A couple of years ago, Canadian scientists celebrated the Christmas season by creating a microscopic gingerbread house. In that same spirit, Danish researchers have now produced what they claim is the world's thinnest Christmas tree – and it's made of graphene.
For those of you who are unfamiliar with the substance, graphene takes the form of a one-atom-thick sheet of carbon atoms, linked together in a honeycomb pattern. It's the world's thinnest, strongest manmade material, plus it's also very electrically and thermally conductive, and highly impermeable.
These characteristics make it quite useful in a variety of applications, such as batteries, electronic devices and high-strength composite materials. One challenge, however, lies in ensuring its quality while producing it on a commercial scale. That's why the Christmas tree was made.
Produced by scientists at the Technical University of Denmark (DTU), the object measures 14 cm (5.5 inches) in length, and is just one third of a nanometer thick – a nanometer is one billionth of a meter. It was cut from a 10-meter-long (32.8-ft) roll of graphene, which was produced by first "growing" graphene on a reusable roll of copper foil, then lifting the graphene off the copper and transferring it onto a roll of inexpensive polymer film for handling and storage.
While this is an established method of graphene production, it's still difficult to check that the graphene hasn't lost any of its functionality while being transferred from one roll to the other. The DTU team addressed that problem using terahertz radiation, which is considered harmless in small amounts.
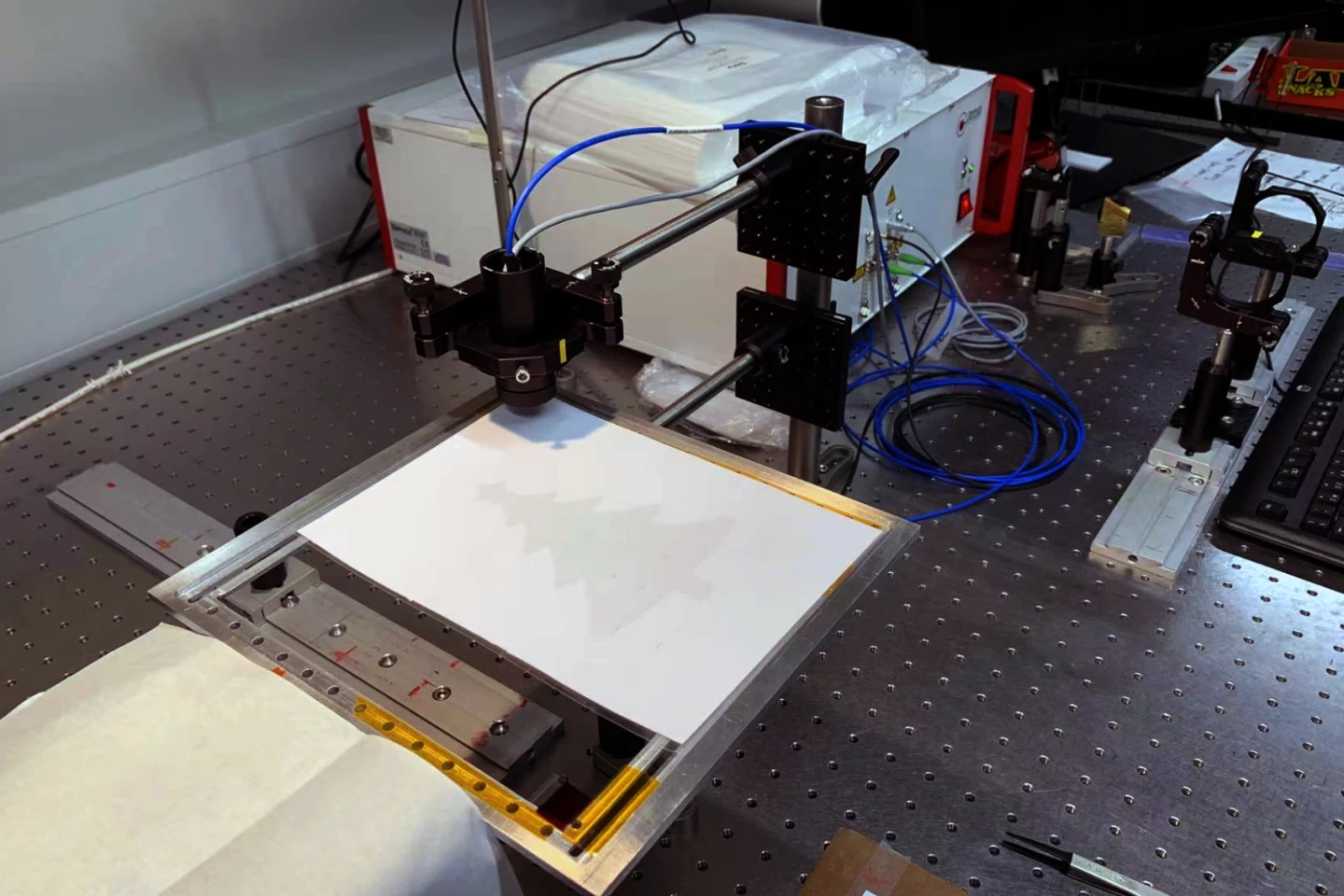
More specifically, once the graphene had been transferred onto the polymer, it was first subjected to terahertz radio waves, then scanned to see how much terahertz radiation it had absorbed. Graphene's ability to absorb such radiation corresponds directly to its electrical conductivity, so as long as the scans show that it's uniformly radiated, it should be good to go.
"Behind the Christmas [tree] joke hides an important breakthrough," says the lead scientist, Prof. Peter Bøggild. "For the first time, we managed to make an in-line quality control of the graphene layer while we transferred it. Doing this is the key to gaining stable, reproducible and usable material properties, which is the prerequisite for utilizing graphene in, e.g. electronic circuits."
The process is demonstrated in the video below.
Source: Technical University of Denmark