From residential homes and skyscrapers to art sculptures and footpaths, concrete is everywhere you look and it's difficult to imagine the modern world without it. As the most widely-used human-made material on Earth, it also plays a huge role in global carbon emissions thanks to its energy intensive production. This means that even slight adjustments to how we make it can have big impacts on its environmental footprint. And as research continue to show, scientists working in this space are not short of ideas.
Concrete has been used as a construction material for millennia and remains popular to this day, with good reason. It's cheap, it's strong, it's simple to make and it lasts a very long time. Global use of concrete today stands at around 30 billion tonnes annually, with demand only expected to increase from here.
The massive carbon footprint of concrete stems largely from one key ingredient: cement. This is added to sand, gravel and water to form wet concrete that can be poured into molds to form structures as they dry, but the production of cement is far and away the most carbon-intensive part of the process.
It involves using fossil fuels to heat limestone and clay to extreme temperatures, around 1,400 °C (2,552 °F). This not only requires huge amounts of energy, but the limestone needs to be extracted from the Earth and crushed up before being baked. This cooking process itself also releases vast amounts of stored carbon dioxide, around 600 kg (1,322 lb) worth for every ton of cement produced. All told, cement production accounts for around 8% of global carbon emissions.
Substitutes for limestone?
Limestone is a key ingredient in cement, and is therefore a key focus for scientists exploring more environmentally friendly alternatives. Last year, scientists at Stanford University cooked up a low-carbon cement recipe that swapped limestone for volcanic rock. This material needs to be treated in the same energy-intensive way to form cement, but doesn't contain any stored carbon that would be released throughout.
Also last year, another interesting approach came from scientists in Germany and Brazil, whose low-carbon cement recipe used an abundant mining waste material called Belterra clay, which could replace 50 to 60 percent of the limestone. This leaves more carbon locked away in the ground, and it can also be baked at lower temperatures. This material was found to meet the performance criteria for traditional cement, but with a recipe that cuts carbon emissions by up to two thirds.
One particularly interesting example of low-carbon cement came earlier this year from scientists at the University of Colorado Boulder, who were inspired by tiny microalgae that naturally sequester carbon dioxide and turn it into calcium carbonate shells they described as an "armor of limestone." The scientists were able to rear these microalgae and have them produce this biologically grown limestone, and then integrate that into cement production in place of mined material.
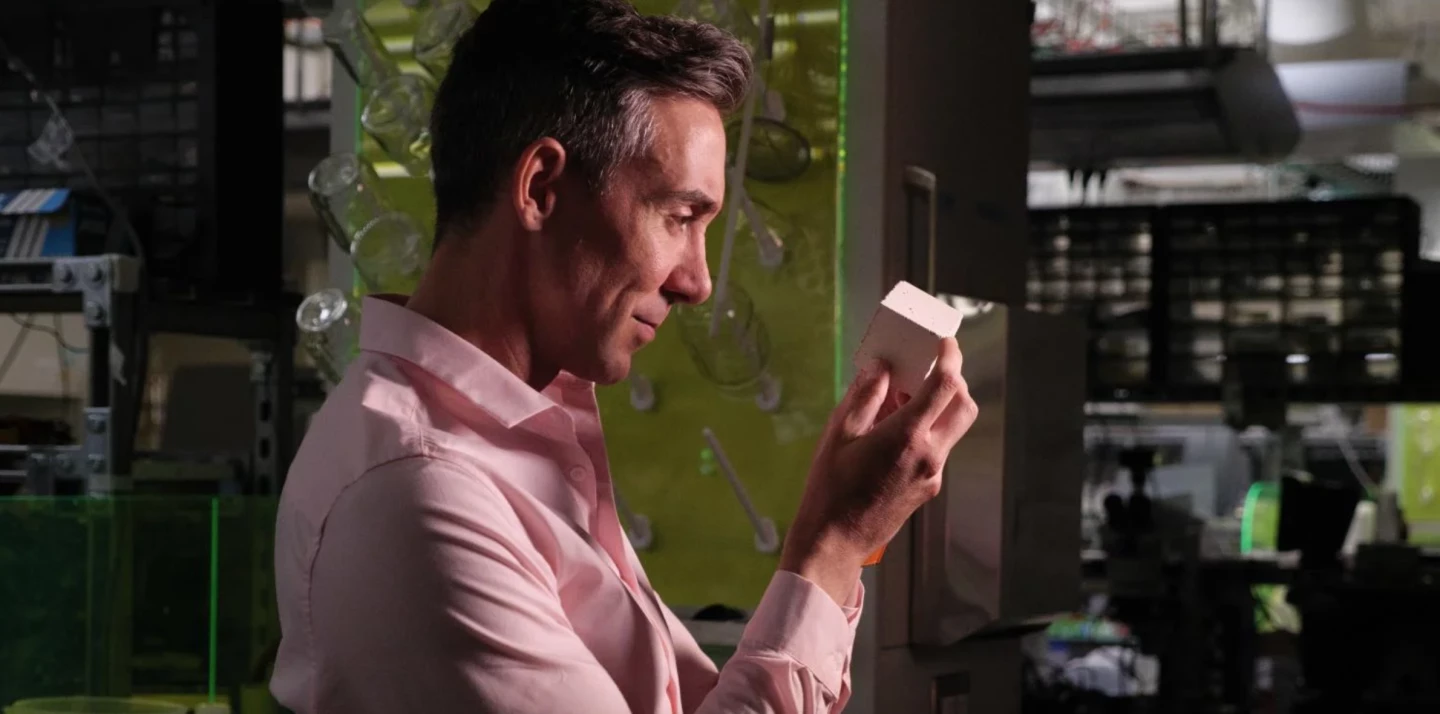
What made this bit of research so compelling, was that the resulting concrete not only looked and behaved like regular concrete, but could actually be carbon neutral or even carbon negative. This is because the microalgae capture more carbon dioxide to fuel the production of calcium carbonate than is generated through the process.
These scientists were awarded a US$3.2-million grant to work on scaling up production of their biogenic limestone and carbon-neutral concrete. They estimate that 1-2 million acres of open ponds would provide enough space to cultivate the microalgae needed to meet the cement demands of the US.
Concrete that lasts
While the resilience of concrete is one of its attractive characteristics, that doesn't mean there isn't room for improvement. When cracks form in concrete structures, for example, it invites water inside that can greatly compromise its strength. This can make them expensive to maintain or can even call for a complete replacement to prevent a catastrophic collapse. This indirectly increases the material's carbon footprint, but there are some interesting solutions in the mix.
These include forms of concrete that deploy a special glue to knit together its own cracks, and others that fill them in with fungus. One version of this self-healing concrete came from scientists at Worcester Polytechnic Institute last year, which used an enzyme found in human blood that could be worked into concrete powder before it is formed.
When a small crack forms in the concrete, this enzyme reacts with CO2 in the air to produce calcium carbonate crystals, which then go on to fill in the gaps. In testing, the concrete proved capable of repairing its own cracks within 24 hours, with the scientists predicting that the technology could extend the lifespan of concrete structures by 20 to 80 years.
One of the other ways scientists are looking to shore up the durability of concrete is, perhaps unsurprisingly, with the world's strongest artificial material. Incorporating graphene into concrete has been shown to make it stronger and more water resistant, and last year we got a first look at what shape it might take in the world.
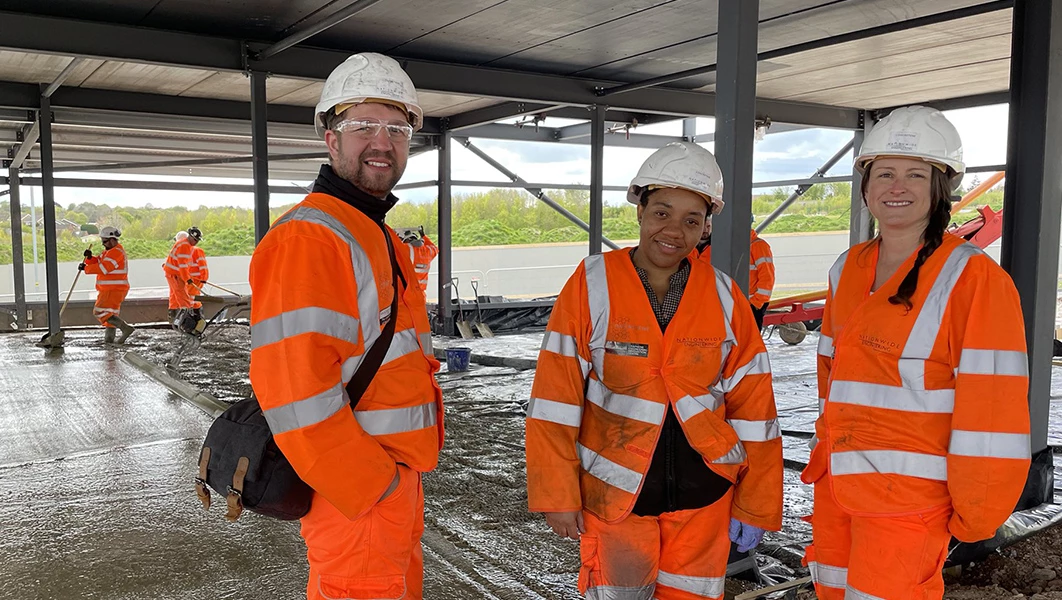
The University of Manchester's "Concretene" features tiny amounts of graphene added to the water and cement to act as mechanical support and boost the chemical reactions that turn the mix into concrete. The result is a concrete with stronger bonds, and around 30% higher strength. The material was poured into the world's first graphene-enhanced concrete slab in England last year, where engineers will monitor its performance.
The thinking is, that because Concretene is far stronger than traditional concrete, less of it needs to be used to bring the same structural strength to a building. The team working on it calculate that if it was deployed across the global supply chain, it could shave around 2% off worldwide emissions.
Addressing waste
Indeed, making concrete stronger and better performing may help coax manufacturers toward its greener forms, and that mightn't just relate to its immediate carbon footprint. We've seen scientists get quite creative with incorporating waste materials into concrete to help not just recycling, but also boost its capabilities.
In 2019, scientists at Australia's Deakin University took non-recyclable glass and ground it up into a coarse powder, which could be used in place of sand as an aggregate for polymer concrete, which proved significantly stronger.
Discarded rubber tires are another waste material attracting significant interest in these circles, which can be ground up and used in place of sand or gravel as an aggregate. Last month, researchers at RMIT University took an impressive step forward, showing off a form of concrete that featured 100% tire-rubber aggregate and showed significant improvements in compressive, flexural and tensile strength.
Back in 2017, MIT scientists developed a form of concrete that made use of irradiated plastic water bottles. Their approach involved exposing discarded plastic bottles to gamma radiation, before grinding them down and mixing them into cement along with fly ash. The resulting concrete proved 15 percent stronger than conventional concrete.
We're also seeing scientists seeking to address the mounting waste generated by the coronavirus pandemic. RMIT University researchers last month demonstrated yet another form of eco-friendly concrete that incorporated personal protective equipment (PPE), 54 tonnes of which they say is produced every day.
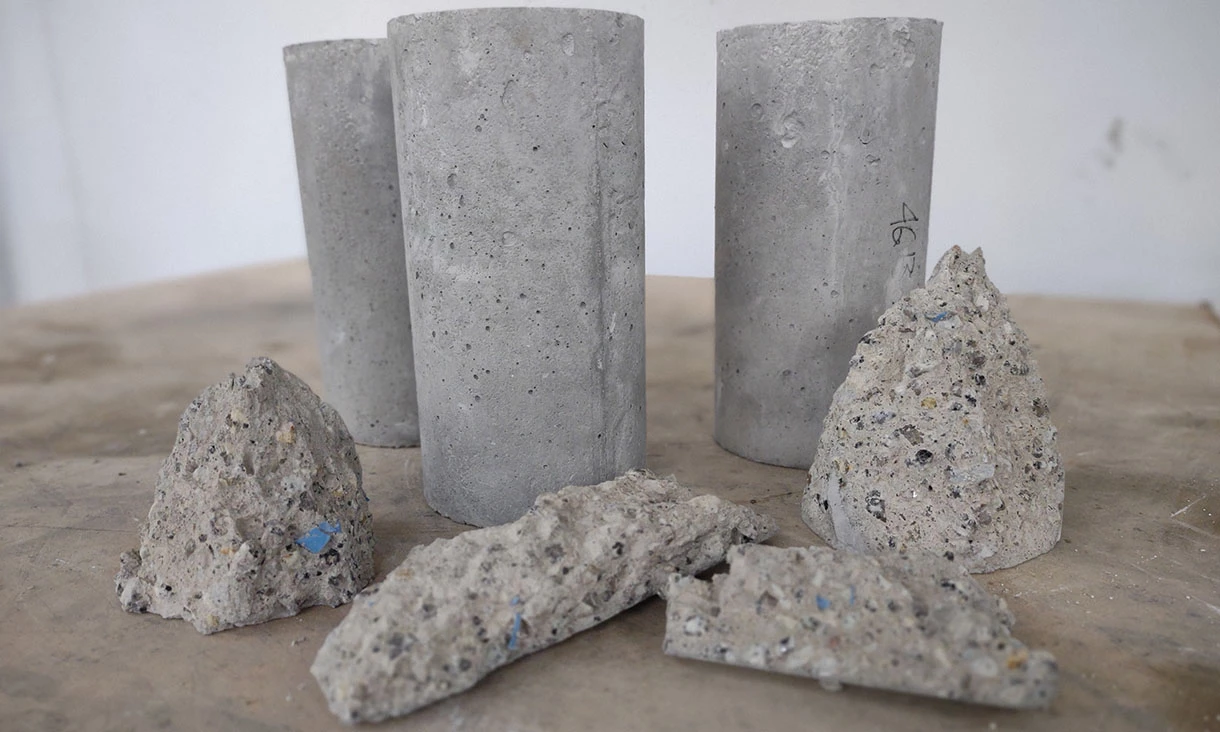
Gowns, face masks and rubber gloves were shredded and incorporated into concrete at different concentrations. The rubber gloves were found to boost compressive strength by up to 22%, while the face masks improved it by up to 17%. The shredded gowns improved compressive strength by 15%, elasticity by 12% and resistance to bending stress by up to 21%.
Towards greener construction
Given that these types of research projects and experimental concretes are still in their early developmental phases, there is a long way to go before we see them put any sort of dent in global carbon emissions. But they do illustrate the many possibilities when it comes to how we might lessen the environmental impact of this omnipresent material. Even small reductions in its carbon footprint could mark some big steps forward.