Concrete has been used in construction for thousands of years, it's everywhere. But its production is a major contributor to global carbon emissions, and we've seen much research aimed at reducing its environmental impact. One such project spun out of VTT Finland is looking to make concrete manufacture carbon negative.
The VTT Technical Research Centre of Finland has been looking into the negative effects of carbonation – the slow process where carbon dioxide gets reabsorbed by concrete over time and can lead to the corrosion of steel reinforcements – for decades.
In the late 2010s, researchers started to focus on turning these problems into an advantage. "We decided to develop carbon negative concrete without knowing exactly how to do it," said VTT senior scientist Tapio Vehmas. "We started experimenting in order to find out how carbon dioxide functions in concrete, how carboaluminates are formed, and how this process replaces cement and lowers the carbon footprint."
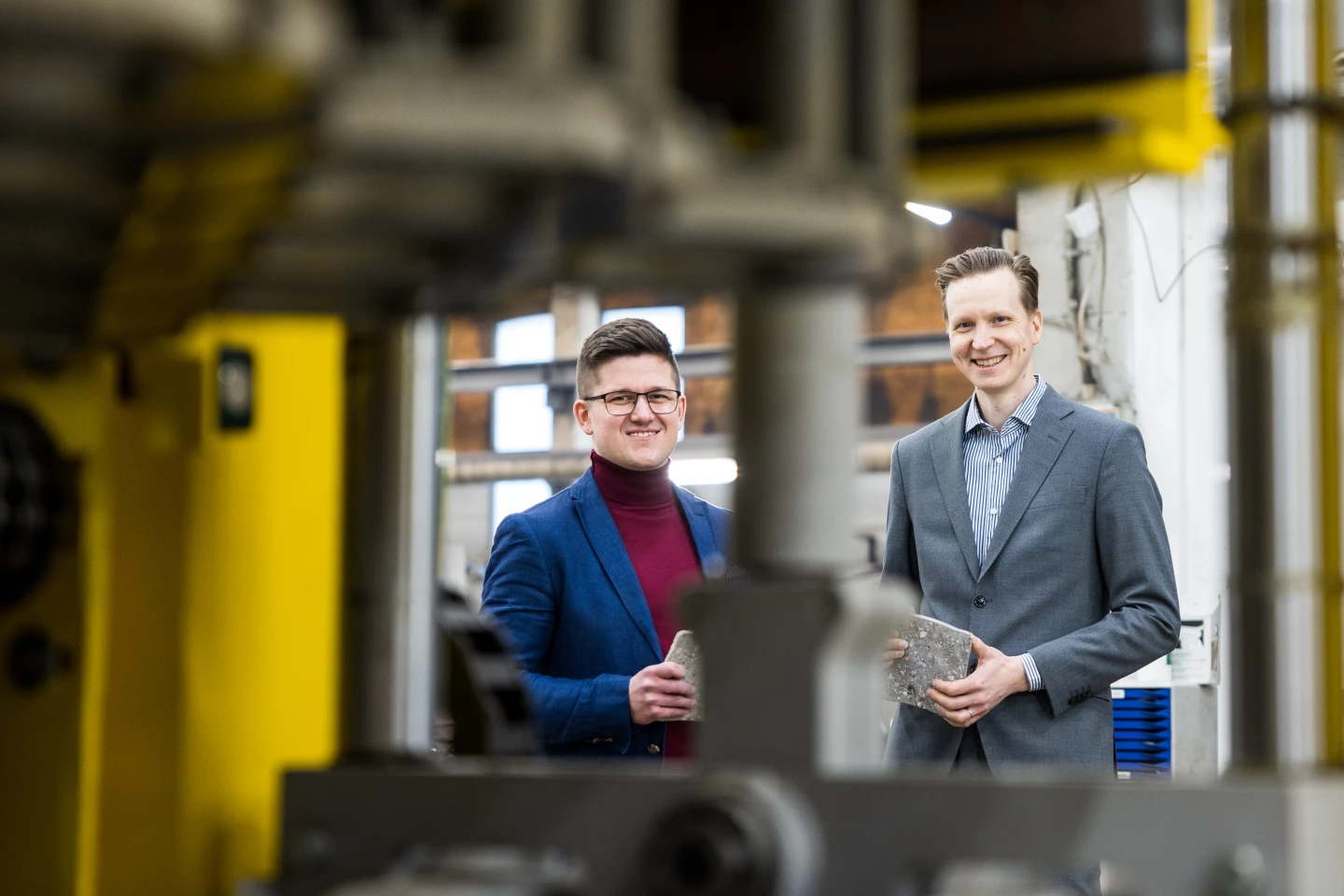
The search began for suitable low-carbon binders. Those experiments revealed that blast furnace slags from the steel industry could be carbonated, and worked well as an effective binder to replace normal cement in concrete.
"This did not work out straight away, but we had to develop the material concept and look for appropriate activators," added Vehmas. "The binder’s final material combination consisted of slags, green liquor dregs and bio-ash."
The project then turned its collective eyes to commercialization, building an automated carbonation pilot system that binds CO2 into precast concrete at atmospheric pressure, and installing it inside a container that was positioned next to a concrete plant in Hollola in southern Finland. Owner of that plant, Rakennusbetoni- ja Elementti Oy, subsequently used the technology to create carbon-negative yard paving for installation at a Skanska construction site.
"We have demonstrated in the pilot unit that our technology is capable of reducing the CO2 emissions of conventional concrete by 45%," said Vehmas, now CEO of VTT spin-out company Carbonaide. "Last autumn, we demonstrated lowering our products’ carbon footprint to -60 kg/m3 by replacing Portland cement with slag." The carbon footprint of conventional concrete is reported to be about 250-300 kg per cubic meter.
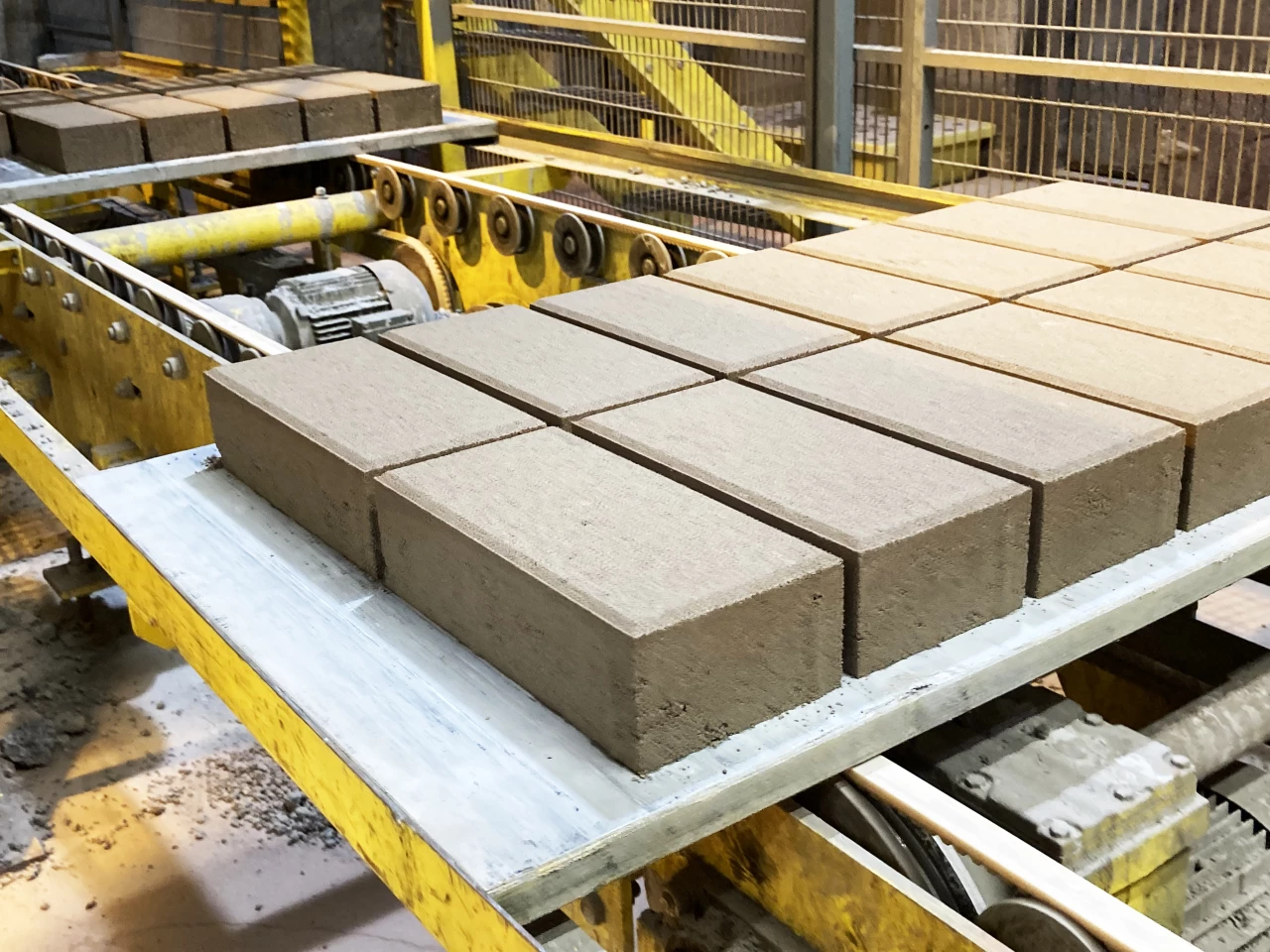
Carbonaide now intends to construct the world's first industrial pilot production line for the manufacture of carbon-negative concrete, and has secured seed funding of €1.8 million (about US$1.95 million) to get things started. The factory-sized unit in Hollola combined with a fully operational value chain are expected to "mineralize up to five tons of CO2 per day and increase production by 100-fold of its carbon-negative concrete products."
The company is aiming to scale up production and have 10 units in operation throughout the region by 2026, which are expected to bind around 500 megatons of CO2 each year by 2050. The current pilot can be seen in operation in the video below.
"Our goal at Carbonaide is to create a more sustainable future with cutting-edge tech that doesn’t just reduce the carbon emissions of construction materials like concrete, but that traps more CO2 than they emit throughout their lifetime," said Vehmas. "It is very natural that the constructed environment becomes a CO2 sink as it is the largest volume of man-made material."
Source: VTT