Materials that change their properties in response to certain stimuli could come to occupy a valuable space in many fields, ranging from robotics, to medical care, to advanced aircraft. A new example of this type of shape-shifting technology is modeled on ancient chain mail armor, enabling it to swiftly switch from flexible to stiff thanks to carefully arranged interlocking particles.
The material was developed by scientists at Singapore's Nanyang Technological University and Caltech in the US, who describe it as a type of "wearable structured fabric." In physics terms, its capabilities are enabled by what's known as a jamming transition, the same principle that causes vacuum-sealed rice or beans to stiffen when packed up tight, leaving the particles with little room to move.
The team set out to develop a fabric that can be easily transitioned from soft and foldable to rigid and load-bearing, pointing to the way Batman's cape can turn into a glider in 2005's Batman Begins, as an example. To do this, the team began investigating how structured but hollow particles could be interlocked to form a fabric with stiffness that could be altered on command.
“Inspired by ancient chain mail armor, we used plastic hollow particles that are interlocked to enhance our tunable fabrics’ stiffness," says study author Assistant Professor Wang Yifan. "To further increase the material’s stiffness and strength, we are now working on fabrics made from various metals including aluminum, which could be used for larger-scale industrial applications requiring higher load capacity, such as bridges or buildings.”
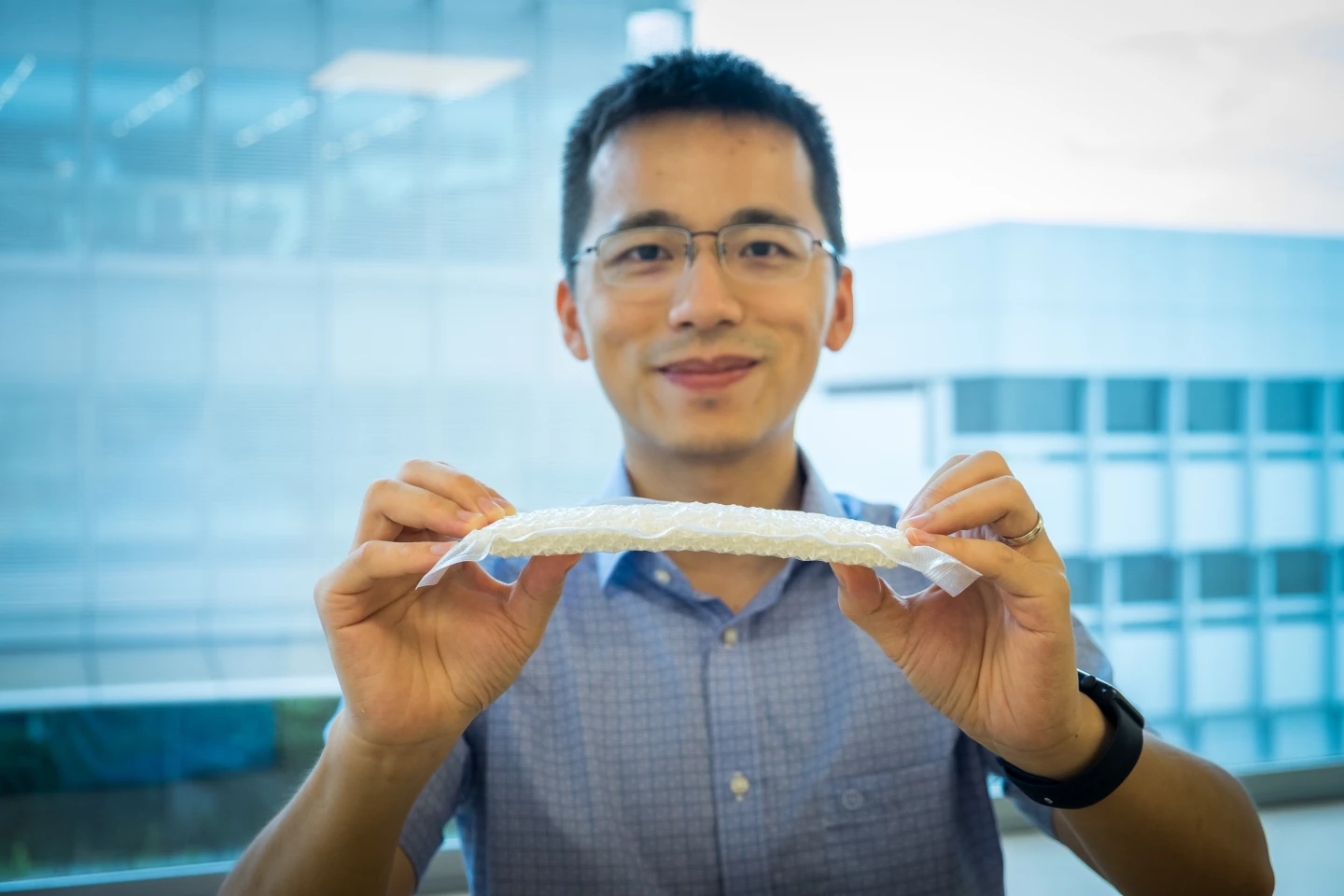
The team's octahedron-shaped particles are 3D printed with nylon plastics into a chain mail-like arrangement, which is then encapsulated in a plastic envelope and compacted using a vacuum. This increased the packing density, pulling the carefully designed particles in and increasing the points of contact between them, resulting in a structure that is 25 times more rigid.
When manipulated into a flat table-like structure, the fabric was capable of holding loads of 1.5 kg (3.3 lb), or 50 times its own weight. In another test, a small steel ball was dropped onto the fabric when it was relaxed, which saw it deform by up to 26 mm (1 in), and then dropped again when it was rigid, which only deformed it by 3 mm.
The scientists then 3D printed a version of the material using aluminum, which they found to have the same pliability and softness of the nylon version. But when "jammed" together, the material proved much stiffer, owing to the hardier attributes of aluminum compared to nylon.
Where a plastic envelope was used to encapsulate the nylon version, the team imagines this metallic version could be encapsulated with Kevlar to form a protective fabric for bulletproof vests. Other potential applications for either version include exoskeletons, adaptive casts that change stiffness as the patient heals, or even bridges that can be rolled out and stiffened on demand.
The team is now working to improve the performance of the material, and is investigating new ways it might be stiffened, with magnetism, temperature and electricity among the possibilities.
The research was published in the journal Nature, and the material is demonstrated in the video below.
Sources: Nanyang Technological University, Caltech