After sugarcane crops have been harvested, a great deal of fibrous stalk waste known as bagasse is left over. That substance has been incorporated into an eco-friendly building material called Sugarcrete, which recently won an international Climate Positive Award.
First announced last May, Sugarcrete was developed via a partnership between the University of East London and British firm Tate & Lyle Sugars.
The material consists of sugarcane bagasse combined with proprietary mineral-based binders. This mixture is compressed and left to cure, resulting in high-strength blocks that can be used in place of traditional clay or concrete bricks.
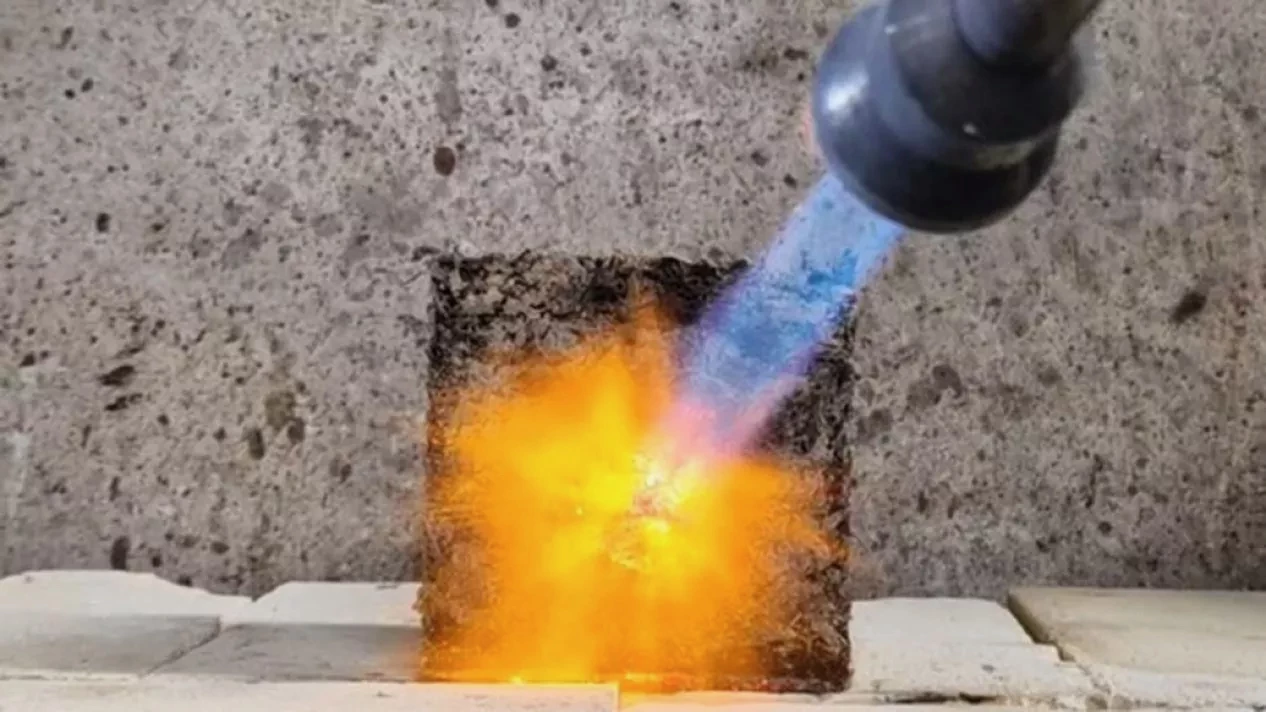
But why would anyone want to make such a substitution?
Well, for starters, the university claims that Sugarcrete fully cures much faster than concrete (one week as opposed to four), it weighs one quarter to one fifth as much per same-sized block, and it's significantly less expensive to produce.
The latter is a particularly big consideration in regions where sugarcane is grown. Instead of being left with a waste product that is often just dumped in landfills, farmers could sell their bagasse to local companies which would use it in Sugarcrete. That material could in turn be utilized in local construction projects, which might not have been affordable if imported concrete was the only option.
Additionally, Sugarcrete's carbon footprint is reportedly only 15% to 20% that of concrete. According to some estimates, the generation of the heat used to produce traditional portland cement (which is used in concrete) is responsible for 5% to 8% of all human-made CO2 emissions.
Sugarcrete has already been demonstrated in prototype modular floor slabs, in which loads are distributed throughout the structure via connections between interlocking blocks. Although some steel reinforcements are utilized, the Sugarcrete slabs utilize up to 90% less steel than slabs made of concrete, which is more likely to crack under pressure.
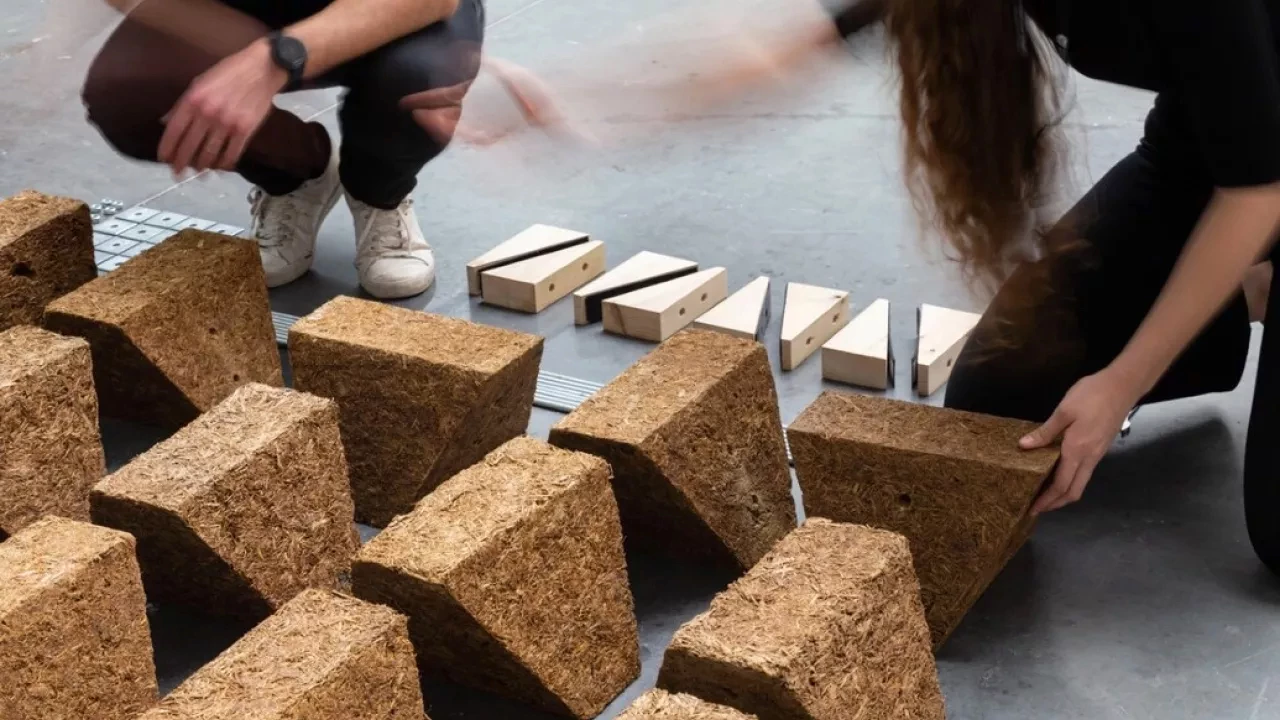
Late last year at the United Nations Climate Change Conference, environmental group Green Cross UK selected Sugarcrete to be the winner of the circular economy section of its Climate Positive Awards. The awards recognize initiatives that address climate change, with the circular economy section aimed specifically at projects which reduce waste by reusing existing materials.
The Sugarcrete team is now seeking agricultural partners in the Global South nations as a next step towards commercialization of the technology.
Source: University of East London