Construction is the world’s largest industry, employing seven percent of the planet's working-age adults, contributing 13 percent of the world’s GDP and completing floor space equivalent to the city of Paris every seven days.
The construction industry is also the most inefficient, least digitized and most polluting industry (according to the UNEP, it accounts for 37% of ALL emissions), so change is imperative from macro economic necessity alone. For the builders of the world faced with a jigsaw puzzle of partial digital solutions and chronic labor and supply chain issues, the margins are growing ever-thinner and the necessity is to change or perish.
British company Automated Architecture (AUAR) has a thoroughly ingenious solution and it has enlisted an all-star cast of financial backers in short order: Morgan Stanley, ABB Robotics, Rival Holdings (USA), Vandenbussche NV (Belgium) with VCs such as Miles Ahead and Bacchus Venture Capital (Jim Horowitz et al) helping to get the initial idea off the ground.
AUAR partners with home builders and contractors in Europe and North America, licensing its micro-factory and all the digital technology to build low-energy homes at the price of normal homes, at any scale. The idea is to provide the tools to empower local ecosystems of communities, contractors, architects and developers to build better homes.
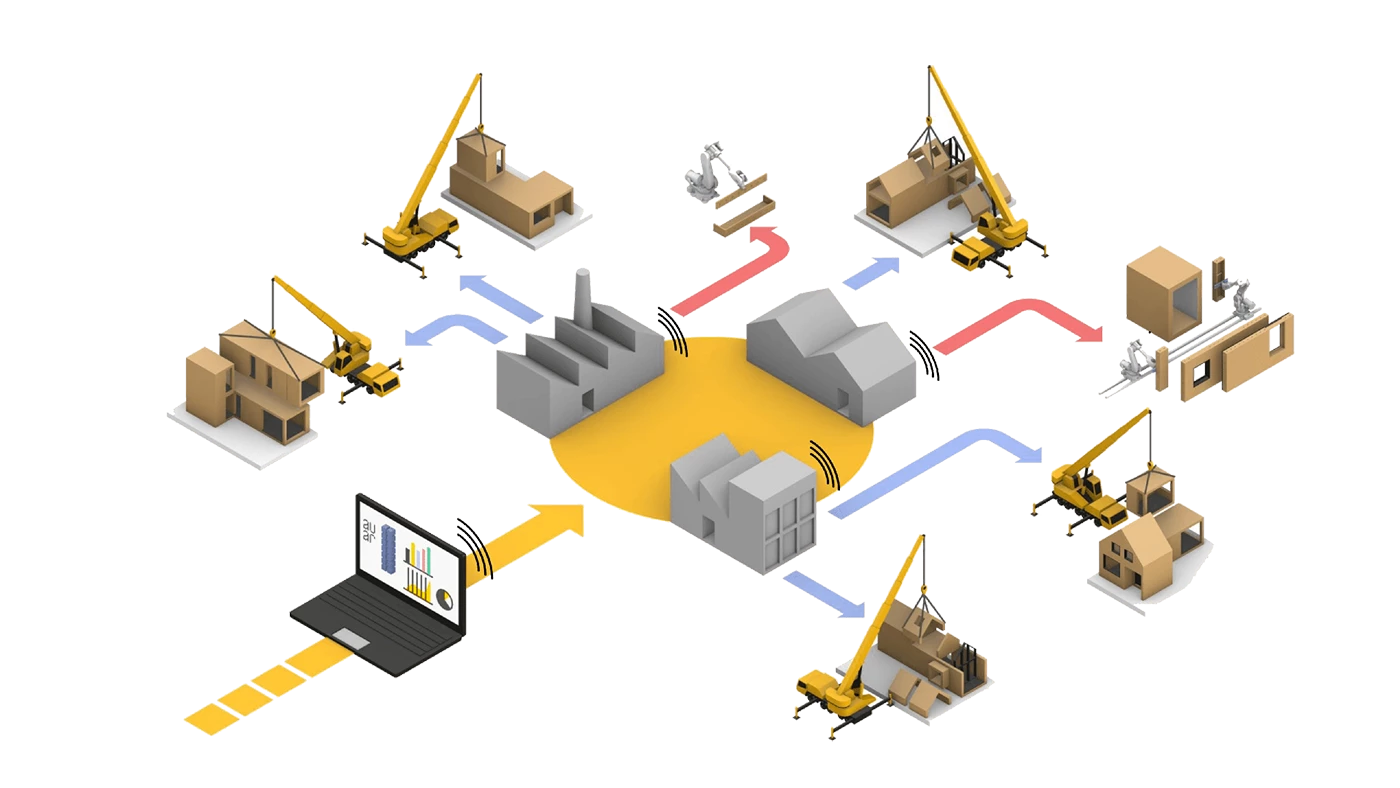
AUAR licenses the company’s low CapEx robotic micro-factories and the entire tech stack required to run them, with prices starting at $300,000 plus an ongoing licensing fee. Their licensees will be existing home builders, who will be able to build homes more cost-efficiently at any scale. AUAR's customer profile is a home builder with a minimum of £20m turnover per year. There's about 3,000 of these potential customers across EU and North America.
Given robots don't need sleep or pay and work considerably faster than humans (who are in chronic short supply), AUAR’s building system is expected to cut labor costs by 30% and supply chain, transport and logistics costs by 80%.
“The average home has about 7000 parts, each with a different supply chain,” says AUAR's co-founder and CEO Mollie Claypool. “We have one primary material, and only a few supply chains.”
“There is an urgent need for affordable low-energy homes, but building high-quality, sustainable timber homes is hard to scale, and AUAR intends to change that. Robots and AI allow us to deliver high-quality housing at significantly lower costs, increasing margins and productivity while lowering the cost for the end users. By using our solution, construction companies can hit their sustainability targets at a cost they are comfortable with.”
Each $300,000 AUAR micro-factory enables an approximate USD $1.3 million per year revenue creation opportunity for home builders, removing the barriers to the widespread adoption of robotics in the construction industry.
AUAR's system is already being deployed, with the first micro-factories opening in Europe last month, and conversations underway with potential partners in Canada, Spain, Sweden, Portugal, France and the Netherlands.
AUAR's first partner in the United States will be Indiana-based Rival Holdings, a company that emerged in 2023 with the merger of two already strong companies with the same vision. Ambassador Supply and VIA Developments formed one company to better enable their intention to operate at the forefront of change in the American construction industry, and AUAR was one of the company's first investments. Rival might be new in name, but it already operates 16 companies in 10 states, with over 800 employees.
Rival CEO Brad Crawford explained the creation of the venture company thus: “As our industry grows and evolves, it is critical that we focus on technology, innovation and disruption. Rival is a company that will work to catalyze innovation and growth, through a holistic view of the real estate and construction industry, and a willingness to take risks and explore possibilities.”
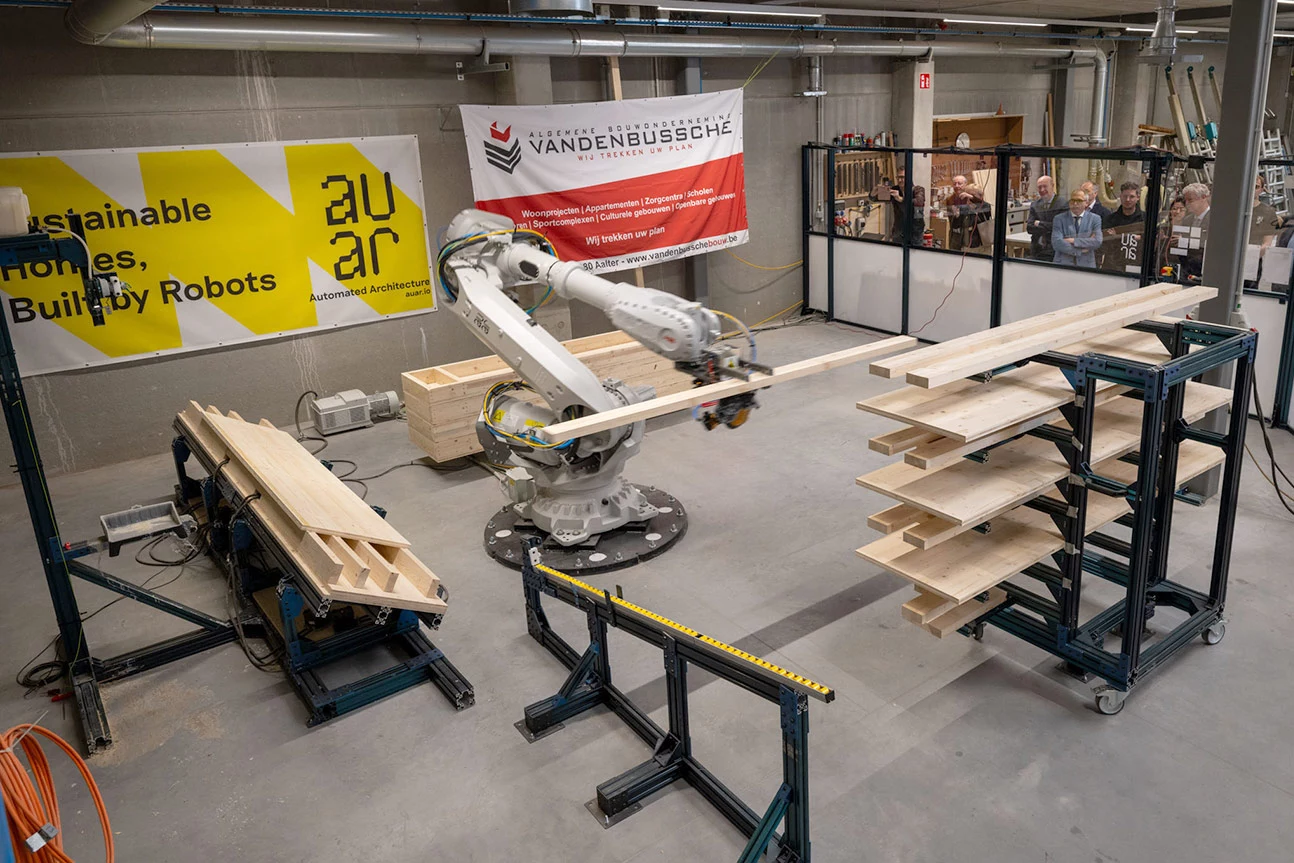
AUAR is targeting 40 licence partners for its micro-factories by 2030, with a capacity to produce over 75,000 energy-efficient homes by then, but clearly the industry is seeking a way to become more efficient and with two large partnerships in play already, the AUAR model also scales, and if the efficiencies can be proven, we expect this business model to be the path of least resistance between two massive needs.
McKinsey Global Institute’s March 2024 report on investing in productivity growth, summed up the imperative: “Today the world needs productivity growth more than ever. It is the only way to raise living standards amid aging, the energy transition, supply chain reconfiguration, and inflated global balance sheets.”
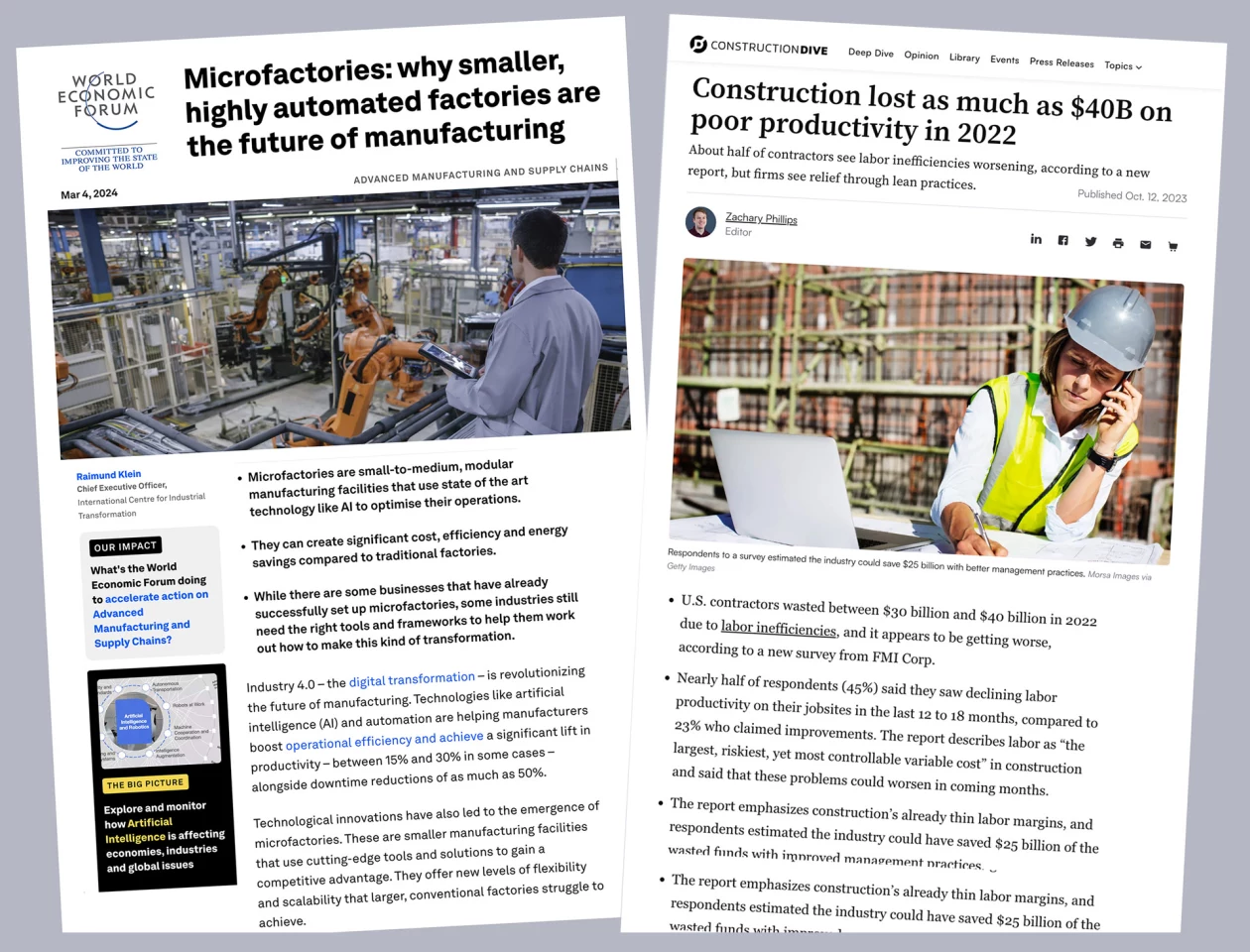
In a similar report on improving construction productivity from a global perspective, McKinsey wrote: “There’s a sense that the industry is on the verge of disruption, and industry players are actively working on new approaches. How organizations are preparing to deal with the disruption varies greatly—though most recognize that failure to adapt could result in being left behind.
“To cope with disruptive pressures, some have taken incremental approaches to adopting best practices by establishing small, discrete programs. Others have created transformational agendas designed to work within the current confines of the industry. Still others are making significant strategic bets to radically restructure the value chain or establish manufacturing-like systems of mass production.

It is unclear which approach will win in a given market segment—but understanding the challenge and the opportunity to address it is a crucial first step.”
The most heralded of the new enabling technologies coming to the construction industry is the micro-factory – a small-scale, high-tech automated manufacturing facility with a broad range of process capabilities that can be scaled up by replicating identical small cells in large numbers. AUAR's robot cells are quite compact, making it an affordable, quickly deployable and scalable solution.
In addition, the operating system uses AI, which makes it easy to generate a design and convert it into building elements. This means that the operator working with the robot only has to validate the process. As a result, this is the ideal solution to the productivity problem that the sector has been facing for years.
By 2030, the company aims to have a network of 40 partners and have its cells building 75,000 homes per year.
That might sound like an ambitious target, but we expect more success, more funding, and more scaling well before then.
We expect that once this model has proven itself, the rush will be on to transform the building sector and AUAR will be at the forefront of this change.
"I am convinced that we can help transform the housing market,” says AUAR's Mollie Claypool.
So are we.