Solar cell technology is a seen as a key pillar in our transition to cleaner forms of energy, but within this field there is all kinds of room for experimentation. Solar cells that are thin and flexible hold unique promise in the area, as they could be applied to all kinds of irregular, curvy or otherwise unsuitable surfaces. Thinner than a human hair, a new lightweight solar cell from MIT scientists continues to push the envelope in this space.
The MIT team behind the technology sought to build on its previous advances in material science, which in 2016 culminated in ultra-thin solar cells light enough to sit atop a soap bubble without breaking it. As is the case with other thin, light and flexible solar cells we’ve looked at over the years, this pointed to all kinds of possibilities, from paper-based electronics to lightweight wearables that harvest energy throughout your day.
Despite the potential, the team still had some problems to solve, with the fabrication technique for the solar cells requiring vacuum chambers and expensive vapor deposition methods. In order to scale the technology up, the scientists have now turned to ink-based printable materials to streamline the process.
This begins with nanomaterials in the form of printable, semiconducting inks, a technology with wide-ranging potential when it comes to electronics. These are deposited onto a plastic substrate only 3 microns thick, along with a printable electrode, to form a solar module. That module can then be peeled off and glued to a fabric substrate that offers the mechanical strength needed to prevent tearing, while adding minimal weight.
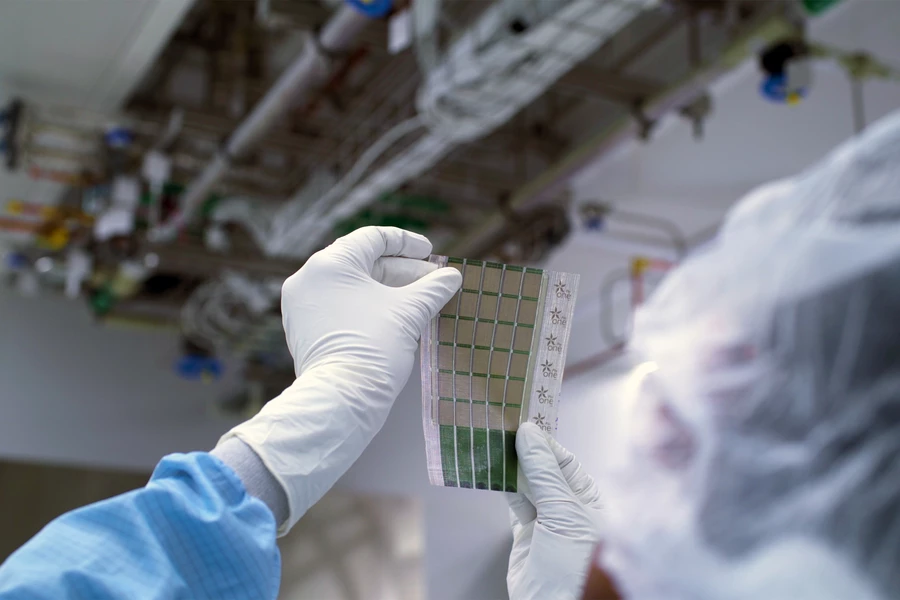
The finished product is a flexible and ultralight solar cell with one hundredth the weight of conventional solar panels, but an ability to generate 18 times more power per kilogram. In testing, the team found the solar cell could generate 370 watts per kilogram (2.2 lb) when adhered to the fabric, but up to 730 watts when standing alone.
“A typical rooftop solar installation in Massachusetts is about 8,000 watts,” said co-lead author Mayuran Saravanapavanantham. “To generate that same amount of power, our fabric photovoltaics would only add about 20 kilograms (44 lb) to the roof of a house.”
The team’s testing also showed that the fabric solar panel could be rolled up and unrolled more than 500 times while retaining 90% of its power generation capabilities, boding well for its durability. Among the problems the team is working to address from here is the issue of environmental degradation, with some form of ultrathin packaging needed to protect the solar cell from the elements.
“Encasing these solar cells in heavy glass, as is standard with the traditional silicon solar cells, would minimize the value of the present advancement, so the team is currently developing ultrathin packaging solutions that would only fractionally increase the weight of the present ultralight devices,” said Jeremiah Mwaura, a research scientist in the MIT Research Laboratory of Electronics.
If these kinds of problems can be solved, the thin profile and light weight of the solar cells could see them find all kinds of uses. Applying them to the sails of a boat, the outside of tents in disaster recovery scenarios or the wings of drones are some of the examples offered, but in theory they could be deployed just about anywhere for the purposes of power generation.
The research was published in the journal Small Methods.
Source: MIT