In June, Boeing’s new 737 MAX single-aisle airliner began wing assembly in Renton, Washington. Since then, the first fuselage arrived from Wichita, Kansas, and is now undergoing final assembly, which includes installation of a new advanced winglet designed to improve fuel efficiency.
The fuselage arrived by rail on August 21 and after installing flight systems and insulation blankets the mechanics have moved on to attaching the wings to the body of the first test aircraft.
This assembly is more than just a milestone in the building of a new class of passenger aircraft. It also acts as a testbed for new assembly methods that, if proven, will be introduced at two other Renton assembly plants as 737 MAX production expands.
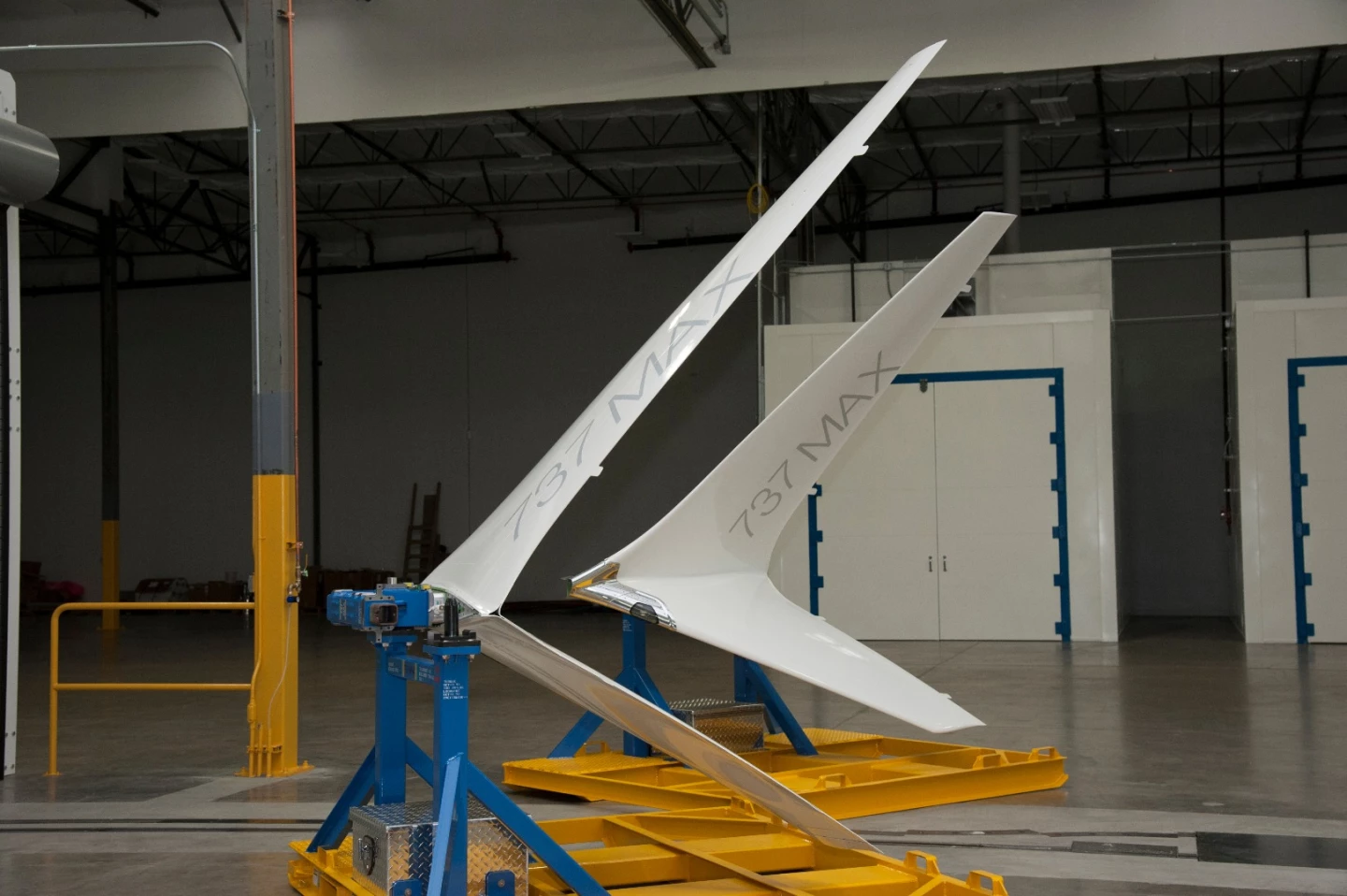
In addition, the first 737 MAX sees the introduction of Boeing’s new Advanced Technology winglets, which the company says increase fuel efficiency by 1.8 percent over conventional winglets by capturing more air as it flows off the tip of the wing and turns it into lift.
An in-house design exclusively for the 737 MAX, it's based on the blended winglet used in the 737 NG and the raked winglet of the 777. Instead of a much larger winglet, it splits the area into two to create a dual-feather design. This allows for greater efficiency without greatly increasing the size and weight of the winglet.
Boeing says the design has undergone wind tunnel tests in Farnborough and Seattle with positive results and this first test aircraft will see the winglet fly for the first time.
The 737 MAX is scheduled for rollout later this year, with the first flight in 2016 and the first customer delivery in 2017. Boeing reports that it has orders for 2,869 of the aircraft from 58 customers.
Source: Boeing