The name Bugatti is associated with bleeding-edge motor cars rather than 3D printing, but the automaker has announced it has produced a new brake caliper that is not only the largest in the motor industry, but is the largest component to be printed from titanium alloy. The product of a joint effort by the Bugatti Development Department and Laser Zentrum Nord in Hamburg, the eight-piston monobloc brake caliper may one day lead to auto components that combine superior performance with faster, cheaper production.
The development of hypercars like the Bugatti Veyron and Chiron may be pushing the envelope of automotive performance, but it's also forcing the development of vehicle components and the materials used to make them. One example is the brake design used on the Chiron, the calipers for which are the largest installed in any production car and were designed using bionic principles. They're forged from high-strength aluminum alloy and contain titanium pistons – eight for the front brakes and six for the rear.
The new calipers are meant to combine minimum weight with maximum stiffness, but Bugatti felt there was room for improvement, so the company's engineers came up with another version made entirely of an aerospace titanium alloy called Ti6AI4V, which is normally used in highly stressed undercarriages, wing components, and jet and rocket engines.
According to Bugatti, calipers made from titanium would have a tensile strength of 1,250 N/mm² (125 kg/mm²). In addition, the titanium caliper, measuring 41 x 21 x 13.6 cm (16 x 8 x 5 in) and with walls only one to four mm thick, would weigh only 2.9 kg (6.4 lb), as opposed to an aluminum version's 4.9 kg (11 lb).
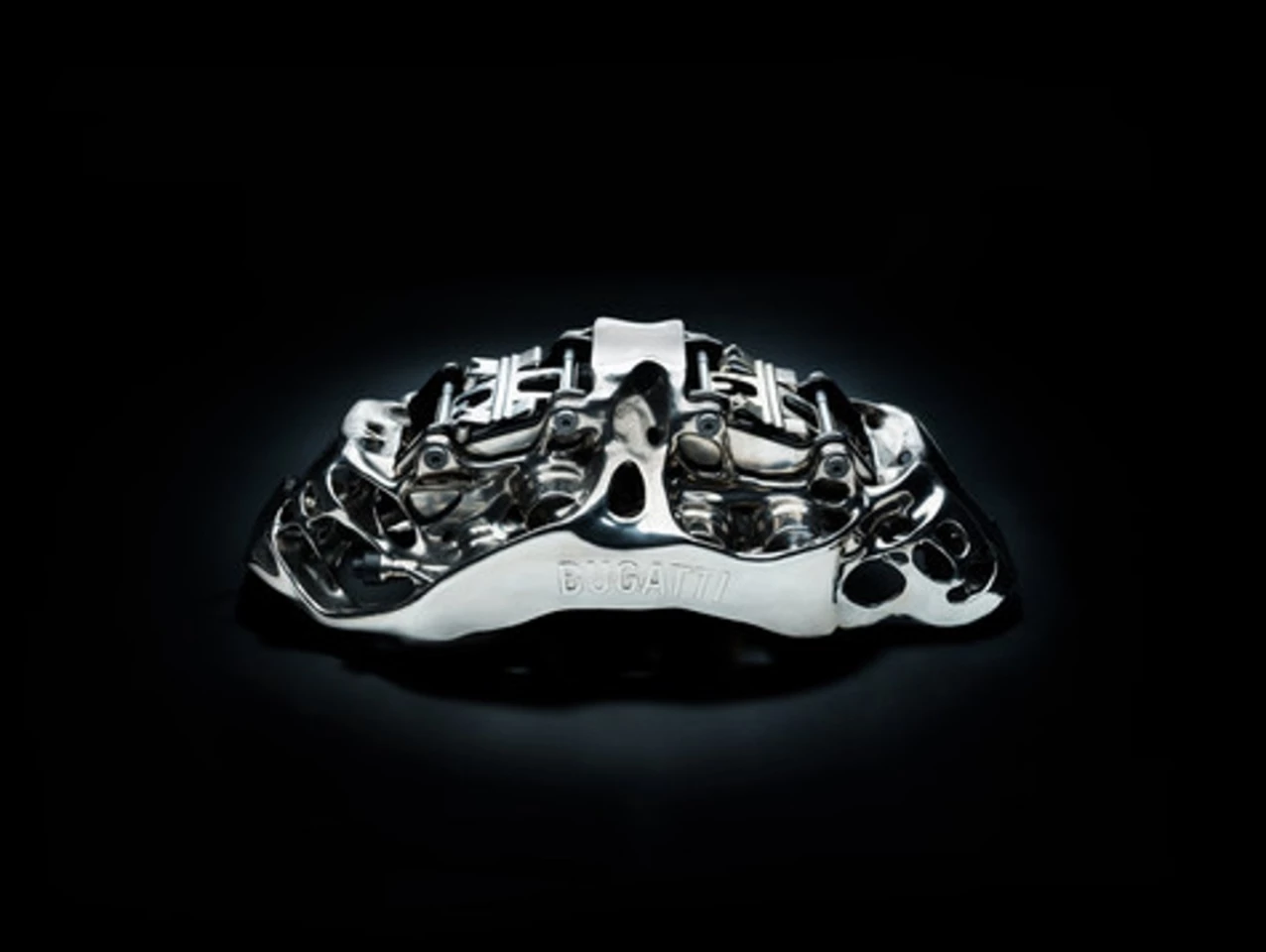
Unfortunately, while titanium promised superior performance and durability compared to aluminum with a 40 percent weight savings, titanium alloys are notoriously hard to cast or forge and often require exotic techniques, like explosive forming. Bugatti's answer was to turn to an additive manufacturing technique, better known as 3D printing, that uses lasers to fuse titanium alloy powder into precise, complex shapes.
The caliper went from idea to prototype in only three months. After Bugatti completed computer modeling, the data files were sent to Laser Zentrum Nord for final process simulation and printing using the world's largest printer capable of handling titanium thanks to its four 400 W lasers.
Bugatti says that printing the caliper took only 45 hours, which is a remarkably short time for making a complex prototype. During the process, the printer laid down 2,213 layers of fine titanium alloy powder one at a time. After each layer was set down, the lasers, guided by the design files, fused the alloy into a cross section of the caliper along with temporary support structures that cooled and solidified instantly, before the machine repeated the process.
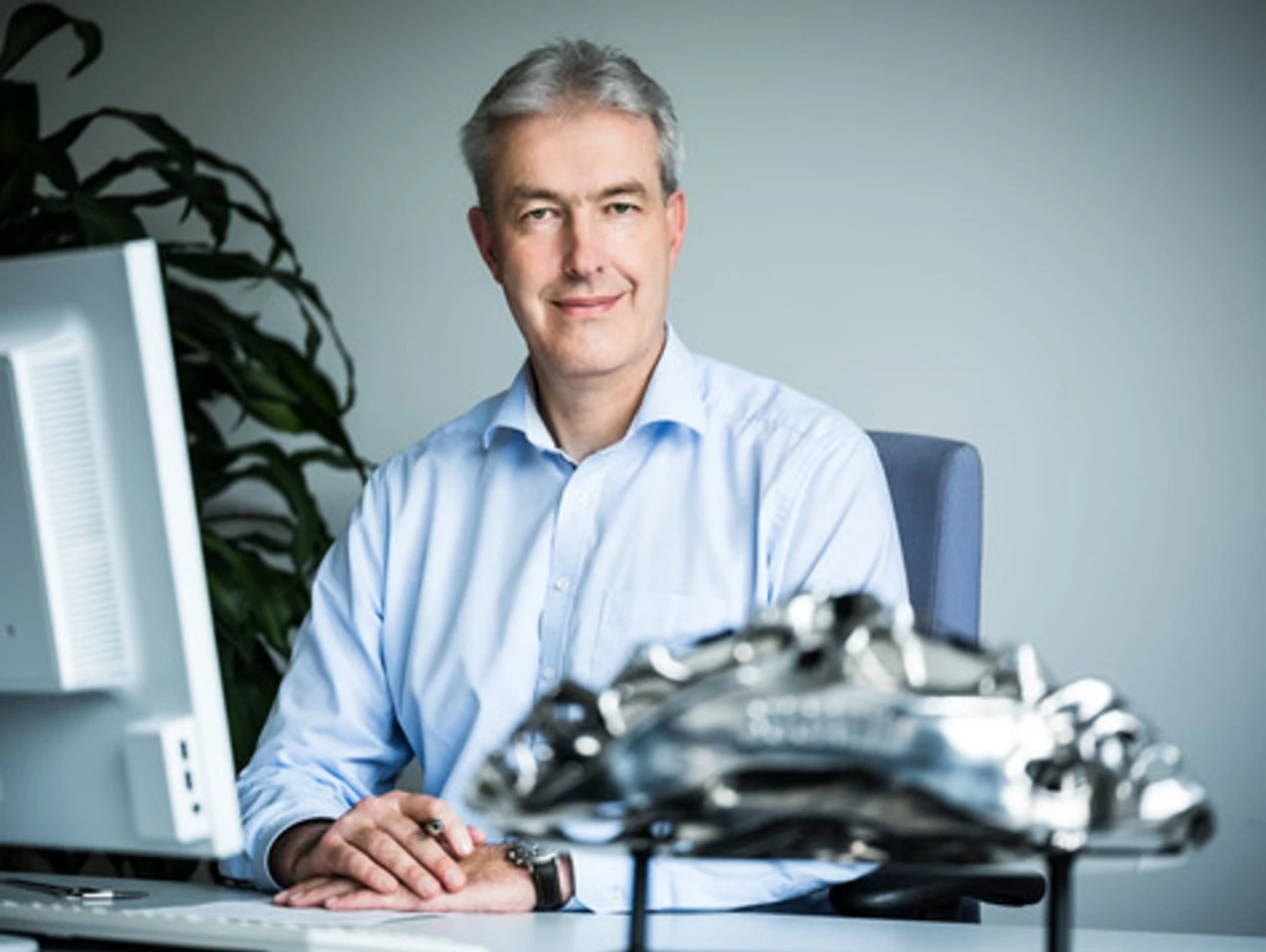
Once completed, the excess powder was removed and the caliper was placed in a furnace, where it was initially subjected to a temperature of 700° C (1,300° F), which was lowered to 100° C (212° F) to stabilize the structure and eliminate stresses. The supports were then removed and the caliper was sent back to Bugatti for final mechanical, physical, and chemical processing to improve is durability before final machining.
"It was a very moving moment for the team when we held our first titanium brake caliper from the 3D printer in our hands," says Frank Götzke, Head of New Technologies in the Technical Development Department of Bugatti Automobiles. "In terms of volume, this is the largest functional component produced from titanium by additive manufacturing methods. Everyone who looks at the part is surprised at how light it is – despite its large size. Technically, this is an extremely impressive brake caliper, and it also looks great."
With the goal of being used in series production, the new caliper is scheduled to begin vehicle trials before June of this year.
Source: Bugatti