One of the most exciting possibilities of 3D-printed architecture is that it could revolutionize affordable housing. Portugal's Havelar shows this may soon be within reach with its inaugural 3D-printed home, which took just 18 hours to print.
Located in the Greater Porto area of Portugal's second-largest city, the unnamed 80 sq m (roughly 860 sq ft) two-bedroom residence was built using COBOD's BOD2 printer, which was also used on Europe's largest 3D-printed building. According to COBOD, Havelar's houses can be produced for €1,500 per sq m, which it contrasts favorably with the Porto average of €3,104 (around US$3,330) per square meter. This cheaper price tag is largely due to the speed of construction offered by the 3D printer, which follows a blueprint and extrudes a cement-like mixture out of a nozzle in layers, building up the basic structure of the home.
Though, as mentioned, the printing process itself took 18 hours, human builders then came in and finished it by installing the windows, door, paneling, roof, and anything else needed. Including the human labor, the entire project took under two months to complete.
The home takes the form of a simple single-story residence defined by the telltale ribbed walls that show that it has been constructed with a 3D printer. Its interior is arranged around a central kitchen and dining room, with the living room, two bedrooms and bathroom adjoining. It's obviously relatively basic compared to other 3D-printed houses we've seen, like the more high-end Wolf Ranch models, though it's also around $400,000 cheaper, so is focused toward a totally different market.
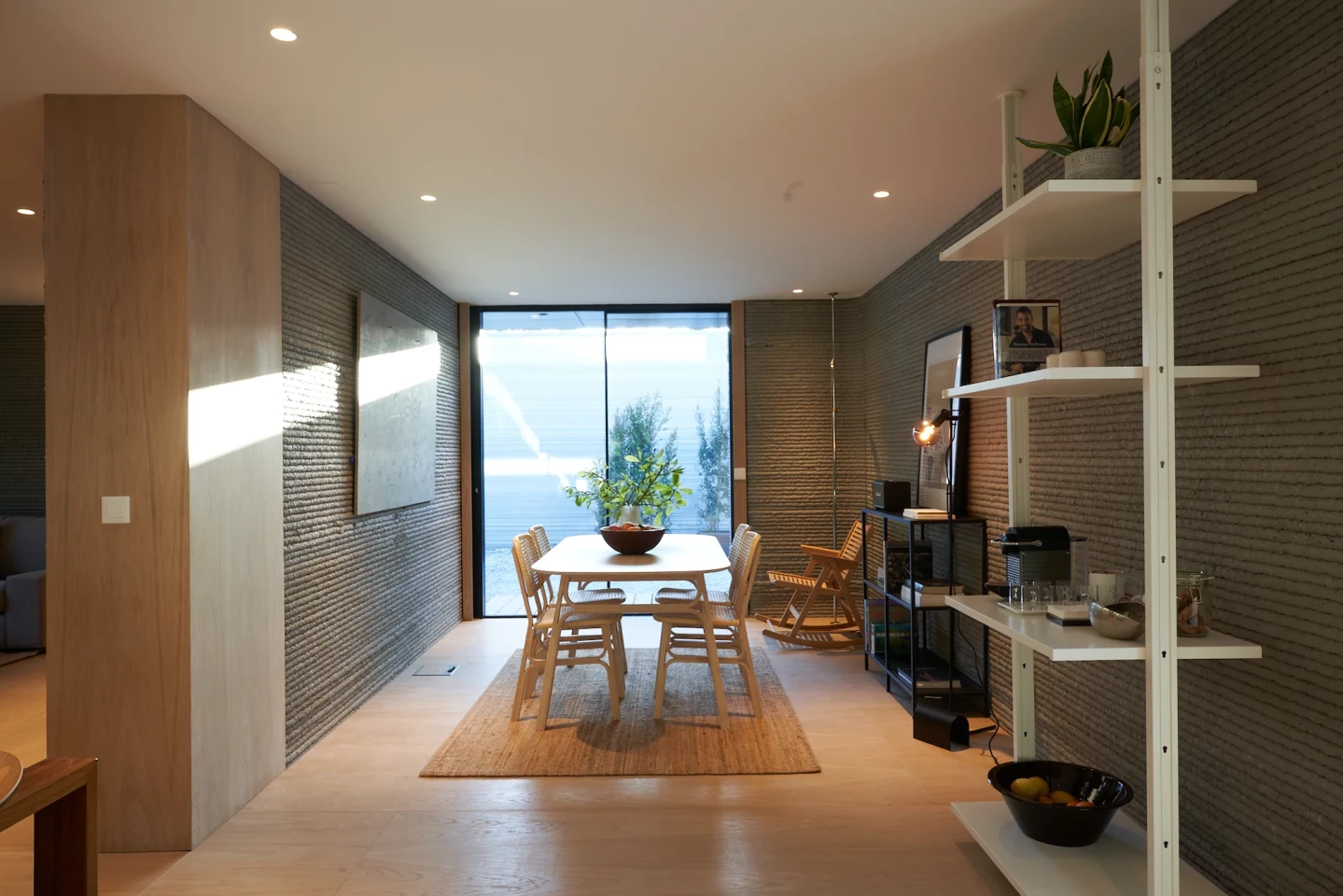
This is the first 3D-printed home Havelar has produced, so it's early days yet, but looking to the future, the firm hopes to scale up production and reach carbon neutrality by 2030 by adopting alternative construction materials like earth and straw.
"We want to team up with partners who see themselves in building sustainable and accessible communities," said Rodrigo Vilas-Boas, Co-Founder of Havelar. "With €150,000 [$161,000], it's possible for a young couple to have the home they've always dreamed of, in an area with good access and services."