Lancaster, California will be home to a "greener than green" trash-to hydrogen production plant three times the size of any other green H2 facility. SGH2 says its process is the cleanest of all on the market, while matching the price of the cheapest producers – and pulling tens of thousands of tons of garbage out of landfills.
For better or worse, many world economies are gearing up to make hydrogen a significant part of the future energy economy. Japan and Korea in particular are making big moves and enormous investments to get this zero-local-emissions energy storage format up and running.
Production of hydrogen can vary from the relatively green (electrolysis of fresh water using solar or wind-based energy) to the profoundly filthy (gasification of brown coal) – and the filthiest are by far the cheapest. Adding carbon capture and sequestration to dirty processes simply makes them more expensive.
That's what makes this SGH2 project so interesting – the company claims it can take trash that would otherwise sit in a landfill and rot, and turn it into super-green hydrogen at bargain-basement prices.
According to a recent memorandum of understanding, the city of Lancaster will host and co-own the SGH2 Lancaster plant, which will be capable of producing up to 11,000 kg of H2 per day, or 3.8 million kg per year, while processing up to 42,000 tons of recycled waste per year. Garbage to clean fuel, with a US$2.1 to $3.2 million saving on landfill costs per year as a sweetener.
"We are the only company in the world delivering green hydrogen that is cost competitive with the cheapest, dirtiest hydrogen made from coal and gas, and much less expensive than other green hydrogen" says SGH2 CEO Dr. Robert Do. "Our technology can scale quickly and produce fuel 24/7, year-round."
How it works
The process, developed by SGH2's parent company Solena, uses high-temperature plasma torches putting out temperatures between 3,500 and 4,000 °C (6,332 to 7,232 °F). This ionic heat, with oxygen-enriched gas fed in, catalyzes a "complete molecular dissociation of all hydrocarbons" in whatever fuel you've fed in, and as it rises and begins to cool, it forms "a very high quality, hydrogen-rich bio-syngas free of tar, soot and heavy metals."
The process accepts a wide variety of waste sources, including paper, old tires, textiles, and notably plastics, which it can handle very efficiently without toxic by-products. The bio-syngas exits the top of a plenum chamber, and is sent to a cooling chamber, followed by a pair of acid scrubbers to remove particulate matter.
A centrifugal compressor further cleans the gas stream, leaving a mixture of hydrogen, carbon monoxide and carbon dioxide. This is run through a water-gas shift reactor that adds water vapor and converts the carbon monoxide to carbon dioxide and more hydrogen gas. The two are separated, neatly capturing all the CO2 as hydrogen comes out the other end.
A Berkeley Lab lifecycle carbon analysis concluded, says SGH2, that each ton of hydrogen produced by this process reduces emissions by between 23 and 31 tons of CO2 equivalent – presumably counting emissions that would be created if the garbage was burned instead of converted into hydrogen. That would be between 13-19 tons more carbon dioxide avoided than any other green hydrogen production process.
What's more, while electrolysis requires some 62 kWh of energy to produce one kilogram of hydrogen, the Solena process is energy-positive, generating 1.8 kWh per kg of hydrogen, meaning the plant generates its own electricity and doesn't require external power input.
The 5-acre facility, in a heavy industrial zone of Lancaster, will employ 35 people full-time and create some 600 jobs in construction. SGH2 is hoping to break ground in Q1 2021 and achieve full operational status by 2023. The company is in negotiations with "California's largest owners and operators of hydrogen refueling stations" to buy the plant's entire output for a 10-year period.
SGH2 says it has demonstrated the technology at a full-size 7-year project in Pennsylvania, now dismantled, and a plasma torch testing facility in the Czech republic. The company says the technology "has been vetted and validated, technically and financially, by leading global institutions including the US Export-Import Bank, Barclays and Deutsche Bank, and Shell New Energies’ gasification experts." It has however, according to Power Magazine, not yet raised the US$55 million needed to build the plant.
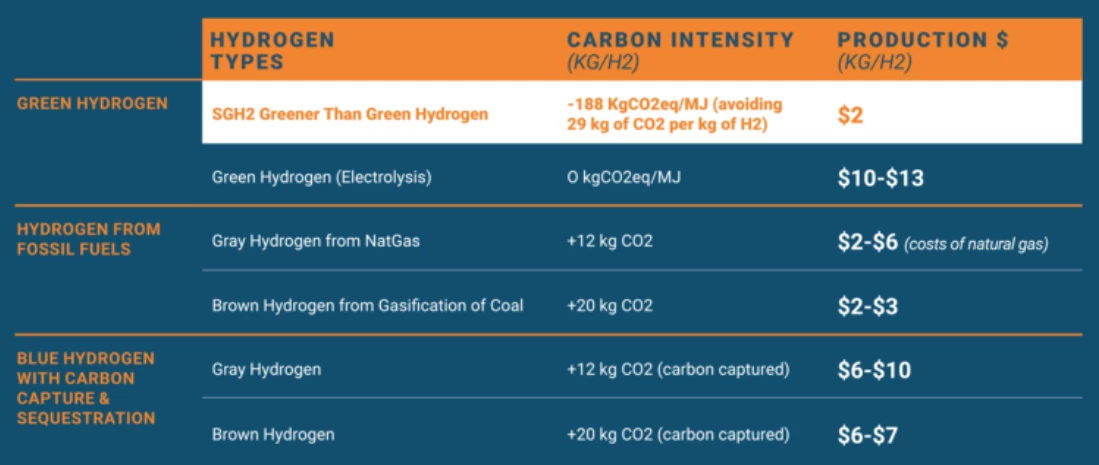
The numbers SGH2 presents are very attractive. We're not sure which methodology has been used to calculate the production costs, though, because they sure don't match up with the numbers in this 2019 Hydrogen Production Cost study, which shows several production methods coming in well under the US$2 per kg mark, and solar PV electrolysis costing as little as US$5.78 per kg. Perhaps the SGH2 table includes the capital costs of building each facility.
Either way, the pump price of hydrogen needs to get down around US$8 per kg before it roughly matches the per-mile cost of gasoline, assuming US$3.50/gallon (according to the California Fuel Cell Partnership). A production price around US$2 per kg should make that eminently possible.
We look forward to hearing more about this project; if hydrogen is going to happen as a substantial part of the new energy economy – and it certainly will, in Japan and Korea at the very least – then a cost-competitive and super-green way to produce it, while reducing landfill waste and disposing of difficult plastics, sounds like an excellent step in the right direction.
The company says it's in negotiations for similar projects in France, Saudi Arabia, Ukraine, Greece, Japan, South Korea, Poland, Turkey, Russia, China, Brazil and Australia.
Source: SGH2