In just a few short years, 3D printed architecture tech has matured from producing basic hut-like homes to creating a community of low-cost housing. Another interesting development in this area comes from Kamp C in Antwerp, Belgium, which recently built a prototype 3D-printed house with two floors using what it calls Europe's largest 3D printer.
The unnamed project measures roughly 90 sq m (around 970 sq ft) and is the first 3D-printed house we've seen with two floors, though we have previously reported on an office building that also had two floors. It was constructed using a COBOD BOD2 printer measuring 10 x 10 m (32 x 32 ft) and, as with other 3D-printed projects, the construction process involved extruding a special cement-like mixture out of a nozzle and building up the basic structure in layers until it was complete. Human laborers then came in and put the finishing touches in place, like the roof and windows, for example.
It was completed on-site over three weeks but Kamp C reckons this could be reduced to as little as two days in the future.
"The material's compressive strength is three times greater than that of the conventional quick build brick," explains Marijke Aerts, the project manager. "Besides the fibers in the concrete, the amount of wire-mesh reinforcement used is extremely limited. As a result of the printing technology used, formwork was redundant, saving an estimated sixty percent on material, time, and budget."
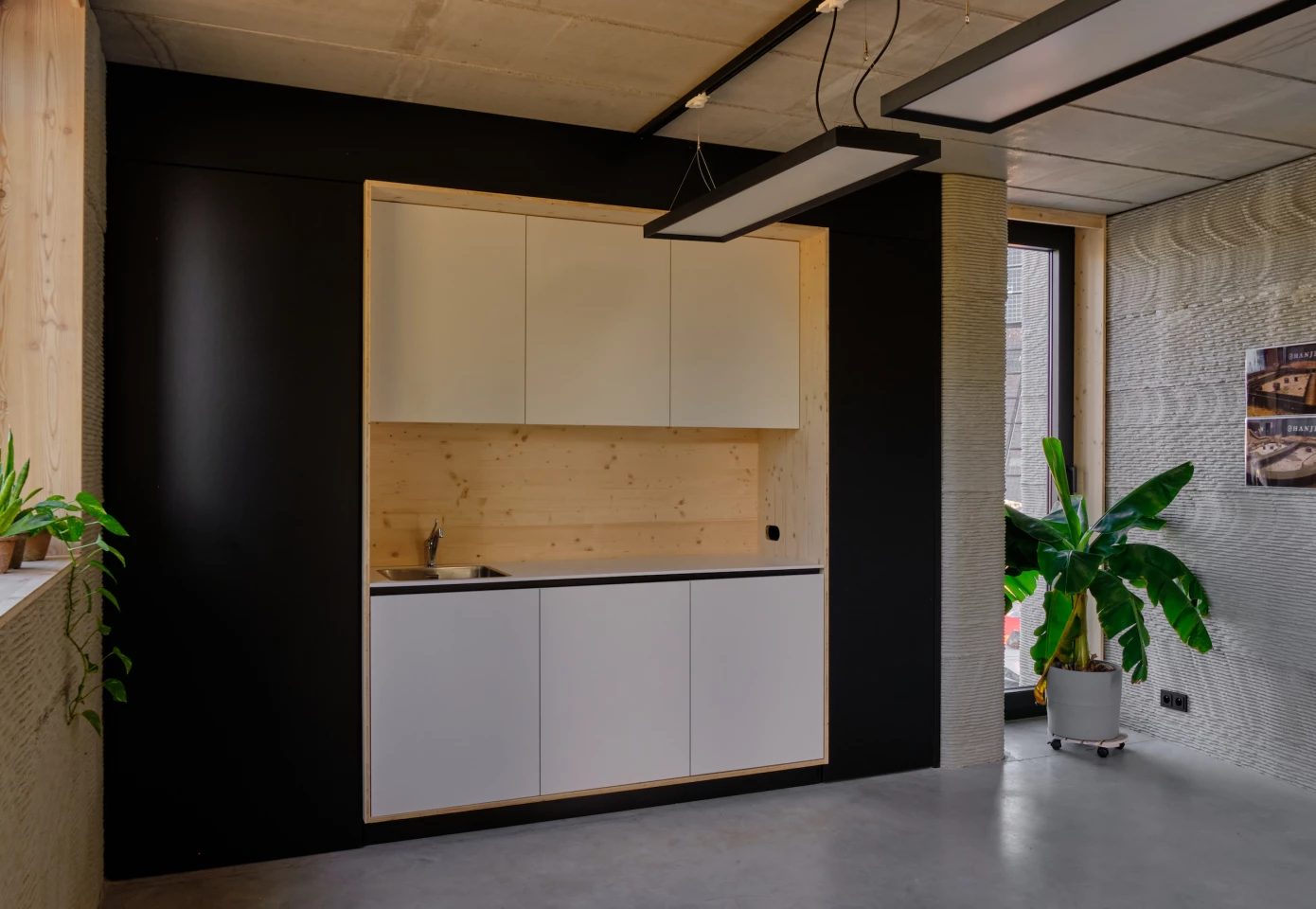
The interior of the prototype home has similar dimensions to a typical Belgian house, though is not actually going to be lived in as it was created for government-funded research purposes and to highlight the possibilities of 3D printed architecture. It includes an entrance hall, two conference rooms, and a kitchen area. Kamp C also added some sustainable and energy-saving extras too, such as underfloor heating, solar panels, and a heat pump. A green roof is planned for the future.
If you're in the Antwerp area and would like to check out the project in person you can do so during July and August by making an appointment through Kamp C's website (in Dutch).
Source: Kamp C