A European project to develop self-powered sensors for monitoring aircraft integrity is off the ground, with EADS Innovation Works and Vienna University of Technology reporting that the first test flights of the thermoelectric Energy Harvesting Modules have been carried out on an Airbus aircraft.
Stress to aircraft frames caused by drastic changes in humidity, pressure, velocity, temperature, bird strikes, passenger and freight loading if undetected can be catastrophic. As a result, corrosion, delamination, cracks, disbonds, and other failures creep in once the aircraft has racked up significant mileage.
There are already various sensors in play that can monitor the degradation of aircraft structure and components before critical levels are reached, thus providing ample time for maintenance engineers to schedule a repair and fit replacement parts before they actually fail. The resulting preventative maintenance through diagnostics provides for lower costs and increased operational flight time for each aircraft.
Existing systems use a wire-based tech which adds to the overall weight of the aircraft and to the complexity of design. Additionally, conventional batteries are not designed for such large temperature difference to which an aircraft is continuously exposed and besides ... nobody wants to regularly replace all the sensor batteries in the aircraft.
As we first reported back in 2011, EADS and the Vienna Institute of Technology are working on a viable, cost-effective, wireless solution that uses thermoelectric Energy Harvesting Modules to power the sensors and wirelessly submits data to a system monitoring unit.
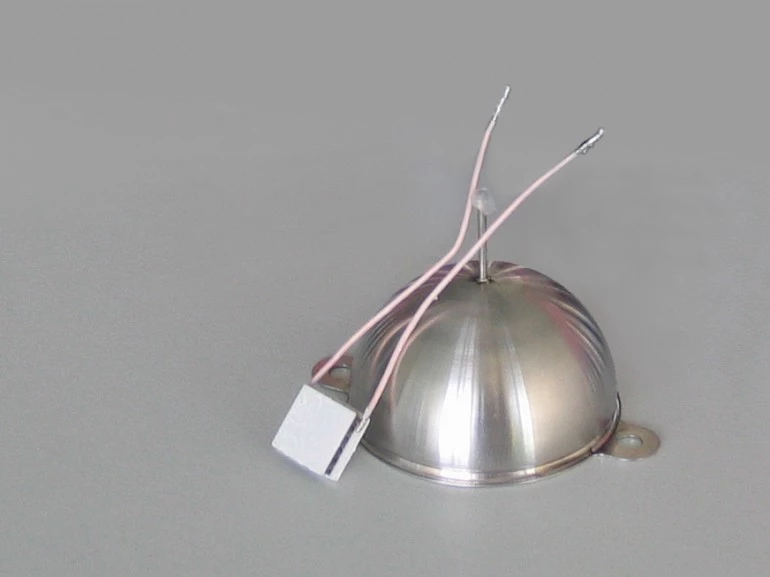
These thermoelectric energy harvesters use the temperature difference created when the aircraft takes off and lands to produce the small amount of energy required by the sensor. Each harvester contains a small water tank which takes on the temperature of the warmer air at ground level. As the plane ascends, the difference in temperature between the warmer water and the colder outer wall is used to create electricity (a phenomena known as the Seebeck effect). On the way back down the scenario is reversed with the water now cooler than the outer wall of the sensor. The harvesters are also designed to store sufficient operating energy when the aircraft is cruising and there is no considerable temperature difference between the two.
During the recent tests, several flight cycles with different flight profiles, flight lengths, and outside temperatures were performed. The results have confirmed expectations from the initial climate chamber simulations carried out two years ago and demonstrated that thermoelectric energy harvesting in harsh aircraft environments is feasible.
"We have been able to obtain around 23 joules of energy per flight, which is sufficient to power up a wireless sensor node," says Vienna University of Technology PhD student Alexandros Elefsiniotis.
Researchers are also investigating the use of alternatives to water which may be more suitable under different flight scenarios.
"EADS Innovation Works wants to use the best available technology for the autonomous sensors in future, therefore the new method is of great interest to us", says Prof. Becker from EADS Innovation Works. "We are confident that energy autonomous sensors will soon be flying in our aircraft."
Source: Vienna University of Technology