In an attempt to combine the vertical take-off and landing (VTOL) capabilities of a helicopter, with the speed, range and altitude capabilities of a fixed wing aircraft, tiltrotor aircraft, such as the AgustaWestland AW609 and the Bell Boeing V-22 Osprey rely on powered rotors mounted on rotating shafts or nacelles at the end of a fixed wing. But the tiltrotor design isn’t the only option for aircraft looking to get the best of both worlds. Like Aerovironment’s SkyTote, the Flexrotor is designed to transition from vertical to horizontal flight without any pivoting of its rotor.
Having been awarded a contract earlier this week by the Office of Naval Research (ONR), Aerovel Corporation will enter the next development phase for the Flexrotor, which is intended to deliver improved maritime surveillance capabilities. With the requirement that it launch from a ship, the unmanned aerial vehicle (UAV) has a wingspan of 3 m (9.84 ft) and an oversized rotor with a diameter of 1.85 m (6.07 ft).
The size of the propeller is designed to strike a balance between providing enough lift to enable the aircraft to take off vertically, while also being small enough to be efficient during horizontal flight.
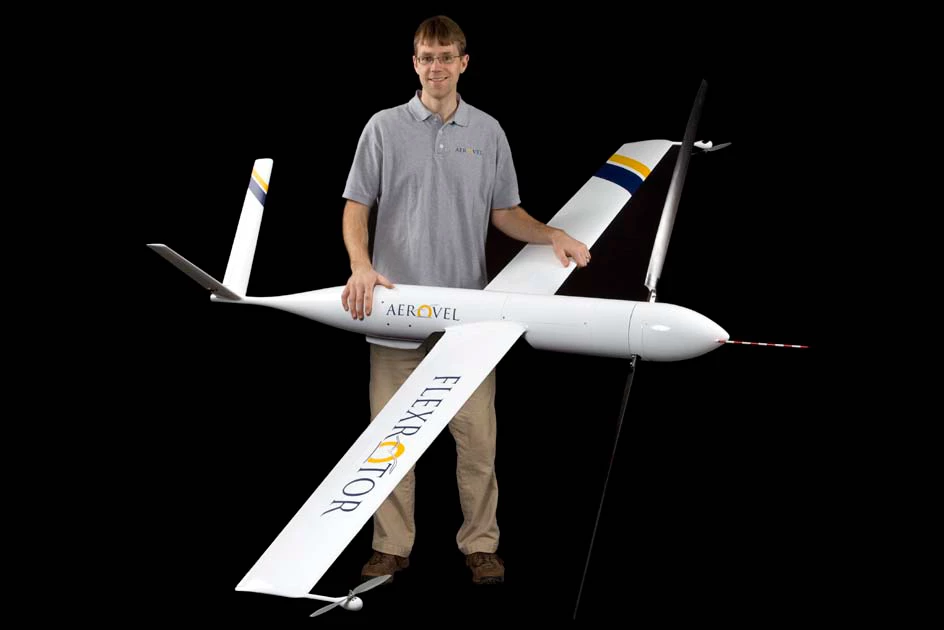
Currently powered by a single-cylinder 28 cc two-stroke engine through a reduction gearbox, the Flexrotor takes off vertically like a helicopter from a portable fold-out rig that supports the wings. Once airborne, the tail is deployed and, once it reaches a high enough altitude, it transitions into horizontal flight by pitching over into a dive before leveling out. To transition back to vertical flight, the aircraft flies at about 70 knots (80 mph/130 km/h) before pulling up and entering a hover that allows it to descend vertically and land.
The aircraft completed its first successful transition from vertical to horizontal flight and back again in August 2011, which can be seen in the video below. This and subsequent test flights have been conducted in light winds, but Aerovel plans to gradually increase the aircraft’s operating envelope and expose it to windier conditions. The development of an upgraded propulsion system to allow the aircraft to cope with crosswinds and high winds will be the focus of the next development phase.
Aerovel is also creating an Automatic Servicing Platform from which the Flexrotor could launch, land, park and refuel with no human assistance. In addition to placement on a ship, the platform could also be used to remotely site the aircraft for launch.
“[The special ops personnel] like the idea of not exposing where they are when they need to launch and recover one,” said John Kinzer, ONR program officer for Air Vehicle Technology. “They could put it on a mountaintop somewhere and just leave it to do surveillance.”
At its maximum vertical take off weight of 19.2 kg (42.3 lb), the Flexrotor can climb at a rate of 1 m/s (197 ft/min). After making the transition to horizontal flight, the aircraft boasts a maximum level speed of 78 knots (90 mph/145 km/h) and can stay in the air for more than 40 hours to reach a maximum range of more than 3,000 km (1,865 miles).
Here's the video of the Flexrotor making its first successful transition from vertical to horizontal flight.