SiFly says its drones fly 4X longer, 10X farther, 10X quieter and carry 5X more payload than the competition, while manufacturing in the USA at China-competitive prices. And they don't need parachutes. We asked how... Here's the secret sauce!
SiFly's claims are absolutely outrageous. Multirotor drones have been around in numbers for more than 10 years now, Chinese companies like DJI have had a decade to evolve and optimize these relatively simple airframes. How can a startup waltz into this space and find 400-1,000% gains in critical performance factors like flight endurance?
Extraordinary claims require extraordinary evidence, and Chief Strategy Officer David Mazar tells me over a video call that the SiFly team has been out and about presenting that evidence to people in person, most recently at a law enforcement drone event in Ogden, Utah this week.
It's probably not the most exciting thing in the world to watch a drone hover for two hours on battery power – he laughs when I ask if people bring a pillow and blanket to the demos. "I mean, you're kind of right," he says, "After a while, there's only so much you can talk about ... After you get past an hour and a half and there's 40% left in the battery, people are like 'ok, let's bring it down, we believe you!'"
I now believe him too. Here's a two-hour hover, mercifully compressed into a 30-second time-lapse video that still manages to get boring.
So what's the secret? How has SiFly found so much extra performance in multirotor airframes? It's not by using a combustion engine or hydrogen fuel cells – or indeed using alien tech, all of which readers proposed in a lively comments section on our last piece. The closest guess came from a reader named "Username" – who pointed out the larger diameter, more efficient rotors, but correctly said this wasn't enough by itself.
Mazar tells me it's a combination of factors working together, as well as some system-level thinking outside the box, that add up to SiFly's ridiculous performance gains.
SiFly's recipe for disruptive multirotor performance
The first ingredient, as "Username" suggested – is SiFly's larger-diameter rotors, leading to lower disc loading, slower rotation speed and improved energy efficiency in a hover.
But this unlocks the second ingredient: a different class of battery. "Most multirotors today," says Mazar, "have really small blades, super high disc loading. They have to use a battery chemistry called lithium polymer (LiPo), which is made for high power, high output missions. Our lower disc loading design enables us to use the same cells you'd see in an electric vehicle – lithium-ion 21700 cells."
Essentially, Mazar says these EV cells are optimized for energy storage rather than peak power output, so they're considerably better for flight endurance.
The third ingredient is ... well, that SiFly's drones carry much bigger batteries than the competition. Is that cheating? "It's all about optimizing the right amount of battery to the total weight of the aircraft," says Mazar. "Most multirotors today are below 35% in their battery to weight fractions. What we've optimized around is a fraction that's much higher, closer to 60% or more."
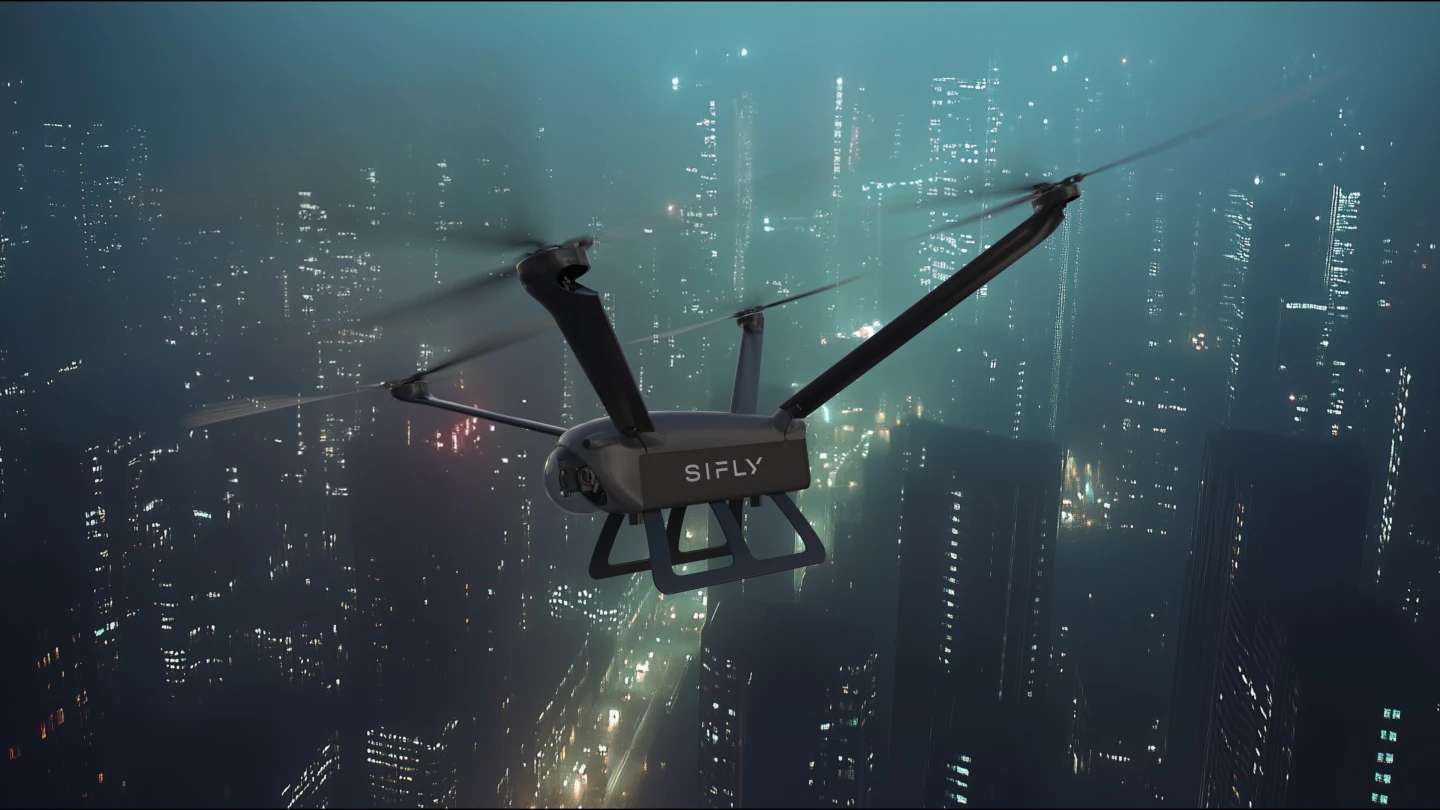
From here, things get considerably more interesting. The SiFly Q12, you may have noticed, can hover for two hours straight, but in forward flight, endurance gets a 50% boost to three hours. There are a few things going on here.
The first is that the arms holding the rotors have been shaped into slim airfoils capable of generating some passive lift at cruise speed. Certainly not as much lift as a proper lift & cruise VTOL (vertical take-off and landing) design with a full sized wing enjoys, but it's not nothing.
The second is that the front two rotors sit lower than the rear two. "Our front rotors are about 10 degrees lower then our rear rotors," says Mazar, "reducing the amount of rotor wash that we get from air coming our of the front rotors when we're in forward flight."
And the third is that the props are flat. "Most multirotors," says Mazar, "really use hover-optimized propellers. We've developed straight, low-drag blades, more akin to a helicopter's, which enable us to fly much more efficiently in forward flight."
Which leads to by far the most interesting innovation on this aircraft in my eyes; if the props are flat, does that mean SiFly runs variable-pitch blades like a helicopter too? Yes – but in a very different way.

Torque-actuated rotor pitch control
Where a helicopter uses a swashplate, allowing a pilot to move the center of lift around the rotor disc or quickly increase or decrease lift all at once, SiFly Founder and CEO Brian Hinman has created and patented a system that mechanically varies blade pitch in response to motor torque.
So the rotor blades sit nearly flat at zero or low torque, but as more torque is applied by the motor, a "torsionally flexible shaft" begins to twist in the motor housing, and this is connected to a mechanism that tilts the blades until they reach a hard stop at a pre-determined maximum pitch. As torque decreases, the flexible shaft elastically moves back to its untwisted state and the blade pitch drops again.
So the harder you run the motors, the more the blades pitch up – perfect for takeoff and hover carrying large payloads. And when you're applying relatively low torque to keep the blades turning in forward flight, they pitch down to enable a lower-drag cruise state.
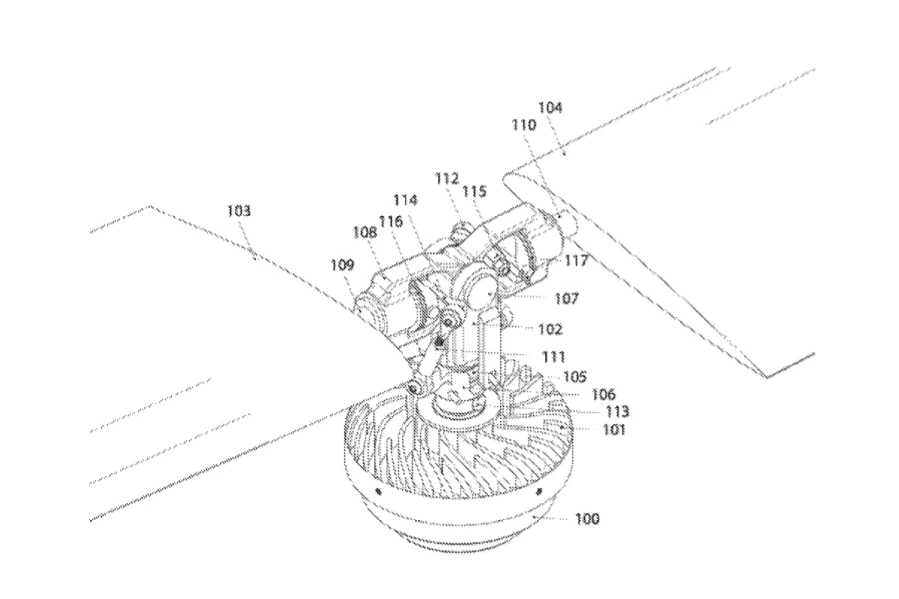
This also gives SiFly an interesting way to rapidly increase or decrease lift without having to wait for propeller RPM to catch up to a control input. "Our torque-actuated rotor pitch control essentially enables us to scale up the quadcopter architecture without facing the inertia and responsiveness problems of RPM-controlled thrust systems," says Mazar. "The rest of the industry, I think, believes that explicit collective control is required to make large rotorcraft – which carries a burden of increased cost and weight and these types of things. We think it's a much more elegant solution and approach that we're taking."
"You put all these things together," Mazar tells me, "and you're talking about efficiency upon efficiency upon efficiency."
Passive autorotation for soft landings
Oh, and this torque-actuated blade pitch system comes with a free set of steak knives, too, in the form of a safety system that lets SiFly's drones autorotate safely down to the ground in a power failure scenario. So where other large drones might require the added weight of ballistic parachute systems to float down safely, these don't.
Hinman describes how this works in a Medium post and another two patents, but it can be summarized like this: in a thrust system power failure – assuming the control system is still powered – the drone begins to fall, and the lack of torque through the motors flattens out the blade pitch. As descent speed increases, the airflow up through the blades spins them up to high RPM, as with a helicopter.
The spinning blades represent a form of stored energy, and this means there's still a way to apply torque to the motors – just in reverse. The control system is able to brake the rotors by running the motors backwards as generators, and the resulting torque is enough to effect a change in blade pitch.
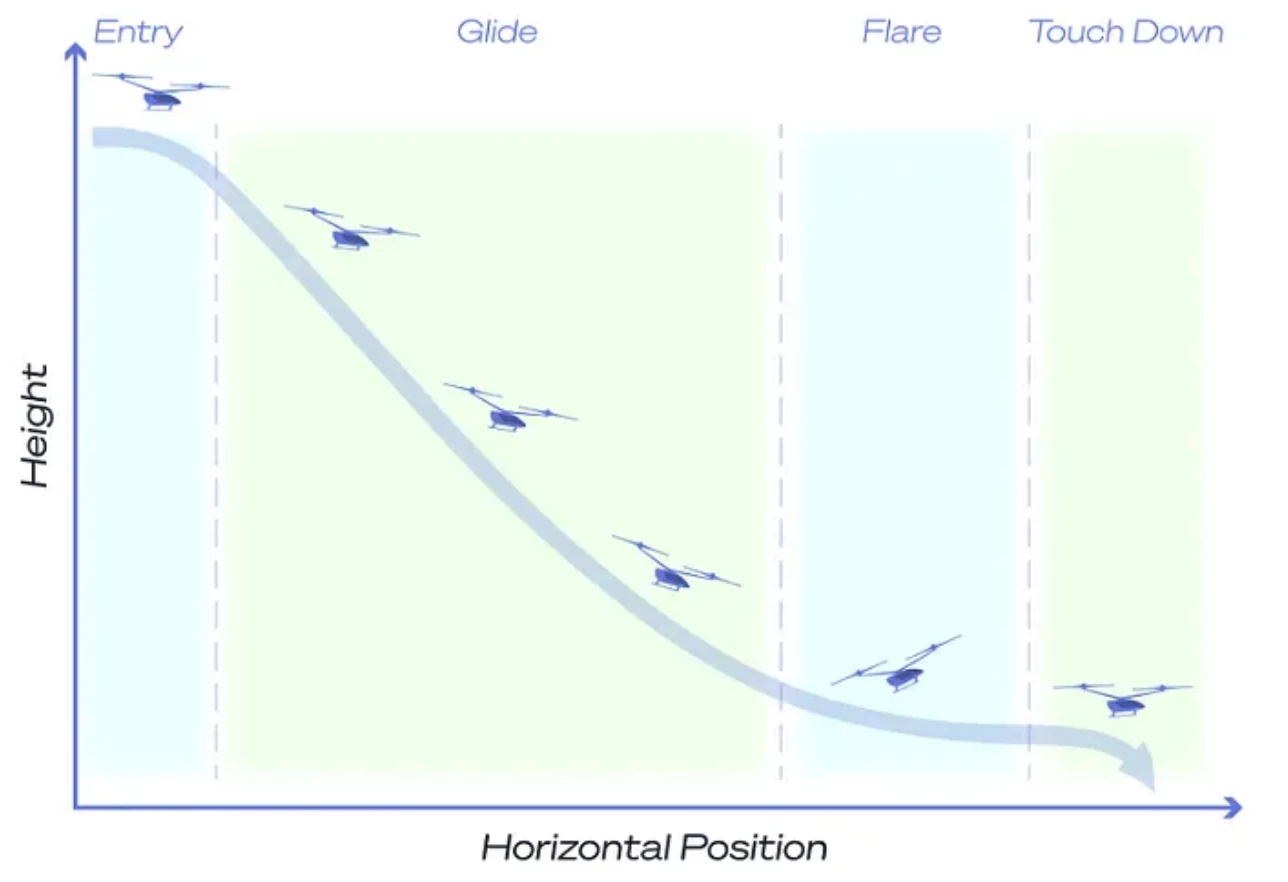
Using this electrical braking system gives SiFly a degree of control over an unpowered descent from cruise speed. Allowing the aircraft to pitch forward slows the rotor speed as it glides downward, and pitching it backward trades some airspeed for rotor speed, forcing a lot of air through the blades and rapidly spinning them up.
Just before a helicopter lands in autorotation, the pilot needs to perform a "flare" in which all blades are pitched up to extract the maximum possible lift from the energy stored in that big, free-spinning top rotor and create the cushion of air required for a soft touchdown.
Obviously, SiFly's quadcopter rotors aren't big or heavy enough to store nearly as much energy as a helicopter rotor. But there is a big battery on board. If that's still functional, Hinman says it's possible to regenerative-brake enough energy back into the battery for a powered flare and landing.
And if the battery's totally gone, well ... "The touch down phase of autorotation involves the unloading of the inertial energy within the four rotors," writes Hinman. "Collective is gradually increased across all four rotors, with some degree of differential adjustment for attitude control, and the quad-copter comes to a cushioned landing on the ground as the rotors gradually lose speed."
Just how cushioned remains to be seen, and the answer will likely be very different depending on cruise speed and altitude at the point of failure. It's unlikely to work as well as helicopter autorotation, but it might top the performance of a ballistic 'chute in some circumstances, and at the end of the day these are uncrewed vehicles; it might just need to slow the fall down enough to let deformable crash structures take the final hit and minimize damage ... Not that this will be a great comfort to anyone standing underneath it when it hits.
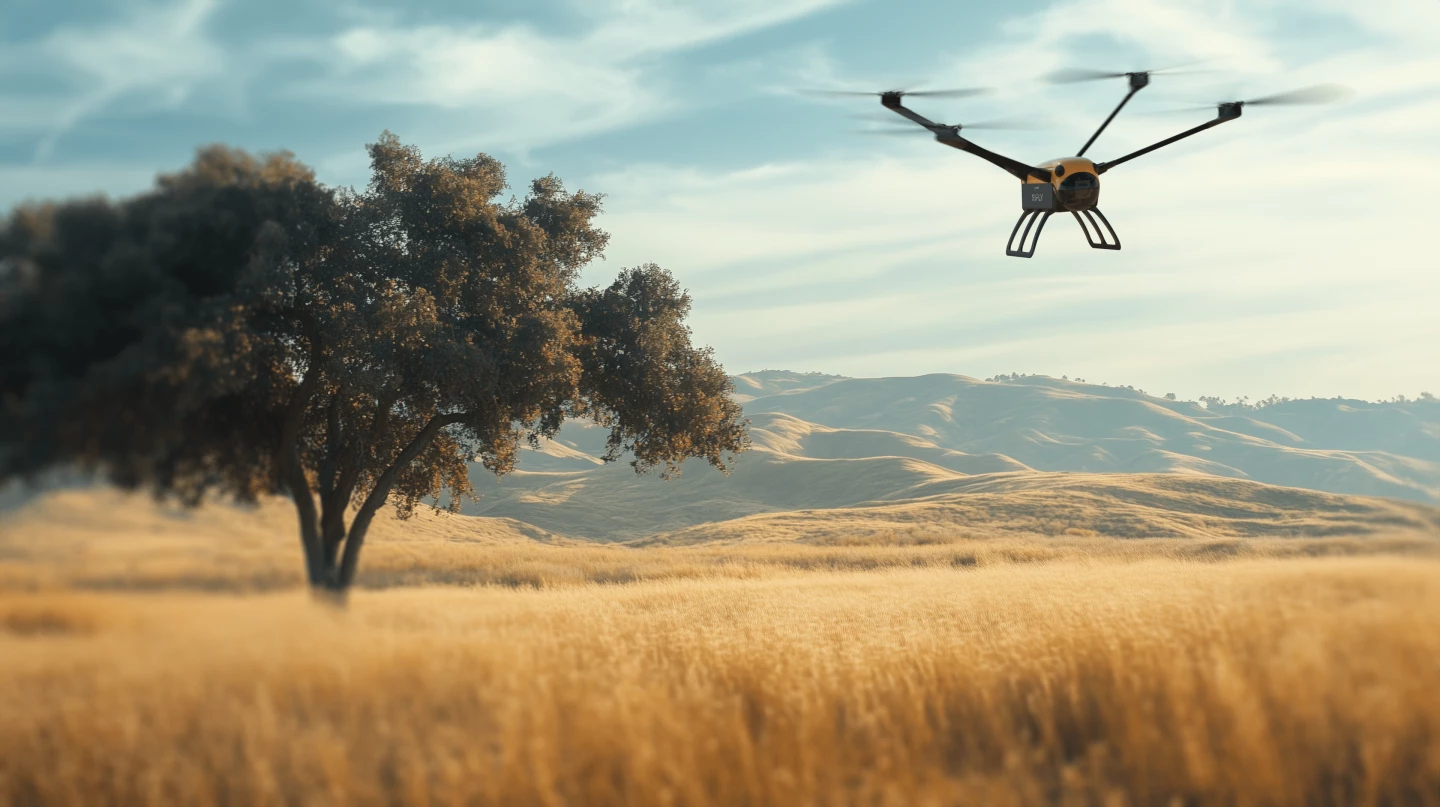
So how are they building this in the USA at prices competitive with Chinese rivals?
Well, firstly, what kind of rivals are we talking about? "We've had people try to compare us to a DJI Air – that's not what we're talking about here," says Mazar. "We're talking about their large enterprise-grade system. Models in the M300, M350 type category. And they have a tremendous product."
So how can SiFly keep American manufacturing costs competitive with Chinese competitors that churn out drones by the million and leverage hyper-local supply chains so effectively that they've completely dominated the drone market from day dot?
Well, not all the components will be made on US soil, for starters. "There are some elements from a component standpoint where China is basically the only place you can get stuff," says Mazar. "Things like blades, there are only a few places to get blades that will be competitive ... But there are supply chains opening up in Malaysia, Vietnam, and some other areas where we have partners that are very capable at developing subcomponent systems ... We're able to bring them back and make it very efficiently."
Certainly, if SiFly wants to press its biggest domestic advantage – the fact that it's producing American-made drones – the company won't be sourcing flight control computers or software out of China that could get it ruled out of consideration for defense contracts and the like.
Realistically, the biggest cost advantage SiFly brings to the table is probably the switch from LiPo to EV-grade batteries, simply due to the scale at which EV cells are now manufactured. "We leverage what electric vehicles are doing on the cell side," says Mazar, "and we have our partners who are packing them, which makes for a much more cost-effective battery solution."
And much of the rest, Mazar says, comes from the fact that the company won't be using off-the-shelf components, but instead using its own designs. "Designing for manufacturing at all levels," he says, "making things simple and easy to produce is one piece of it." This sounds a little backwards to me – surely it's hard to beat off-the-shelf prices.
We shall see – but not just yet. "We have defined a price for our pre-order program," Mazar tells me, "and we will be releasing that publicly in the very near future."
Certainly, this company is bringing some very innovative thinking to the table. It's rare to see a disruptor come into an industry like this, which looked pretty mature and settled, and blow competitors' performance so far out of the water – and I hope you've found the process of figuring out how as fascinating as I have!
Source: SiFly