Researchers at the Energy Biosciences Institute (EBI) are generating bio fuels from renewable sources, such as sugar and starch, using a process that could be commercialized in as little as five to ten years. Although the fuels are currently more expensive to produce than those made from petroleum, they contain more energy per gallon than ethanol and the researchers say that, if adopted, could help to cut greenhouse gas emissions from transportation.
The process begins with a bacterial fermentation process first developed by chemist Chaim Weizmann back during the first world war, which results in a mixture of acetone, butanol, and ethanol. Weizmann, who became the first President of Israel in 1949, is considered the father of industrial fermentation as he used the bacterium Clostridium acetobutylicum to produce acetone. This was in turn used in the manufacture of cordite, which was used by the Allies as a replacement for gunpowder as an explosive propellant.
The EBI researchers discovered that organic solvents could distill acetone and butanol using just ten percent of the energy normally required. The process leaves most of the ethanol behind and the resulting mixture has the right ratio to be easily converted into fuel resembling petroleum-based diesel using a catalytic process. Tests carried out by the team showed the fuel burned about as well as normal petroleum-based diesel fuel.
“It looks very compatible with diesel, and can be blended like diesel to suit summer or winter driving conditions in different states,” said Harvey Blanch, a professor of chemical and biomolecular engineering.
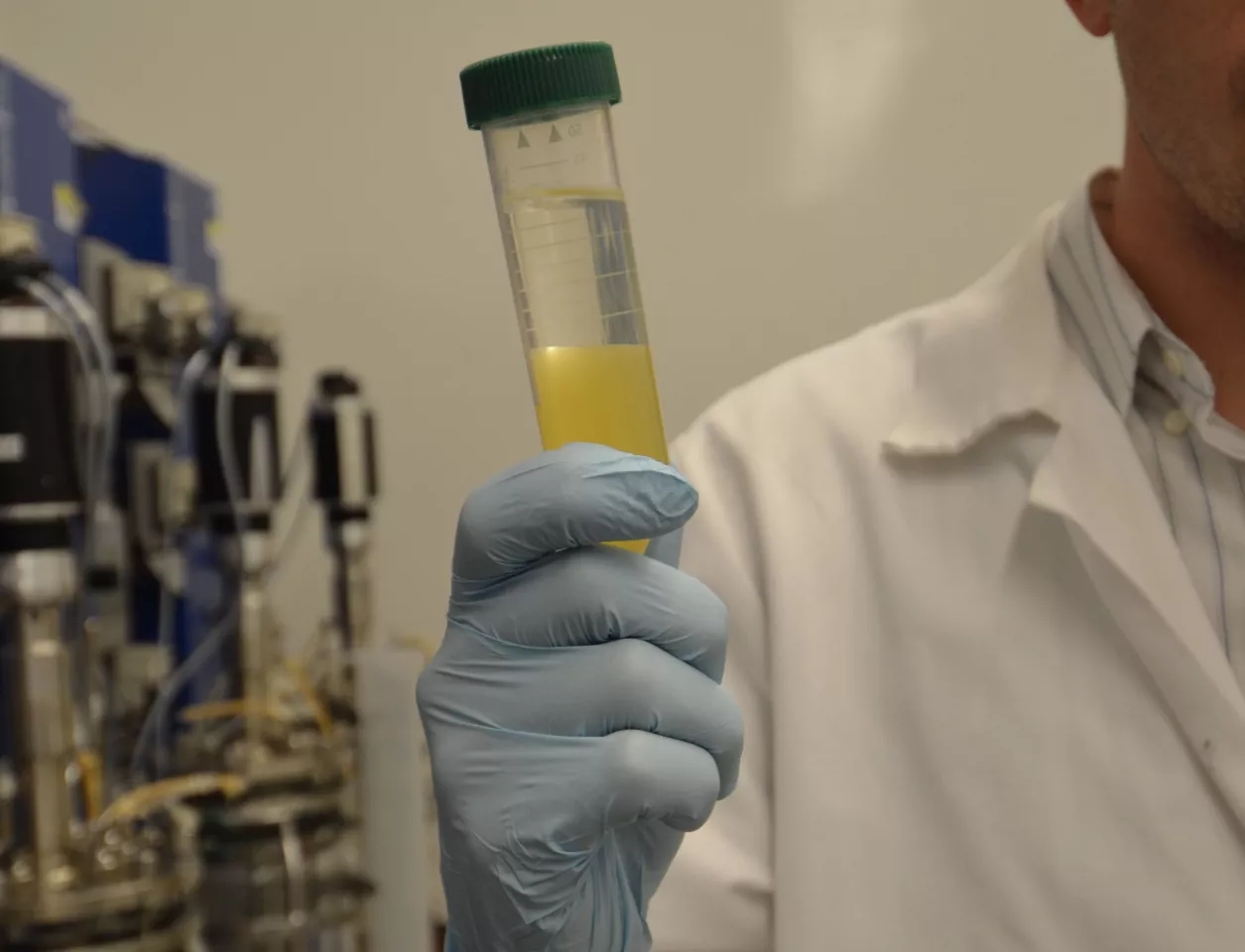
The catalytic process, which uses palladium and potassium phosphate, converts the chemicals into hydrocarbons. “You can tune the size of your hydrocarbons based on the reaction conditions to produce the lighter hydrocarbons typical of gasoline, or the longer-chain hydrocarbons in diesel, or the branched chain hydrocarbons in jet fuel,” explained Dean Toste, a professor of chemistry who developed the catalyst. The resulting chemicals can also be turned into plastics.
The researchers have already found alternative catalysts that are cheaper but just as effective, nudging the process closer towards commercial viability. BP pledged US$500 million dollars in funding to the EBI, a joint initiative between UC Berkeley, the Lawrence Berkeley National Laboratory, and the University of Illinois at Urbana-Champaign, where the discovery was made.
The team's work is described in a paper published in a recent issue of the journal Nature.
Source: UC Berkeley News Center