Diginova, a consortium of European companies and universities, has proposed a roadmap for how the manufacturing industry could fully benefit from the digital era over the next two decades. According to this vision, we are moving toward manufacturing highly customizable, on-demand goods that are locally produced from raw materials and globally distributed digital designs. This could lead to extreme product customization, decentralization of production and, perhaps surprisingly, much lower costs of everyday goods ranging from smartphones to medicine.
The industrial revolution introduced a highly effective way of driving prices down. This involves very large capital investments, high energy use, extensive amounts of repetitive manual labor, long distance transportation, and the underlying assumption that the consumer base is sufficiently large and homogeneous.
But the one-size-fits-all philosophy doesn't always work. Take, for instance, the way companies are struggling to find the "perfect" smartphone screen size. Seven years after the first iPhone was introduced, we've determined that some screens are probably too small and some probably too big; but, like Goldilocks, will we ever find a universal screen size that's just right?
For tech giants like Apple and Samsung, the choice has always been between producing a single screen size (which is easier to manage, but will never exactly meet everyone's needs), or offering a wide range of options (which is more flexible but can easily end up confusing potential buyers).
Smartphone wars have shown us that it's foolish to assume that consumers will ever come to a unanimous agreement on the matter, since we each have individual needs and preferences. Perhaps, instead of Goldilocks, we're more like Cinderella, and what we really want is a perfectly fitting Gorilla glass slipper that's uniquely tailored to us.
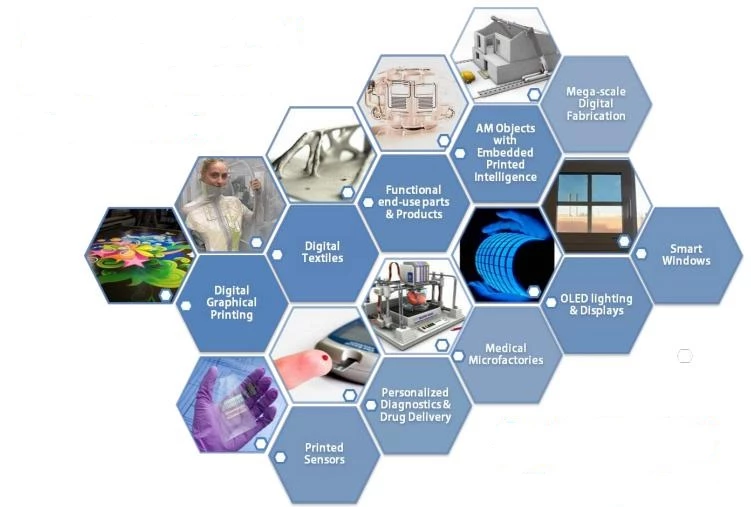
As the world is becoming more digital, and with the introduction of disruptive technologies like 3D printing, there may be a better way – a paradigm that's less wasteful, allows for much greater personalization, and requires very little capital investment, evening out the playing field. Diginova, a Germany-based consortium of 20 companies and universities from all over Europe, has produced an insightful document detailing how such radical change might take place over the next two decades.
Diginova's vision is that, in the same way that the music, photography and printing industry have been revolutionized by the switch to digital technology, so will the manufacturing industry.
More precisely, we could be heading toward a global distribution network of digital designs and specification files that will form the basis of local production. Large scale production will become less economically advantageous, making smaller production and customized products increasingly competitive, heading toward low-carbon and zero-waste manufacturing.
Using the example of 3D printing: when needing a new pair of shoes, rather than going to a store you may choose to go online, pick your favorite design and buy it for a few dollars, or download for free. With a few taps of your fingers you could use your smartphone to scan your foot, select colors and materials, and upload the design to a local 3D printing shop. Now, all you need to do is wait for your pair of perfectly fitting shoes to be delivered to your doorstep.
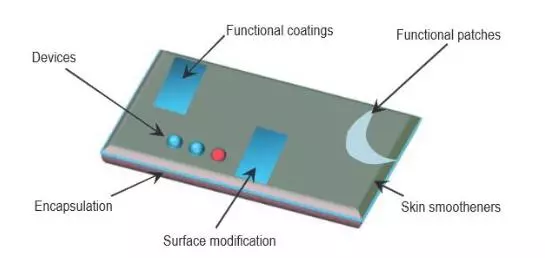
But 3D printing is only one of several industries that is undergoing this type of transformation. Diginova has identified the few areas in which the switch to digital fabrication is likely to have the greatest effect over the next 20 years. These include digital graphical printing, smart textiles, OLED lighting and displays, smart windows, printed sensors, personalized diagnostics and drug deliveries, and even medical microfactories.
Coming back to our example of smartphone screens, the potential for digital fabrication within OLED technology is to allow for the creation of an extremely wide range of screens in both size and shape, including perhaps curved and flexible displays (they'll need to fit the phone chassis, of course, but that problem can be solved just as easily).
Ultimately, even without the advantages of the economies of scale, digital fabrication will lower costs. Once local communities, or even individuals, have their own fabrication equipment, they can create a car, a mobile phone, agricultural equipment or whatever product they need at the cost of raw materials, limited transportation and local overheads, rather than covering the substantial costs of shipping, labor, marketing, and retailer mark-ups. Renewables such as solar or wind could also help keep power costs down.
A document (PDF) detailing the proposed roadmap for digital fabrication is freely available for download.
Source: Diginova