A pair of Princeton engineers have developed a new kind of concrete that promises more than 5 times the damage resistance of the usual stuff, by poking holes in its structure.
This could mean not only safer buildings, but it could also reduce our need to produce concrete to repair and rebuild structures – and that'd be great for the environment. Cement, which is used to make concrete, contributes to 3% of all greenhouse gas emissions worldwide, and every dent we can make in that figure helps.
For the new concrete, assistant professor of civil and environmental engineering Reza Moini and PhD candidate Shashank Gupta were inspired by the architecture of the dense outer shell of human thigh bones.
Also called cortical bone, it consists of elliptical tubular components known as osteons. Their shape, and the matrix in which they're arranged, deflects cracks around these osteons and prevents them from breaking apart all at once on impact.
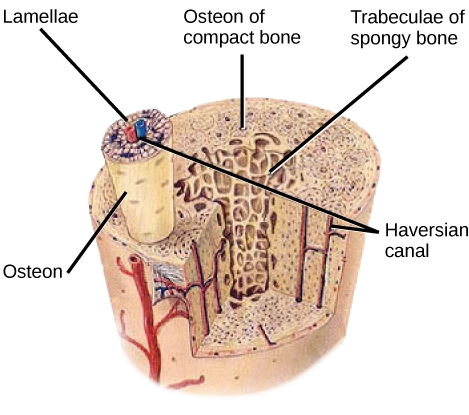
With its clever geometric design, this concrete's hollow tubes 'trap' cracks and delays them from spreading further. That's vastly different from other approaches to strengthen concrete, which involve adding materials like fibers and plastics to the mix.
"What makes this stepwise mechanism unique is that each crack extension is controlled, preventing sudden, catastrophic failure," Gupta explained. "Instead of breaking all at once, the material withstands progressive damage, making it much tougher.”
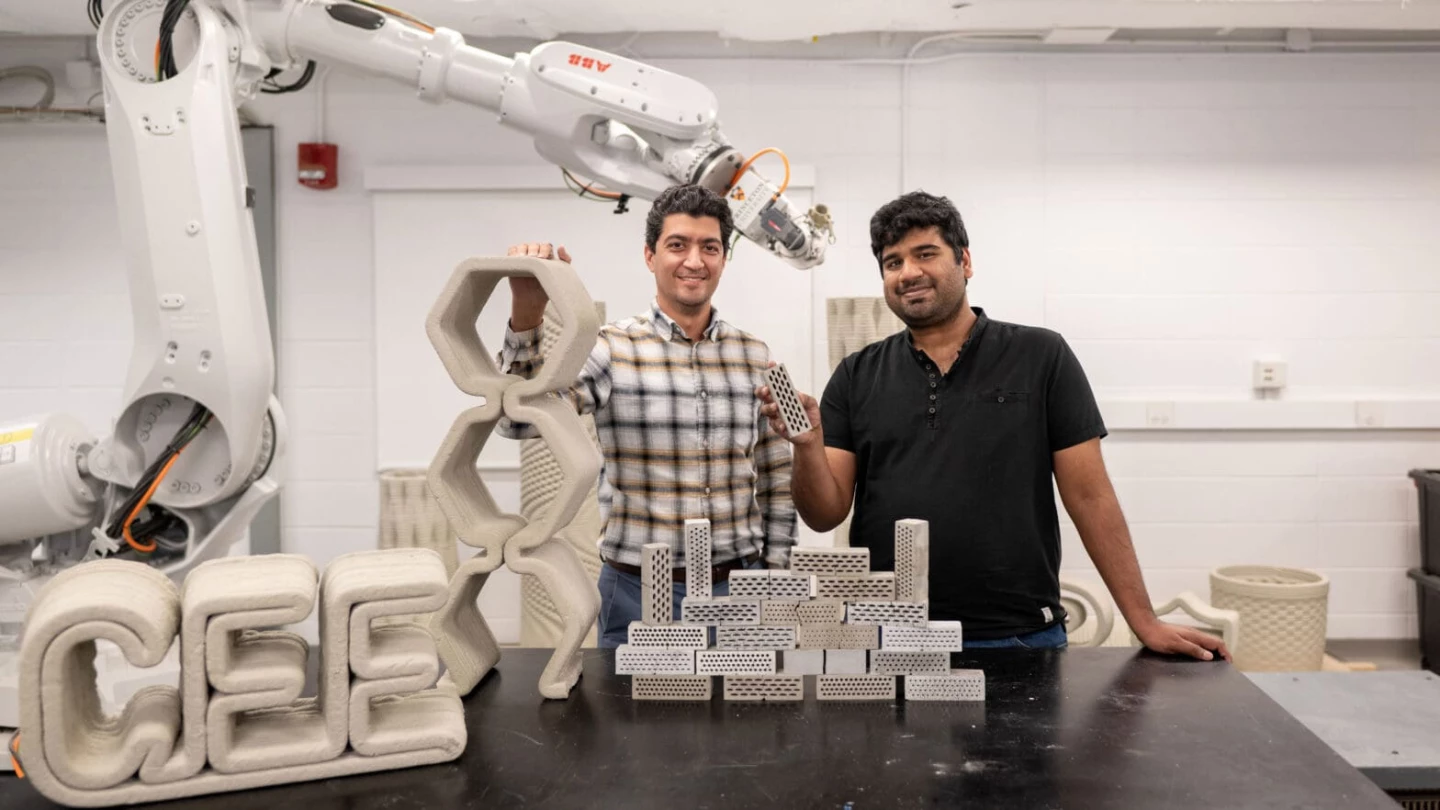
Making and breaking tougher concrete
To cast this bio-inspired concrete, the duo 3D printed a tubular template mold using polyvinyl alcohol (PVA). They then fabricated a negative of that template by pouring rubber into the mold. It's then dissolved to create a urethane silicon mold, and that's used to cast the concrete.
To test its toughness, they performed what are called a three-point bending test and a single-edge notch bend. Essentially, they used a 2-mm-thick diamond saw and a razor to cut notches into the concrete. This was repeated multiple times to gather data on the material's fracture toughness. Their findings were published in the journal Advanced Materials.
This isn't the first time the researchers have found inspiration for new materials in nature. Earlier this year, the team developed a cement composite that exhibited 17 times greater crack resistance than standard cement. The duo took cues from mother of pearl – found in crack-resistant oyster shells – which is made up of hexagonal tablets of aragonite joined by a biopolymer. That gave them the idea for their ultra strong composite material.
Concrete and cement are having a green moment this year. Back in May, we learned about a method to produce carbon-zero cement while purifying iron at the same time. And last month, we saw researchers in Japan combine CO2 and concrete rubble from a demolished school to make strong and reusable bricks for constructing new buildings.
Source: Princeton University