The 2010 Los Angeles Auto Show Design Challenge – which asked designers to come up with an efficient 1,000lb (454kg), four-passenger vehicle that maintained comfort, safety, driving-performance and style – has finished in a tie between GM’s Cadillac Aera concept and the Smart 454 from Mercedes-Benz Advanced Design. Previously, the Design Challenge was restricted to major Southern California automotive design studios but this year saw the field widen to include studios from Germany and Japan, resulting in entries from Mercedes-Benz, Honda, Nissan, Toyota and Maybach.
Cadillac Aera
The Cadillac Aera’s win marked the third win for the General Motors Advanced Design California studio in the competition’s short seven-year history. Although it’s designed as a small urban vehicle, the designers approached the Aera (Aero + Era) from Cadillac’s luxury perspective. The 2+2 touring coupe is powered by compressed air via a Pneumatic Drive System that has a 10,000-psi composite air storage tank with a capacity for a 1,000-mile range.
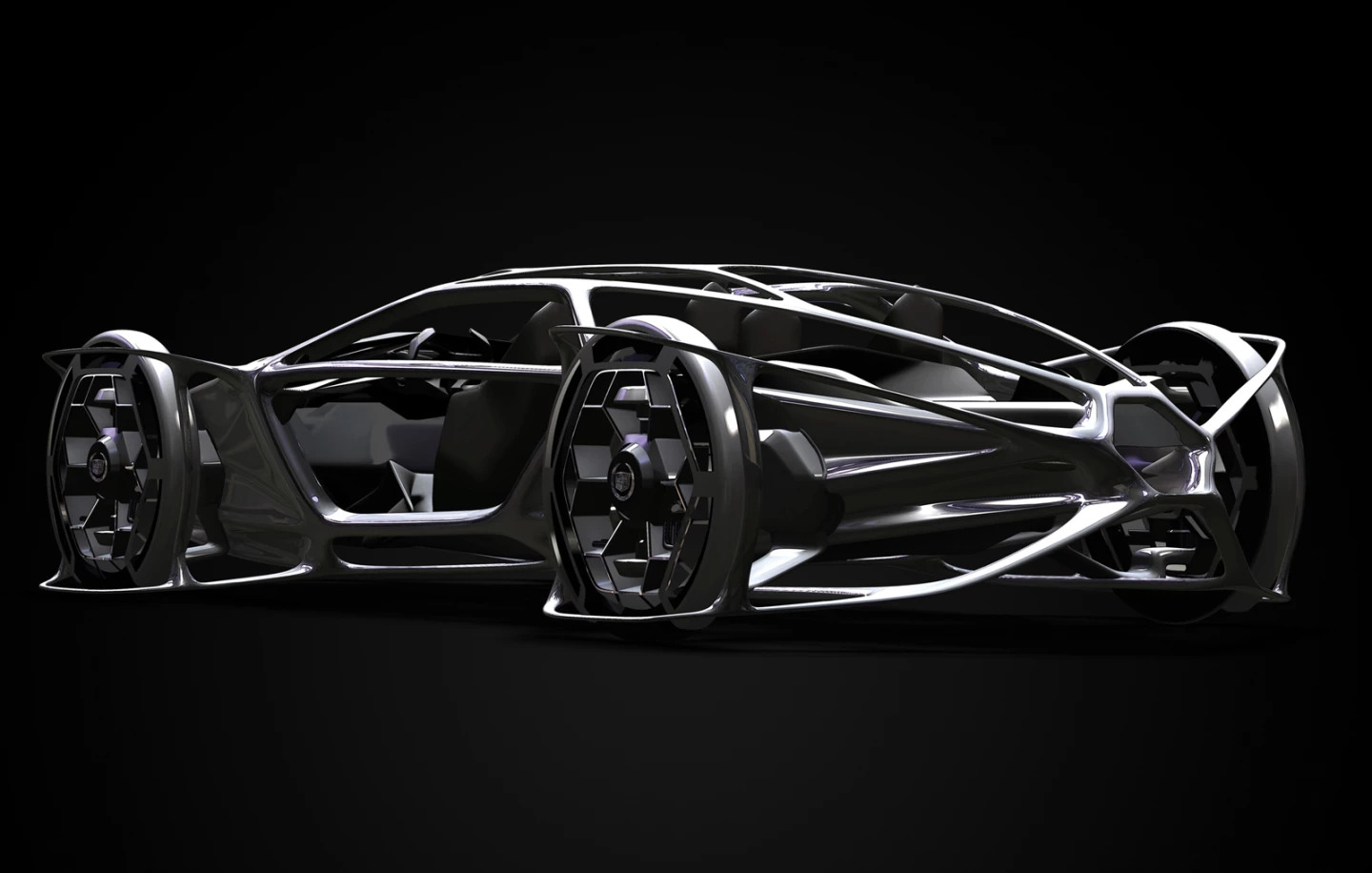
Instead of conventional body panels and glass, the exterior of the Aera is made of a flexible polymer skin that is ultra-lightweight and optimizes aerodynamics. Additionally, pressurized air cells in the skin, which is similar to material developed for the NASA Mars Rover airbags, help cushion the blow in the event of an accident.
The exterior skin sits over the top of a 3D lattice, mono-formed frame that was designed to be similar to configurations consistently found in nature. The lightweight frame is manufactured using a “unique, alloy-utilizing, semi-solid freeform” process, while all major body parts, including interior components, are essentially “grown” into a single part lattice structure.
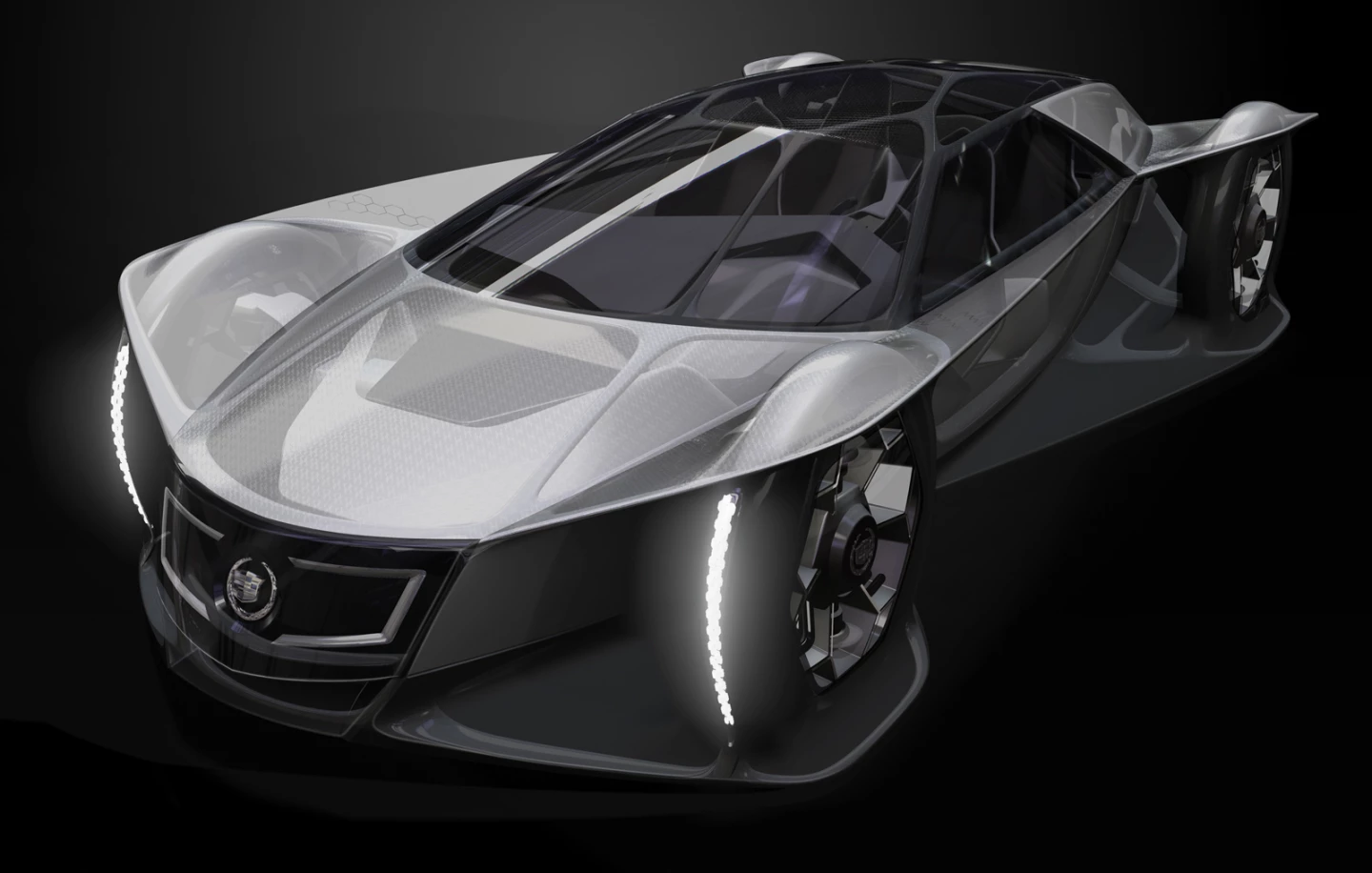
To decrease the mass of electrical components, the vehicle includes a drive-by wire system, while an all-in-one wheel system combines rotary actuator propulsion, steering and suspension functions. There’s also a vehicle-to-vehicle communications system for added safety.
smart 454
From the outset, the competition’s requirement for a four-passenger design marked a departure from smart’s usual two-passenger vehicles. The smart 454, which refers to the Design Challenge’s 1000lb (454kg) weight limit, is driven by two 15 kW electric motors that are housed between the rear wheels and are powered by a replaceable lithium-ion battery.
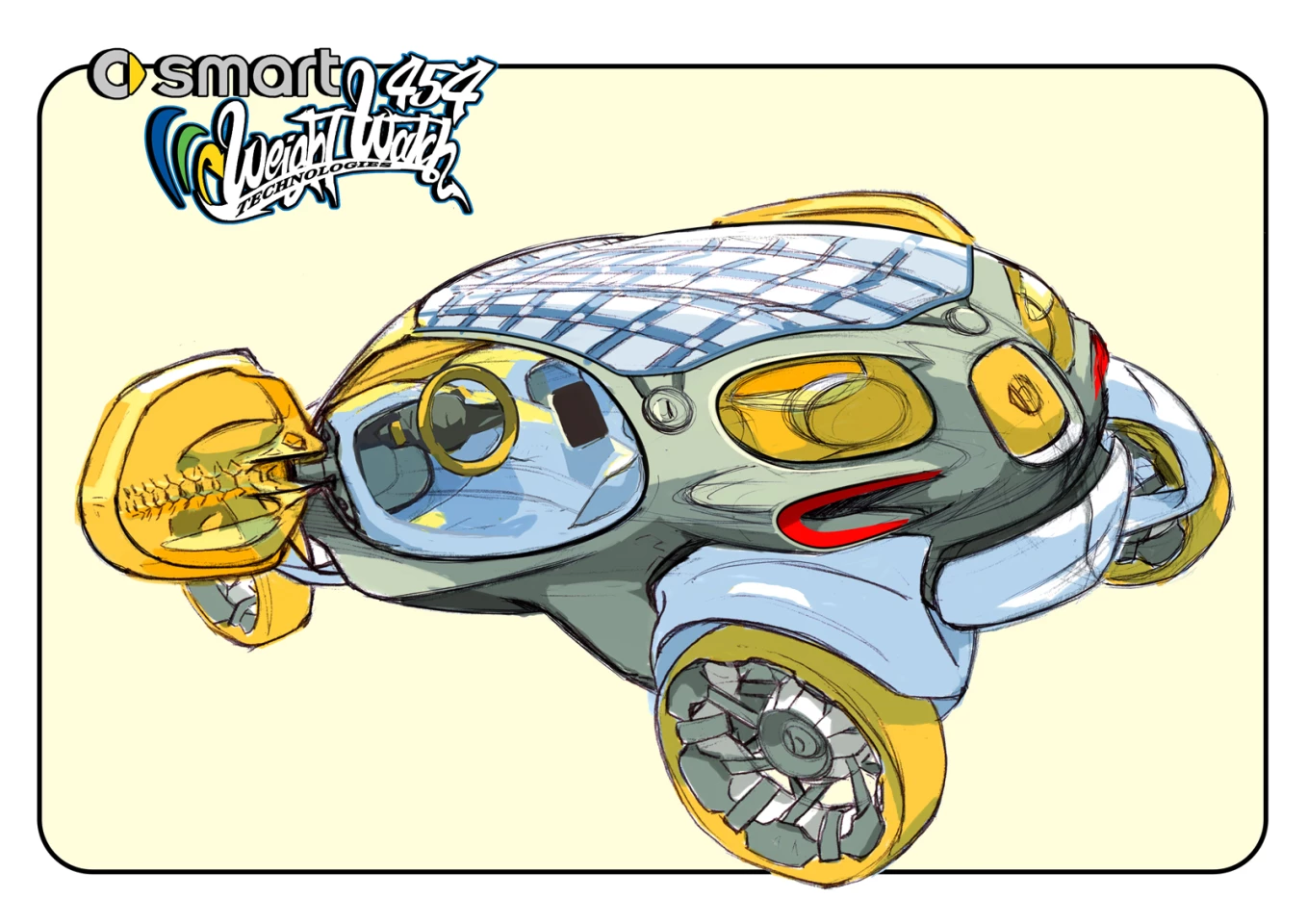
Inside, it’s a case of BYO instrument panel with all functions such as speedometer, battery charge indicator, navigation system and air conditioning controlled and managed via an iPad.
But it’s the method used to create the tridion cell that forms the main structure of smart’s vehicles that is really unique. The vehicle would be produced by so-called “Smart Granny Robots” (SGR) that knit the tridion cell from carbon fibers using huge knitting needles. The designers say this process would allow the vehicle’s geometry to be optimized in terms of weight and strength.
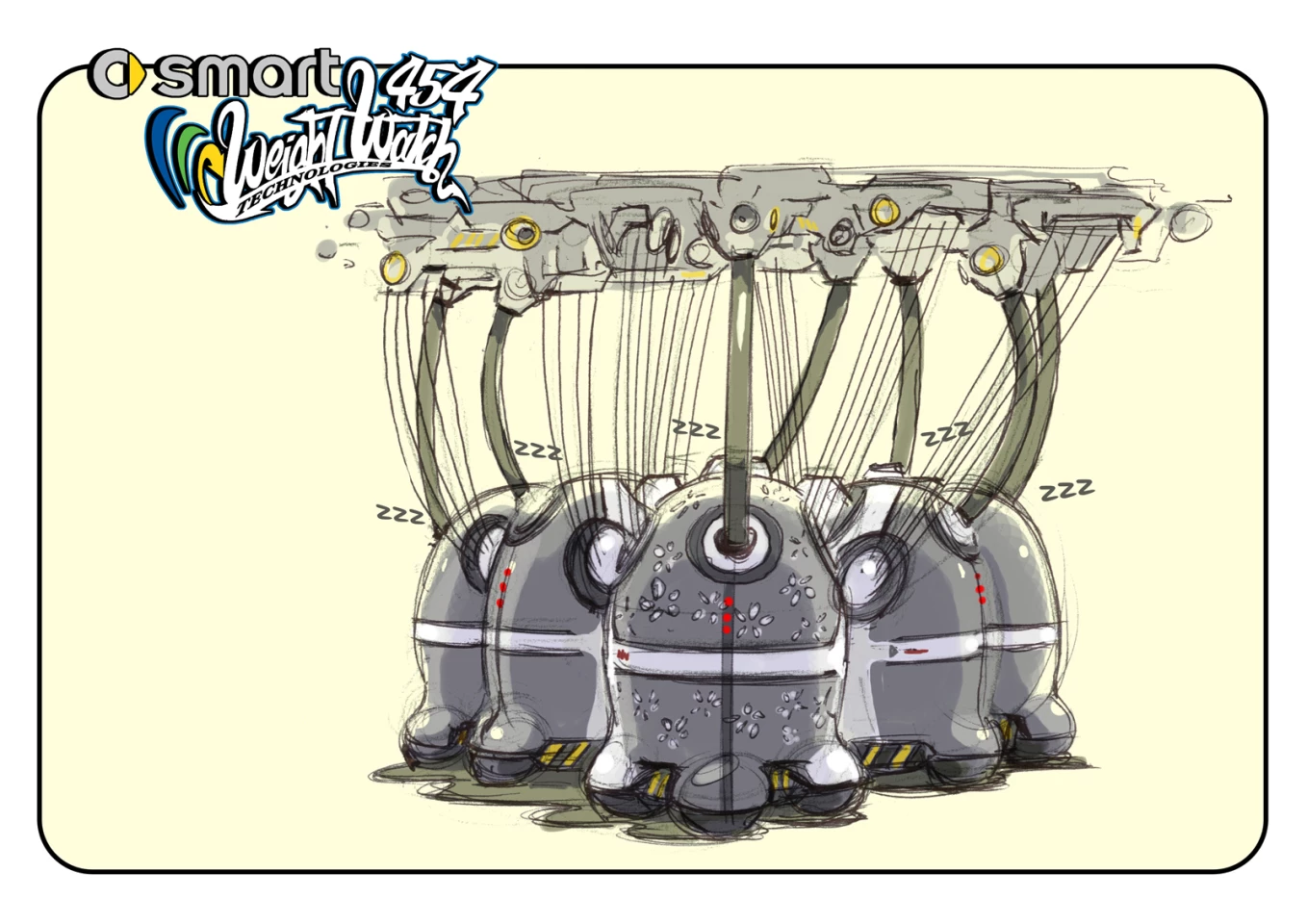
Fitted to the cell are windows, fenders, and bumpers made of recyclable, colored plastic and a roof made of thin, yet durable recycled textile fabric in various printed and woven patterns. Carbon fiber tires would rule out the risk of a flat tire, while SGR technology would enable the production of truly unique and lightweight rims. The familiar smart modular “clip on” design principle would also make the doors, roof, engine and transmission simple to exchange.
Brand fitting winners
“This year’s design challenge was extremely difficult to judge because of the quality of all of the entries, but I believe that the executions that won exemplified everything that we were trying to achieve with this competition,” said Stewart Reed, chair, Transportation Design, Art Center College of Design. “The concepts that won were really spot on for their brands, which was one of many reasons for the victory.”