A study conducted at Columbia University has revealed that even when stitched together from much smaller fragments, large sheets of graphene still retain much of their mechanical properties. The discovery may be a crucial step forward in the mass-production of carbon nanotubes that could be used to manufacture flexible electronics, ultra-light and strong materials, and perhaps even the first space elevator.
Graphene, the wonder-material
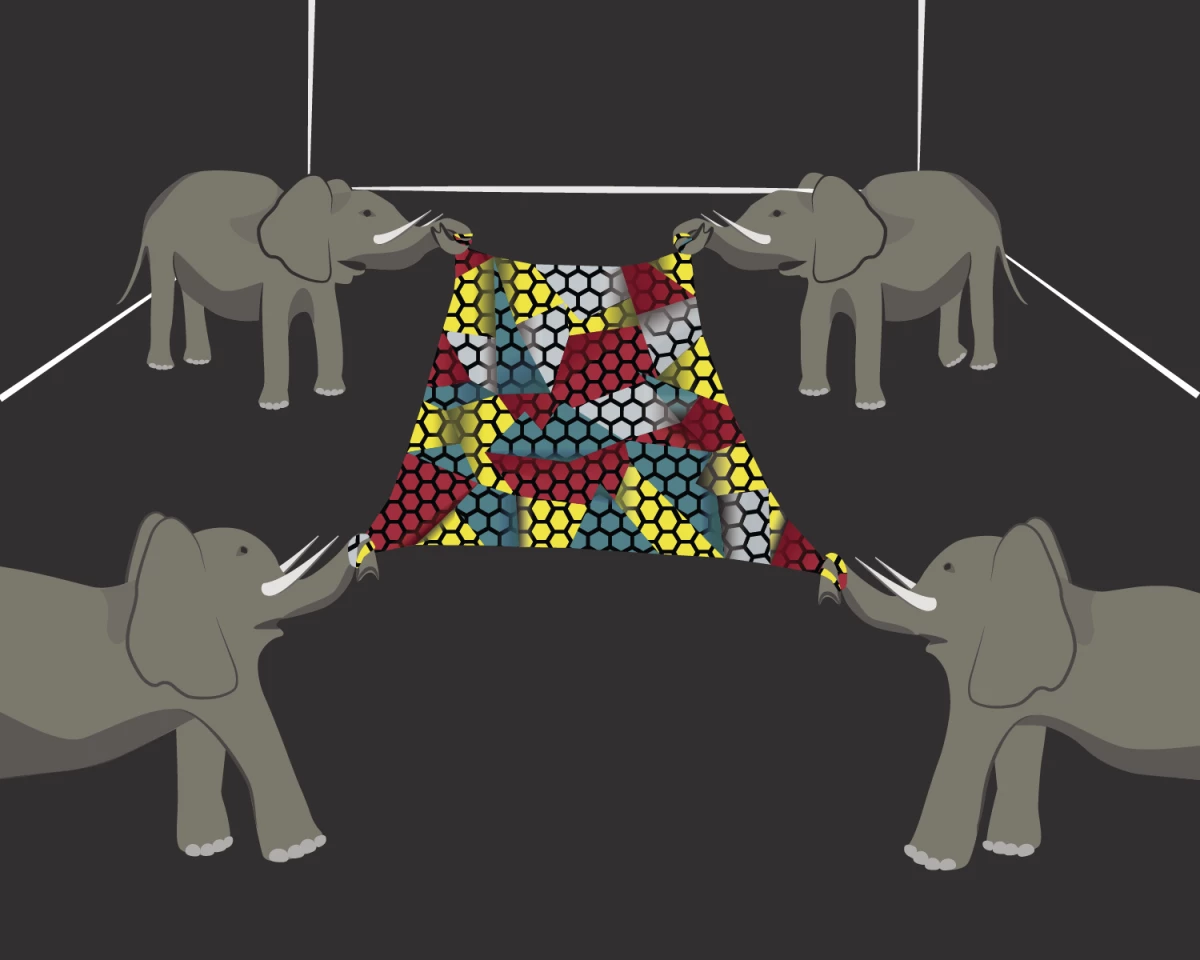
In its purest form, graphene is quite remarkable: it is the strongest material known to man, a great conductor of heat and electricity, and is both very stiff and very ductile. Graphene is also exquisitely light: at a mere 0.77 mg per square meter, a giant sheet covering the whole of the Unites States would weigh less than four space shuttles at launch.
Graphene derives the bulk of its strength from two factors. Firstly, each carbon atom is surrounded by six others in a highly stable honeycomb structure, with the atoms locked firmly in place by very strong covalent bonds; secondly, its extremely simple, two-dimensional structure leaves little room for weakening defects to appear in the lattice.
Researchers see in graphene a promising avenue to flexible electronics technology, leading to smart clothing, Harry Potter-style newspapers that can play videos on demand, and smartphones that unfold into full-sized tablets, to name a few. Graphene could also create high-performance composites to replace carbon fiber or, some researchers speculate, even a space elevator that could tether an artificial satellite to Earth (carbon nanotubes, which are rolled-up sheets of graphene, are the only known material with a strength-to-weight ratio high enough to pull off such a feat.)
Toward flexible displays
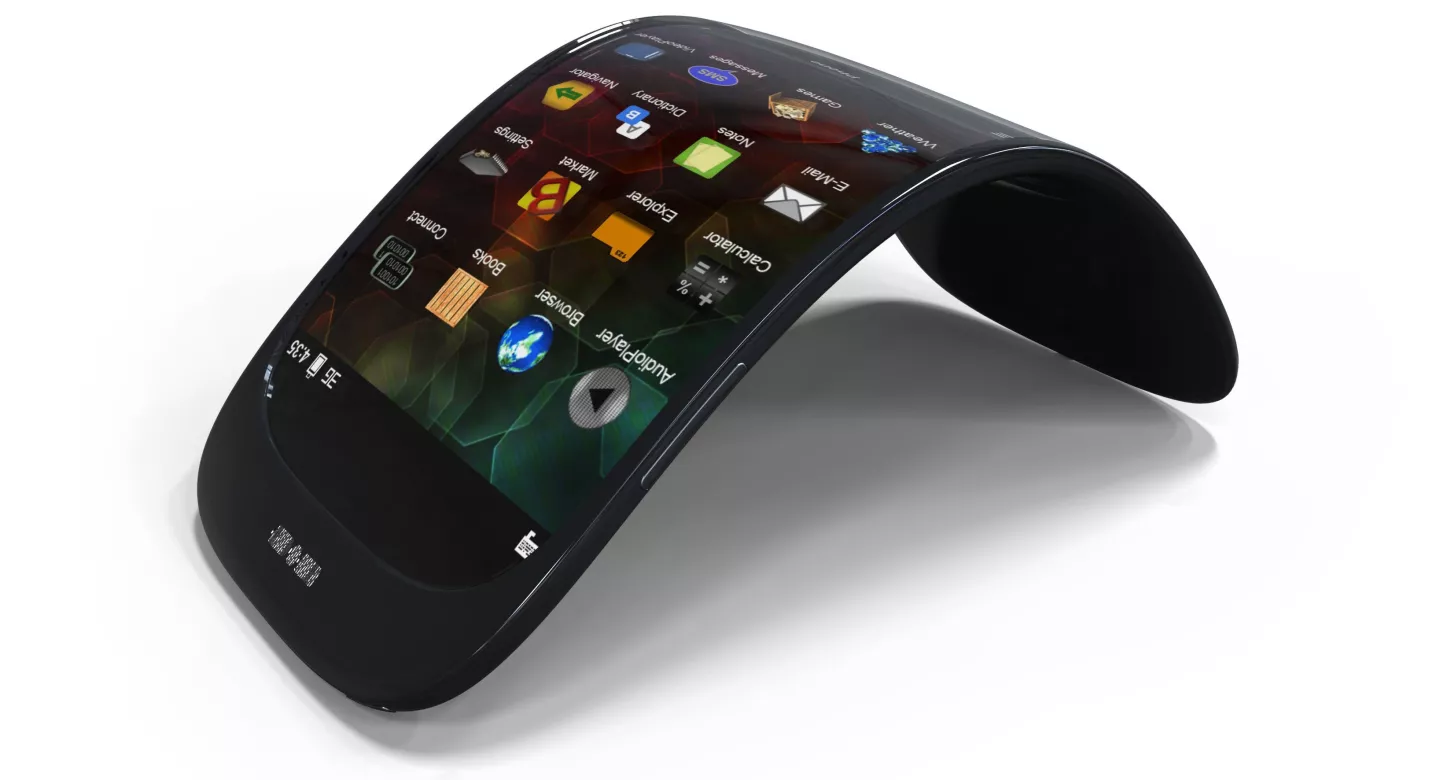
Scientists can manufacture very small quantities of pure graphene by mechanically peeling a graphite crystal. The process is adequate for the purposes of research, but it's also very costly and unpractical, so it can't be scaled up for mass production.
To create larger sheets of graphene (about as large as a TV screen), scientists rely instead on a procedure named "chemical vapor deposition" (CVD), in which single layers of graphene are grown inside a high-temperature furnace. The result isn't a uniform structure, but rather resembles a quilt made of small patches (grains) of graphene "sewn" over a thin layer of copper.
Theory dictates that CVD graphene sheets should retain nearly all the strength of their purest counterpart but, in past experiments, they have proven significantly weaker. Columbia University researchers James Hone and Jeffrey Kysar set out to find why, and discovered that what weakens the CVD graphene aren't the grains themselves, but rather the chemical used to remove the copper substrate after the grains have formed.
The team then developed a new process that uses a different etchant to remove the copper substrate, leaving the sheet undamaged. By doing so, they were able to create sheets of graphene that were just as strong as the material in its original, crystalline form.
When the sheet contained large grains, CVD graphene built in this matter tested exactly as strong as its purer, crystalline version; and, more surprisingly, even when the grains were much smaller the material still retained up to 90 percent of its original strength.
"This is an exciting result for the future of graphene, because it provides experimental evidence that the exceptional strength it possesses at the atomic scale can persist all the way up to samples inches or more in size," says Hone.
The researchers will now focus on studying other two-dimensional materials and how they are affected by the presence of grains. "Our work shows that grain boundaries in 2D materials can be much more sensitive to processing than in 3D materials," says Kisar. "This is because all the atoms in graphene are surface atoms, so surface damage can completely destroy the strength of these materials. However with appropriate processing that avoids surface damage, grain boundaries in 2D materials can be nearly as strong as the perfect, defect-free structure."
The study was published in a recent issue of Science.
Sources: Columbia University, Science podcast, Caltech