For vehicles like ebikes, belt drives offer a smoother, zero-maintenance alternative to chain drives. The Shift Drive system takes the technology further, by allowing riders to shift between two gears – plus it works on unmodified bicycle frames.
Currently the subject of a Start Engine investment-seeking campaign, Shift Drive was created by California-based belt drive manufacturer Veer.
The setup incorporates the company's existing Split Belt. Unlike traditional drive belts which come pre-made in the form of an uninterrupted loop, the Split Belt starts out as one long strip. Once it and the rest of the Veer drivetrain have been installed on the bike, the two ends of that strip are riveted together so that it then forms a loop.
The big advantage of this system lies in the fact that when the Split Belt eventually wears out, it can just be pulled apart and replaced with another that's simply put in and looped up.
By contrast, in order to allow for the replacement of a conventional pre-looped belt, a bike must have a removable section built into its drive-side seat stay. Otherwise, there would be no way of getting the new belt onto the drivetrain in one properly tensioned piece.
Another disadvantage of traditional belt drives is the fact that because they can't incorporate derailleurs, the belt drivetrain itself can only offer a single gear ratio. In order to provide more gears, a third-party hub or bottom bracket gearbox must be added to the mix – although that adds weight, complexity and expense.
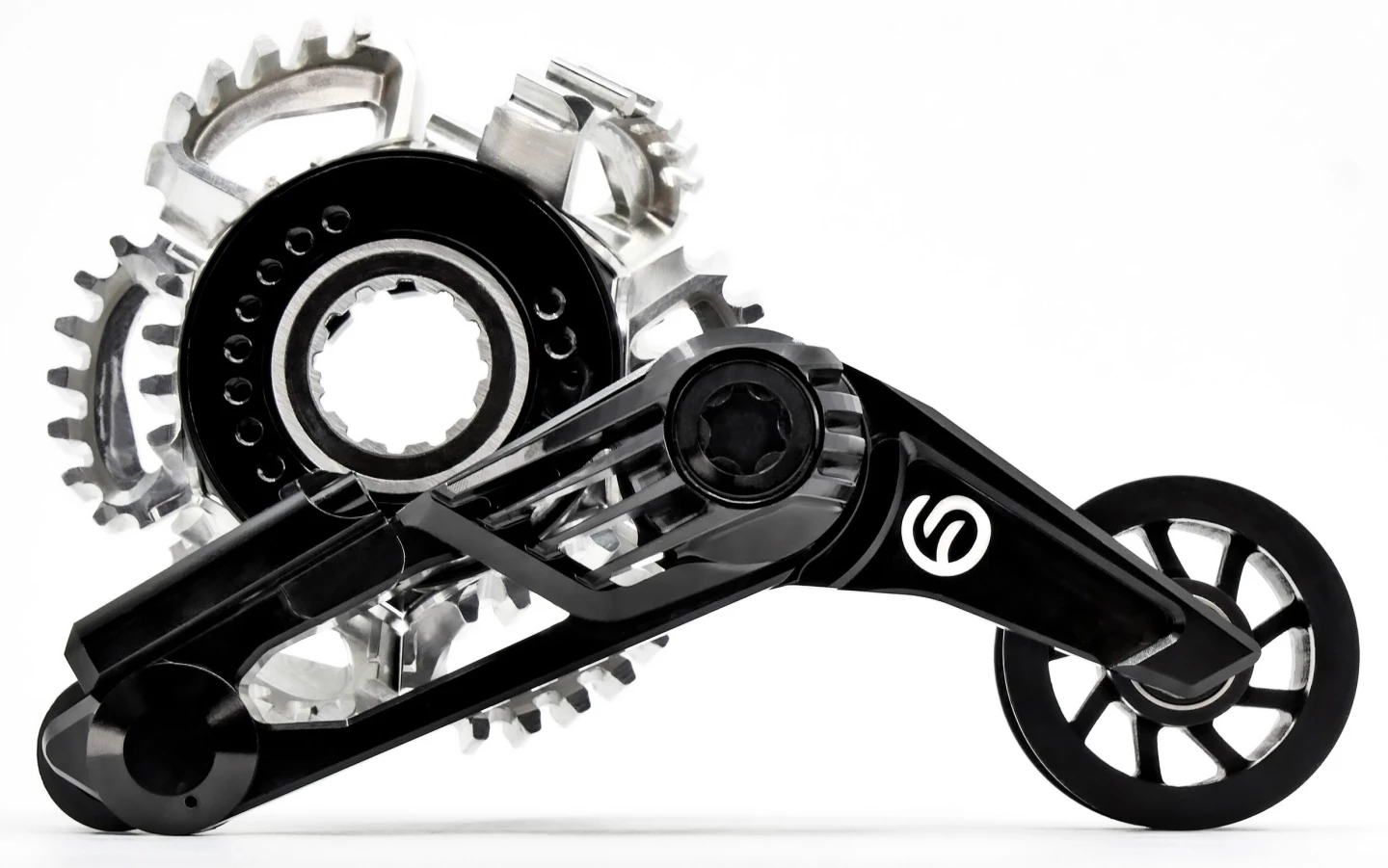
Shift Drive instead utilizes a rear cog that incorporates several separate sprocket-toothed elements arranged side-by-side to form a ring. Each element can independently swivel 180 degrees relative to the underlying cog body, in order to place either a taller or shorter side of itself directly beneath the belt.
By having all of the elements sequentially swivel in the same direction, it's thus possible to increase or decrease the diameter of the cog – or at least, the part of it that the belt engages. A clutched-spring tensioner wheel located below the cog automatically takes up the belt slack as needed.
It's difficult to describe how the system works in written words, but you can see it in animated two-geared action in the video at the end of this article, starting at the 01:18 mark.

Veer founder Sean Hacking tells us that while an electronic micro-servo initiates each gear-shift, the actual swiveling of the segments is driven solely by the rotation of the hub. The shifts can be manually triggered via a handlebar-mounted remote, or they could be automatically triggered via a pedaling torque sensor.
What's more, Shift Drive can be used along with any third-party geared hub that has a standard 9-spline freehub body, thus doubling the total amount of gears available. That said, Veer is working on adding additional gears to the Shift Drive system itself.
Hacking says that the technology should start showing up on production ebikes – and possibly other light electric vehicles – as of next summer (Northern Hemisphere). Prospective commercial partners can get in touch with him via either the Start Engine campaign or the company website.
Source: Veer