With their big ugly welds, aluminum-framed mountain bikes generally aren't quite as pretty as their carbon fiber or titanium counterparts. That said, the German-made Frace F160 is a huge exception, as its frame is milled from a solid block of aluminum.
The F160 was initially created by Bernd Iwanow, who previously worked as a CNC machine operator and production manager.
"Two years ago I got an order to help design a bike and then mill two prototypes," he tells us. "When the construction was finished and we had milled the first parts, the company filed for bankruptcy. So I stood there with my many ideas and could not implement them ... The idea was born."
Since he's not a mountain biker himself, Iwanow proceeded to have two pro riders try out his prototypes. Their feedback was reportedly quite positive, leading to the current fifth-generation version of the F160 that is now slated to enter limited production.
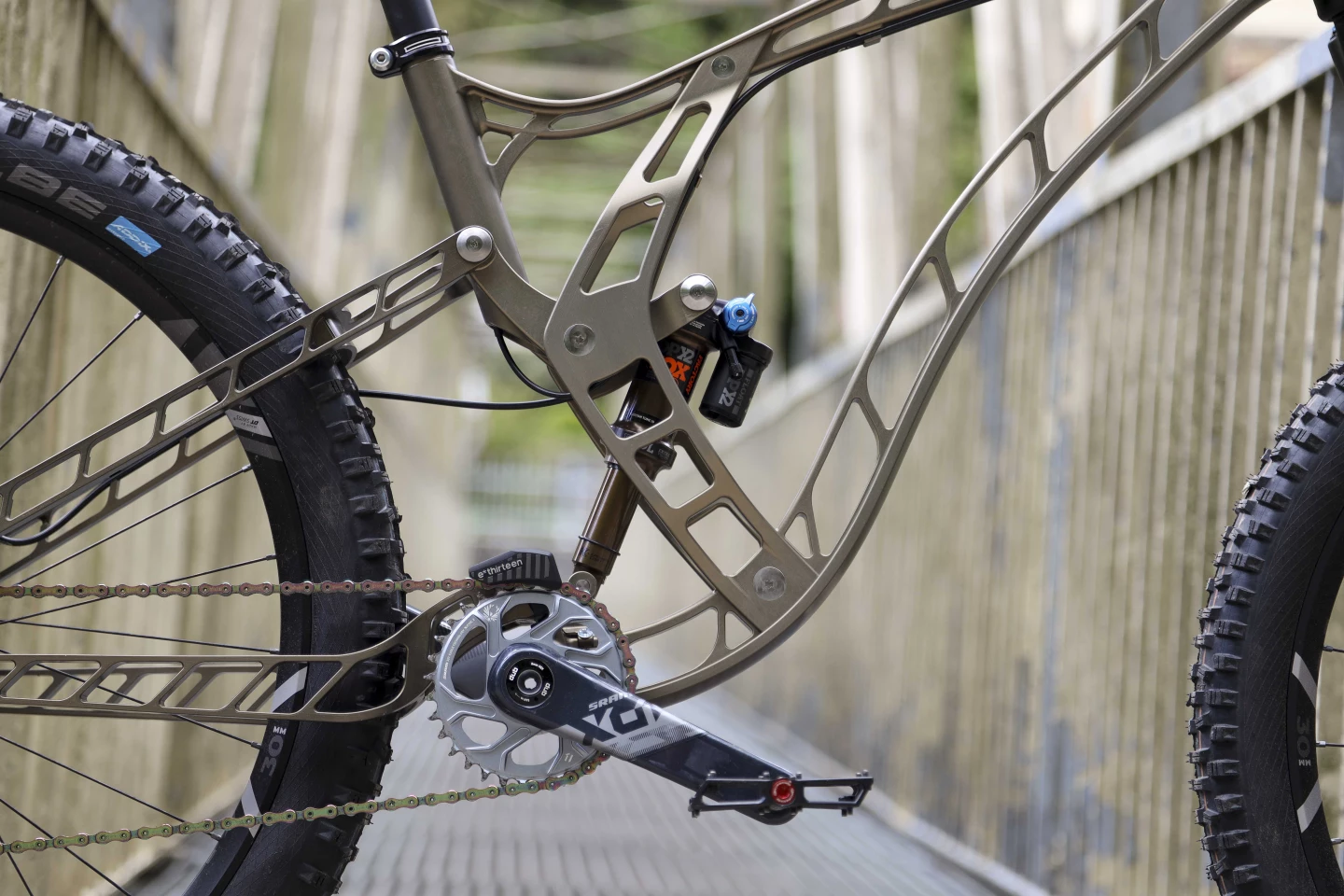
Each frame begins as a 70-kg (154-lb) slab of 7075 aluminum, which isn't weldable but is very stiff. That slab gets machined into eight separate segments, which are subsequently joined together using titanium screws (it should be noted that Pole Bicycles does also manufacture milled aluminum frames, although they're made of two halves that are glued together).
The resulting frame has passed strength and fatigue tests conducted by Germany's EFBE bicycle-assessment group, and it certainly is pleasing to the eye. With a complete 27.5-inch-wheeled dual-suspension bike tipping the scales at a claimed 16.3 kg (36 lb), the F160 won't be the lightest bike on the trail – but definitely one of the coolest-looking.
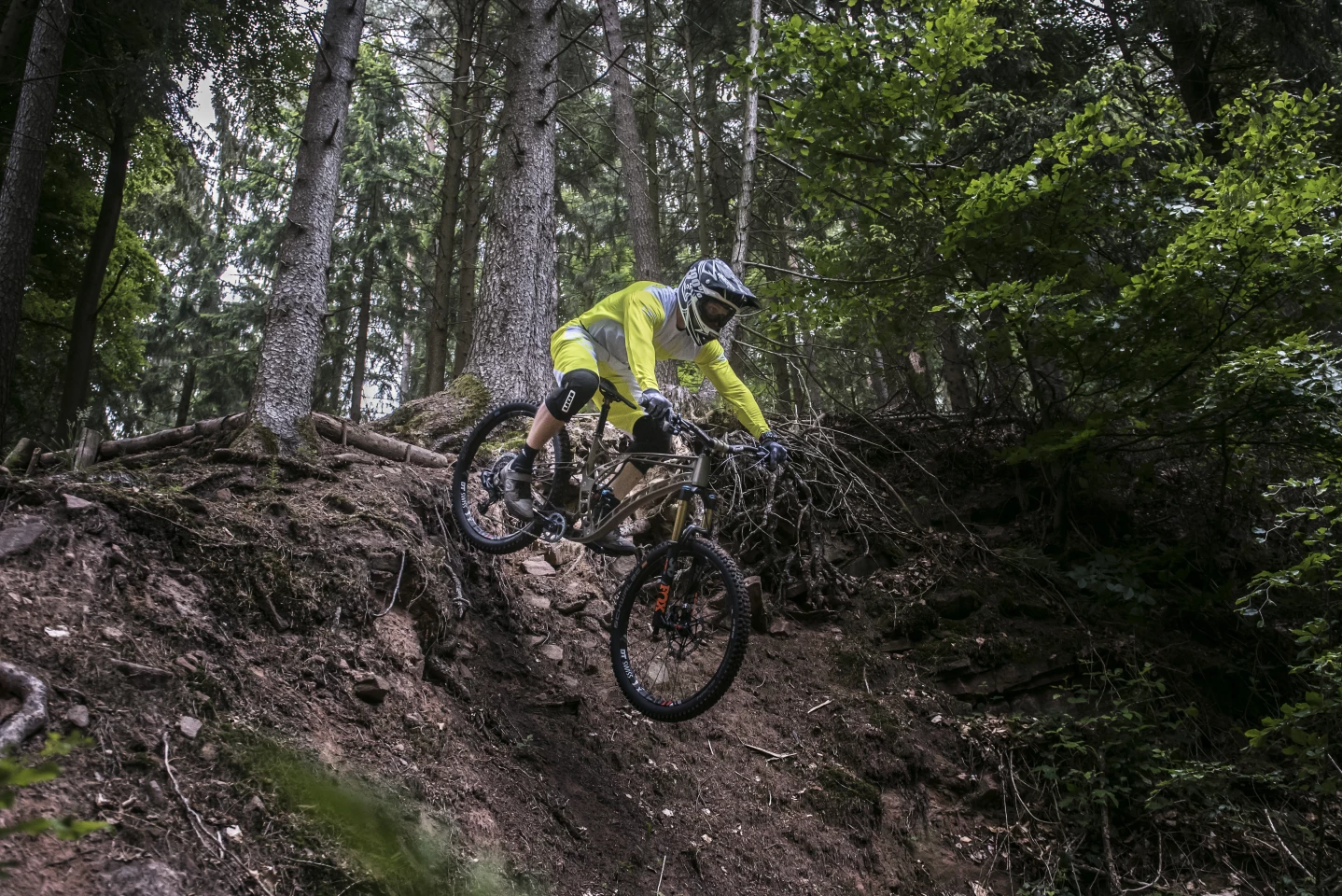
Plans now call for production and sales of frames to begin next month, with first deliveries following in September. Availability of complete bikes should commence in October. Iwanow tells us that he hopes to manufacture 50 frames per year, each one priced at €5,000 (about US$5,612). Complete bikes will cost between €7,500 and €12,000 ($8,419 and $13,472), depending on the components.
And should anyone be interested, Bernd is presently looking for a North American distributor of his frames. He can be reached via the Source link below.