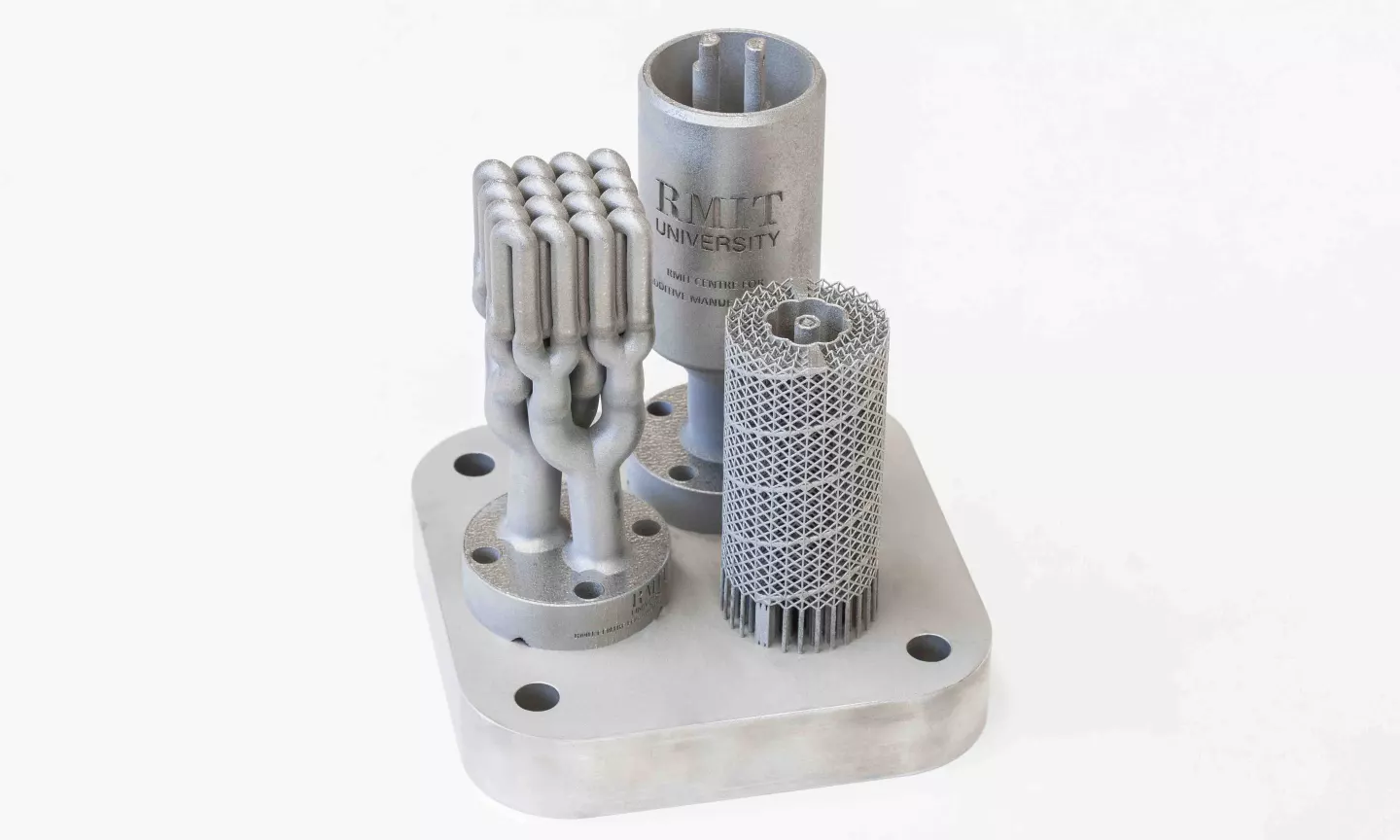
“Our 3D printed catalysts are like miniature chemical reactors and what makes them so incredibly effective is that mix of metal and synthetic minerals,” Hubesch says. “It’s an exciting new direction for catalysis, but we need more research to fully understand this process and identify the best combination of metal alloys for the greatest impact.”
The team produced a variety of 3D-printed catalysts in experimental formats, but there is a lot of work to do before we see them go to work in next-generation aircraft. The scientists will now use X-ray synchrotron techniques among other methods to study their function in greater detail and optimize their performance.
“Our lab tests show the 3D printed catalysts we’ve developed have great promise for fueling the future of hypersonic flight,” says lead researcher Dr Selvakannan Periasamy. “Powerful and efficient, they offer an exciting potential solution for thermal management in aviation – and beyond. With further development, we hope this new generation of ultra-efficient 3D printed catalysts could be used to transform any industrial process where overheating is an ever-present challenge.”
The research was published in the journal Chemical Communications.
Source: RMIT