3D printing is set to go to sea in the form of an additive manufacturing technique for repairing submarines. Being developed by Australia’s dedicated submarine sustainment organization, ASC, in partnership with the CSIRO and DMTC Limited, the cold spray printing technology is intended to repair the Royal Australian Navy's (RAN's) Collins Class submarines in situ.
If you look at the size of any country's navy, the numbers can be quite deceptive. What looks like a large fleet on paper may be much smaller because only a fraction of the fleet may be active at any one time. For submarines, only one in four may be actually on duty, with the other three being in transit, under repairs, or used in training.
To keep the RAN up to strength, ASC is looking to 3D printing as part of a two-year project designed to speed up repairs and maintenance. In particular, the company is developing a cold spray technique that fires a spray of supersonic gas that accelerates metal powder particles to form a dense deposit on a surface.
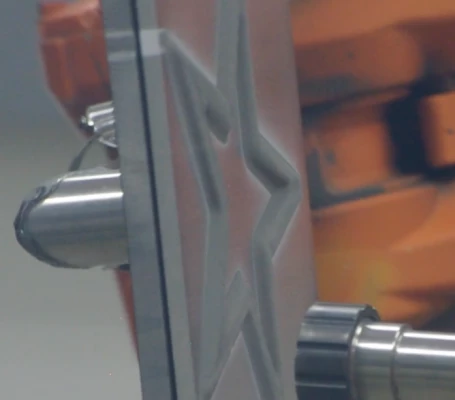
According to ASC, this method doesn't need the high temperatures required for other metal printing processes and doesn't damage other components that might be in the immediate area. The result is a way to make in situ repairs while the submarine is afloat without having to go into dry dock, leading to savings in time and money. The ultimate goal is to license the technology primarily for maintaining the Navy's fleet of Collins Class submarines.
"It’s vitally important for ASC to be on the cutting edge of submarine sustainment innovation, to continually improve Australia’s submarine availability to the Royal Australian Navy service," says ASC Chief Executive Officer Stuart Whiley."The use of additive manufacturing for the repair of critical submarine components, including the pressure hull, will mean faster, less disruptive repairs for our frontline Collins Class submarine fleet."
The video below shows cold spray printing in action.
Source: ASC