A new type of 3D-printed lattice structure has surprised researchers with its strength and light weight. It uses two different lattice structures merged together to eliminate the weak points normally found in these complex shapes.
RMIT researchers in Melbourne, Australia, took hollow-strut lattice designs as a starting point, inspired by hollow-stemmed water lilies and organ pipe coral, and then looked at ways to reduce the high stress concentrations created at the join points.
“Ideally, the stress in all complex cellular materials should be evenly spread,” said Distinguished Professor Ma Qian, lead author on a new study. “However, for most topologies, it is common for less than half of the material to mainly bear the compressive load, while the larger volume of material is structurally insignificant.”
The researchers reinforced the tubular lattice by overlaying a second lattice over the top, adding a thin X-shaped cross-section running through the tubes and joints that distributes load much more evenly in compression testing.
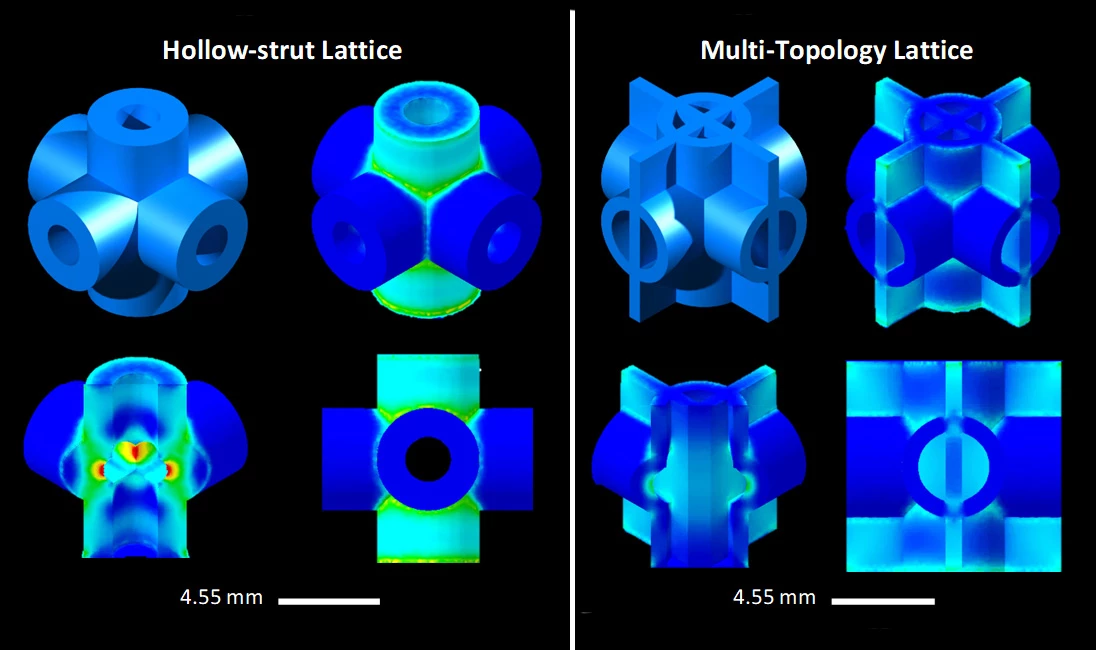
It's a highly complex shape, but easy enough to manufacture using a laser powder bed fusion 3D printer, and the researchers tested the resulting cube to find it 50% stronger than cast magnesium alloy WE54 – a material of similar density used in aerospace.
It'll scale, they say, from millimeters to several meters in size, depending on the printers available, and it offers temperature resistance up to 350 °C as is, or up to 600 °C with an upgrade to a more heat-resistant titanium alloy.
The researchers say it'll be useful in areas where strength and light weight are critical, naming aircraft and rocket parts among possible commercial applications. Interestingly, they also say it could be handy for medical bone implants, where the complex, partially empty shape may eventually fill up with regrown bone cells as it fuses with the body.
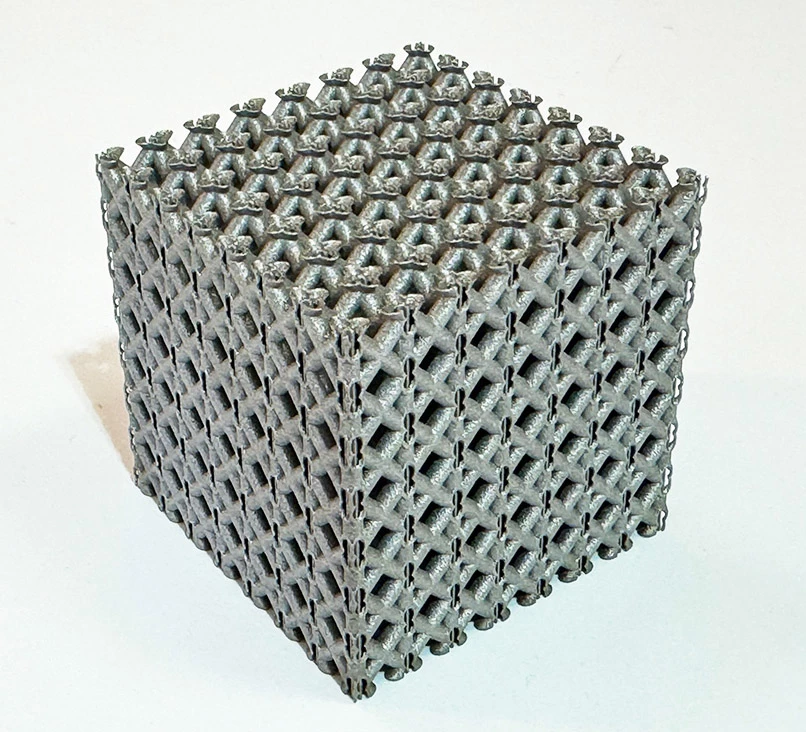
Will this be easy to manufacture? "Not everyone has a laser powder bed fusion machine in their warehouse,” admitted Qian. “However, as the technology develops, it will become more accessible and the printing process will become much faster, enabling a larger audience to implement our high-strength multi-topology metamaterials in their components. Importantly, metal 3D printing allows easy net shape fabrication for real applications.”
The RMIT team is calling for companies looking to collaborate on and commercialize these metamaterials across a range of applications, and says it will continue to refine the lattice design in search of higher strength and lower weight.
The paper is available in the journal Advanced Materials.
Source: RMIT