Camcon's Intelligent Valve Technology (IVT) replaces the camshaft with electric actuators for full, precise digital control over the air charge of any engine. Now, the company's focus is shifting from cars to heavy diesels and artificial intelligence.
When we last caught up with the Camcon team in 2018, they were entirely dedicated to getting digital valve technology into the passenger car market. With total control of when the intake and exhaust valves open and close, and indeed how far they lift, Camcon felt that the performance, efficiency and emissions reduction benefits would be highly attractive to automakers.
It hasn't worked out that way, for a few reasons. Firstly, the industry is torn over the future of the powertrain altogether, with electric, hybrid and hydrogen beginning to draw focus away from combustion engines. In such an environment, people have been wary of spending too much on revolutionary combustion engine technology that's yet to prove itself at scale.
Secondly, adopting a digital valve train introduces a deluge of new variables that engineers can play with. There might be all sorts of benefits available, but getting to them requires an incredible amount of configuration work across engine speeds, temperatures, different loads and different circumstances that might call for different priorities.
And finally, while mechanically-minded folk might find digital valves fascinating and immediately understand their significance, the average mass-market car buyer is probably much more interested in the shape, how many cup holders it has, or what colors there are, than what innovation lies under the hood. Whatever the reasons, Camcon has found it a tough sell.
The company is working in three directions to push things forward: it's building plug and play valve train kits for a range of common single-cylinder research engines, it's opening up to the heavy-duty diesel (HDD) market, and it's assembling a machine learning team to start applying artificial intelligence to the complex task of calibrating the IVT for a given engine and set of performance outcomes.
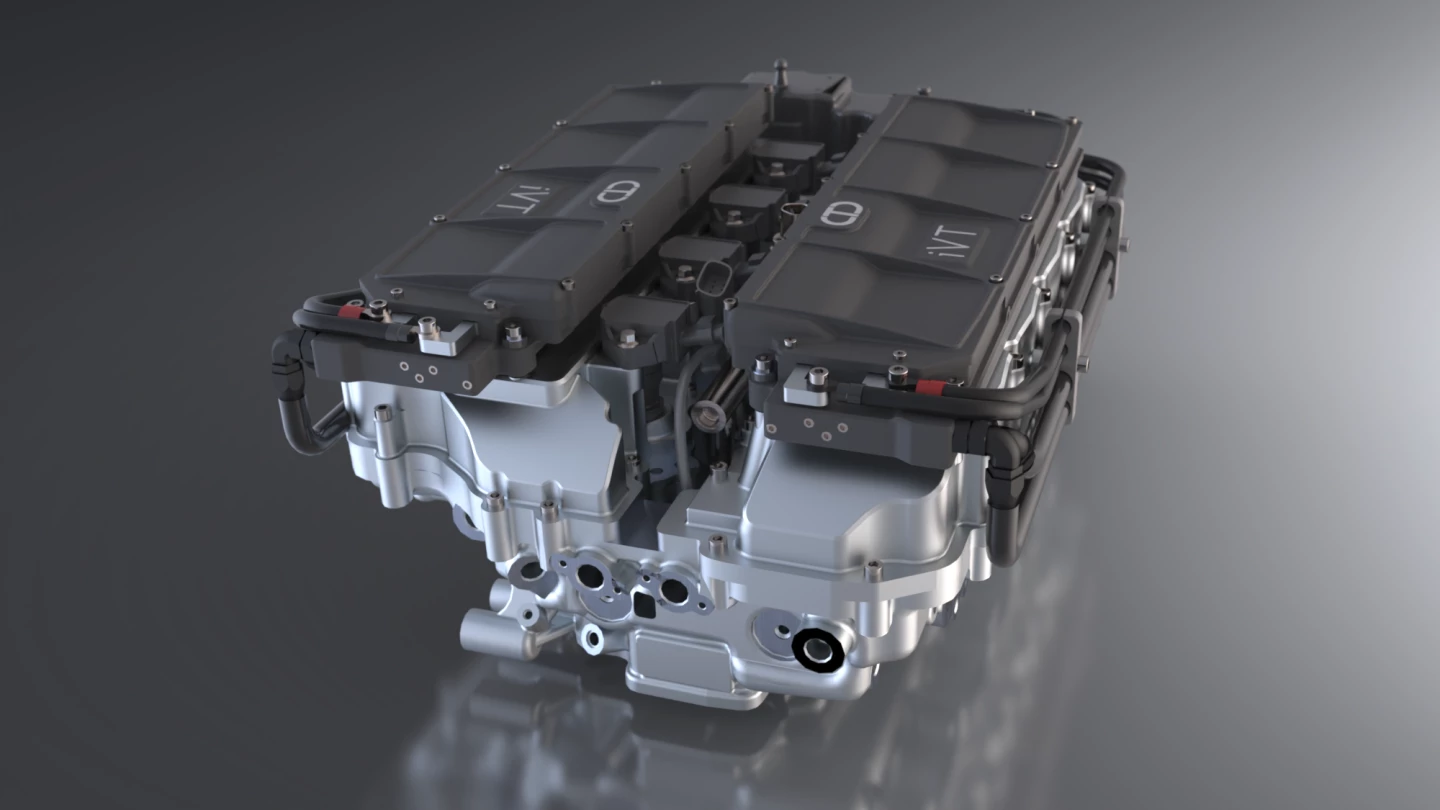
Valve kits for research engines
Camcon has begun producing IVT top ends that fit straight onto common single-cylinder research engines used in engine development across the industry, making it as easy as possible for manufacturers to get their hands on the technology and start working with it.
It's not just for companies looking to work with digital valve technology, though; it can actually radically speed up an automaker's development and testing process, whatever it is they're working on, because you can change cam profiles at the touch of a button instead of shutting everything down, tearing the engine down, putting in new camshafts and getting it all back up to temperature again.
There's already one such unit installed in the research labs of a tier one company, with half a dozen more coming in the next year. Not a bad start, considering that there are only 500-odd of these research engines in use worldwide.
Intelligent Valve Control for heavy diesel trucks
While Camcon has been banging on the doors of automotive giants, the team has found that the bulk of its incoming enquiries have been from the trucking sector – a market Camcon COO Mark Gostick tells us the team hadn't considered at all, and which appears to be in need of some innovative solutions.
"They're starting to come under the same kinds of regulatory pressures that the passenger vehicles have been," Gostick tells us over a Skype call. "They've got to find ways to clean up their act, less in terms of CO2, and more in terms of other particulates, NOX, these kinds of things. It's got to a state where the amount of after-treatment gear they're fitting on to the engine costs more than the engine itself."
The IVT solution, says Camcon Technical Director Roger Stone, can significantly reduce the size, weight and cost of the after-treatment equipment fitted to a big diesel engine. "We can use our system to better control the exhaust after treatment kit temperature. We can maintain it at its optimum operating temperature over a greater proportion of the drive cycle. We can't eliminate that equipment, but we can reduce the size and cost and weight."
As a bonus, the IVT system can be configured to provide an engine braking capability to completely replace the 375-odd-pound (170 kg) specialized engine brake system fitted to many trucks. And on top of those impressive weight savings, the team is confident it can deliver a significant reduction in fuel use.
"In terms of fuel efficiency," says Gostick, "we can't make as big an impact as we can with petrol in a passenger car, but we reckon we can do about five percent in terms of straight fuel economy on a heavy duty diesel. When you're spending the better part of a million Euros on fuel over the lifetime of the vehicle, that's a significant change to your operating costs."
The trucking market, Gostick believes, requires such long ranges and fast turnarounds that it's unlikely to go fully electric any time soon. "We still believe we'll make it in the passenger car space. But in the heavy duty trucking market, electrification seems a lot further off, if it ever happens. So anything you can do to improve the state of things in the HDD market right now is attractive."
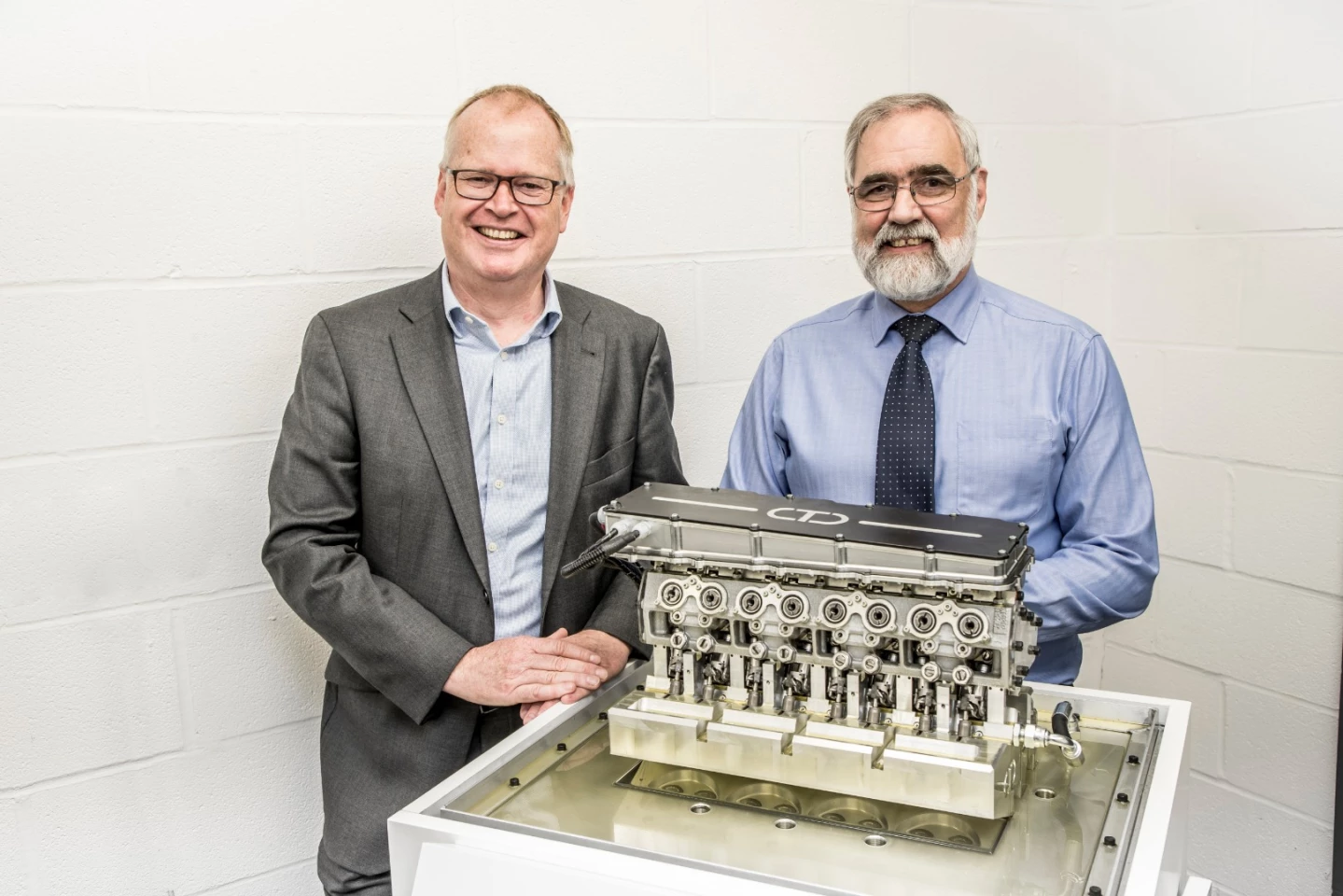
Investing in artificial intelligence
Achieving the many benefits of total digital valve control is proving to be no walk in the park. While there are only three things to think about – when you open the valve, how high you open it, and when you close it – tailoring those values to maximize power, efficiency and emissions factors across the complete range of engine speeds, temperatures, combustion conditions and situations is a grueling job.
That's before you start playing any tricks like running an engine as a two-stroke for a power boost, or as a 12-stroke for efficient, temperature controlled cruising, or messing around with GPS data to prioritize NOX emission reduction in town, but CO2 emission reduction when you're in the middle of nowhere – all of which are possible with the IVT system.
Camcon has decided the best way forward might be to handle the software and calibration side of things itself, using the power of artificial intelligence to speed the process along and improve outcomes while reducing a big barrier to entry for its customers.
"Just giving the customers the system creates a problem, so we're going to solve that problem, too," says Gostick. "We're looking at the application of artificial intelligence and neural networks, to sit alongside the calibration work of the engine on the test bed and help optimize the operation of the engine. So, you've got digital control of the fuel injection and the spark, you've now got digital control of the air, so if you could use machine learning in the test cell with the engine, you can set it up to try to optimize for what you want in an intelligent way. You might even be able to integrate it into the vehicle at a later stage.
"People in engine consultancies have been trying to do this sort of thing for a while now, but they haven't had the closed-loop tools, the digital control of the air. So we're out in the market now, trying to raise a lot of money. Not only do we have to make the system, we have to do the solution. Our future is probably more as a software company than a hardware company."
In this vein, Gostick says Camcon is considering doing an open license for its hardware, letting anyone manufacture and supply it while the company focuses on the calibration work, acting as a consultancy. This would get around another problem: the fact that auto manufacturers will only buy production-grade hardware from recognized, trusted suppliers.
The full electrification of transport, say Gostick and Stone, is further away than people are projecting. And as long as combustion engines remain in the mix, it makes sense to push ICE technology to be as efficient, clean and intelligent as possible. We'd sure love to see what kind of impact this gear can make.
Source: Camcon