The majority of today’s lithium batteries use a rare and expensive metal called cobalt as part of the cathode component, but mining this material comes at a great cost to the environment. One of the greener alternatives is known as lithium ion phosphate, and a new breakthrough could boost the eco-credentials of this cathode material even further by restoring it to its original condition once it is spent, using just a fraction of the energy of current approaches.
The research was carried out by nanoengineers at the University of California (UC) San Diego, and focuses on recycling techniques for batteries with cathodes made from lithium iron phosphate. By doing away with heavy metals such as nickel and cobalt, these types of batteries can help avoid the degradation of landscapes and water supplies where these materials are mined, along with the exposure of workers to dangerous conditions.
Increasing awareness of the problems associated with cobalt is driving a shift in the industry, with many looking to alternative battery designs, including big names like IBM and Tesla, who this year started selling a Model 3 with lithium iron phosphate batteries. These are safer, have longer lifetimes and are cheaper to produce, though one shortcoming is that it is expensive to recycle them once they are spent.
“It’s not cost-effective to recycle them,” says Zheng Chen, a professor of nanoengineering at UC San Diego. “It’s the same dilemma with plastics – the materials are cheap, but the methods to recover them are not.”
The recycling breakthrough focuses on a couple of mechanisms behind the deteriorating performance of lithium iron phosphate batteries. As they are cycled, this process drives structural changes that see empty spaces created in the cathode as lithium ions are lost, while the iron and lithium ions also trade places in the crystal structure. This entraps the lithium ions and prevents them from cycling through the battery.
The team took commercially available lithium iron phosphate battery cells and depleted them to half their storage capacity. They then disassembled the cells and soaked the resulting powder in a solution with lithium salt and citric acid, before rinsing it off, drying it and then heating it at temperatures of around 60 to 80 °C (140 to 176 °F). This powder was then fashioned into new cathodes and tested in coin and pouch cell batteries, where the team found the performance to be restored to its initial state.
This is because the recycling technique not only replenishes the battery’s stocks of lithium ions, but enables the lithium and iron ions to revert back to their original spots in the cathode structure. This is thanks to the addition of citric acid, which feeds the iron ions with electrons and reduces a positive charge that normally repels them from moving back to their original spot. The upshot of all this is that the lithium ions can be released and cycled through the battery once again.
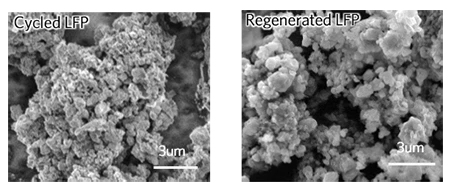
According to the team, its technique consumes 80 to 90 percent less energy than current approaches to recycling lithium ion phosphate batteries, and emits around 75 percent less greenhouse gases. While this is a great start, the team says further studies are needed to ascertain the overall environmental footprint of collecting and transporting large amounts of these batteries.
“Figuring out how to optimize these logistics is the next challenge,” Chen says. “And that will bring this recycling process closer to industry adoption.”
The research was published in the journal Joule.