Living coral reefs consist of rigid porous "skeletons" inhabited by the tiny coral polyps that built them. A new research project aims to restore damaged reefs faster than ever, utilizing 3D-printed skeletons made of the same material as the real thing.
First of all, there have been other projects that attempted to encourage the regrowth of coral by placing artificial skeletons on existing reefs. In most cases, though, those skeletons were made of materials such as concrete or polymers.
This means that waterborne coral polyps arriving at the reef have had to secrete calcium carbonate onto the structures, in order to "make them their own." Given that some corals grow at a rate of just a few millimeters per year, it can take quite a long time to rebuild reefs in this fashion.
Seeking to speed things up, scientists at Saudi Arabia's King Abdullah University of Science and Technology (KAUST) have developed a technique for producing skeletons made entirely of calcium carbonate. Known as 3D CoraPrint, the process begins with a 3D scan being performed on a natural coral skeleton. From there, either of two printing methods can be used.
In one scenario, the resulting 3D computer model is used to print a replica of the skeleton, made of an ordinary material such as plastic. That model is then used to create a silicone mold, which is subsequently filled with an "eco-friendly and sustainable" calcium carbonate ink. Once that ink cures in response to exposure to light, the finished calcium carbonate skeleton is removed from the mold.
The other option is to simply 3D-print the replica skeleton directly out of the calcium carbonate ink, which cures as it's deposited on the print bed. In either case, the finished product is then seeded with small fragments of live coral, in order to jumpstart the polyp colonization process once the artificial skeleton is placed on the reef.
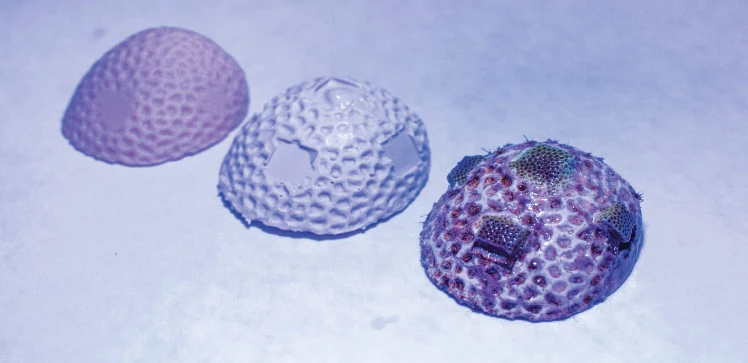
According to the researchers, both printing techniques have their pluses and minuses. If a mold is created, then many skeletons can be cast from that mold in quick succession, but they have to be relatively small in order to allow the ink to cure. Direct 3D printing takes longer, but allows for larger skeletons in a variety of shapes.
"With 3D printing and molds, we can get both flexibility and mimicry of what’s already going on in nature," says Zainab Khan, who is leading the study along with Charlotte Hauser and Hamed Albalawi. "The structure and process can be as close as possible to nature. Our goal is to facilitate that."
The research is described in a paper that was recently published in the journal ACS Sustainable Chemistry & Engineering.
Source: KAUST