While titanium implants such as artificial hips can greatly improve patients' lives, they're also subject to serious bacterial infections. An experimental new antibacterial titanium alloy, however, could make such problems a thing of the past.
When pretty much any manmade object is implanted in the body, there's a chance that harmful bacteria will colonize its surface – and the surrounding tissue. The microbes go on to form a viscous coating known as a biofilm, which is resistant to antibiotics. For this reason, a second surgery is sometimes required to clean off and disinfect the implant.
In recent years, various groups have developed antibacterial coatings that can be applied to titanium implants. And while some of these coatings do show promise, they may wear off over time. Additionally, applying them to the implant adds just one more step to the production process.
That's where the new 3D-printable material comes in.
Developed by scientists at Washington State University, it consists mainly of a traditional titanium alloy but also contains 3% copper and 10% tantalum, the latter of which is a corrosion-resistant metal.
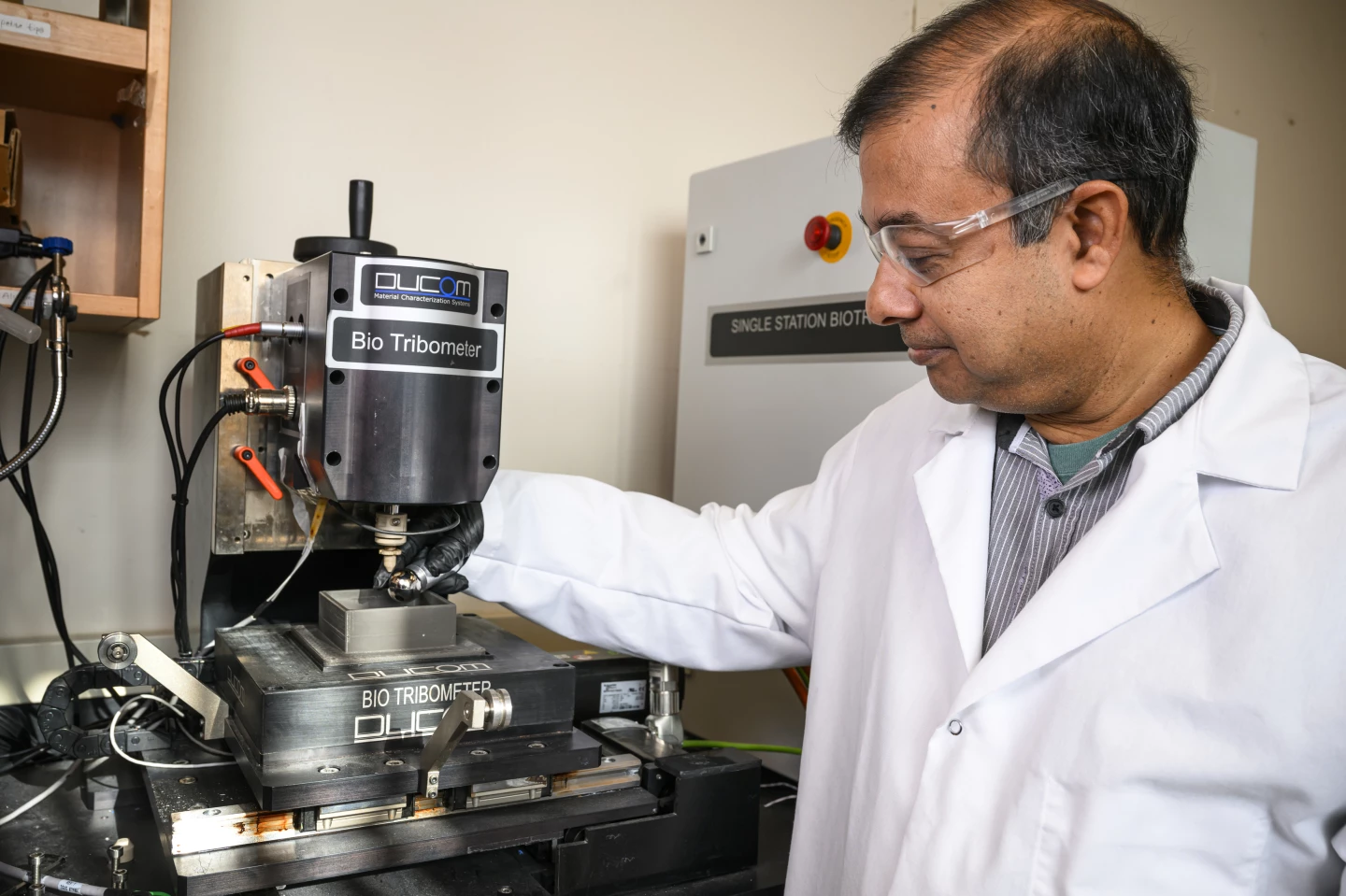
When bacteria come into contact with the material, the copper kills most of them by causing their outer membranes to rupture. The tantalum, meanwhile, encourages the growth of adjacent bone tissue. This factor speeds up the healing process, reducing the timespan in which infections can occur – of course, it also gets patients back on their feet sooner.
In tests performed on lab rats, implants made of the alloy were found to kill 87% of infectious Staphylococcus aureus bacteria on contact. The scientists are now working on boosting that figure to over 99%, plus they're also assessing how well implants made of the material stand up to real-world use.
"The biggest advantage for this type of multifunctional device is that one can use it for infection control as well as for good bone tissue integration," said Prof. Susmita Bose, co-author of a paper on the research. "Because infection is such a big issue in today’s surgical world, if any multifunctional device can do both things, there’s nothing like it."
The paper was recently published in the International Journal of Extreme Manufacturing.
Source: Washington State University