Saab has flown a 3D-printed replacement part on the exterior of a Gripen fighter jet for the first time. The test flight over the company's facility at Linköping, Sweden, on March 19, 2021, potentially paves the way for 3D-printed parts to be used to make battlefield repairs.
When talking about military matters it's really easy to get fixated on the flashy topics like fighter jets and forgetting that for every Top Gun pilot there's a very long line of support personnel. In fact, every combat unit on land, sea, or air is only the very sharp tip of a very long logistical spear.
Not surprisingly, one of the biggest and most constant problems is how to keep combat aircraft flying from forward operating bases by ensuring they have enough spare parts to fix battle damage or inevitable wear and tear. This isn't always possible, so mechanics are often reduced to improvising or stealing parts from several aircraft to keep one flying.
To address this problem, Saab and the AMEXCI consortium have been working since 2018 on the Battlefield Damage Repair project, which uses 3D printing technology as a way to quickly produce spares in the field so an aircraft can either complete its mission or fly back to a maintenance base for more extensive repairs.
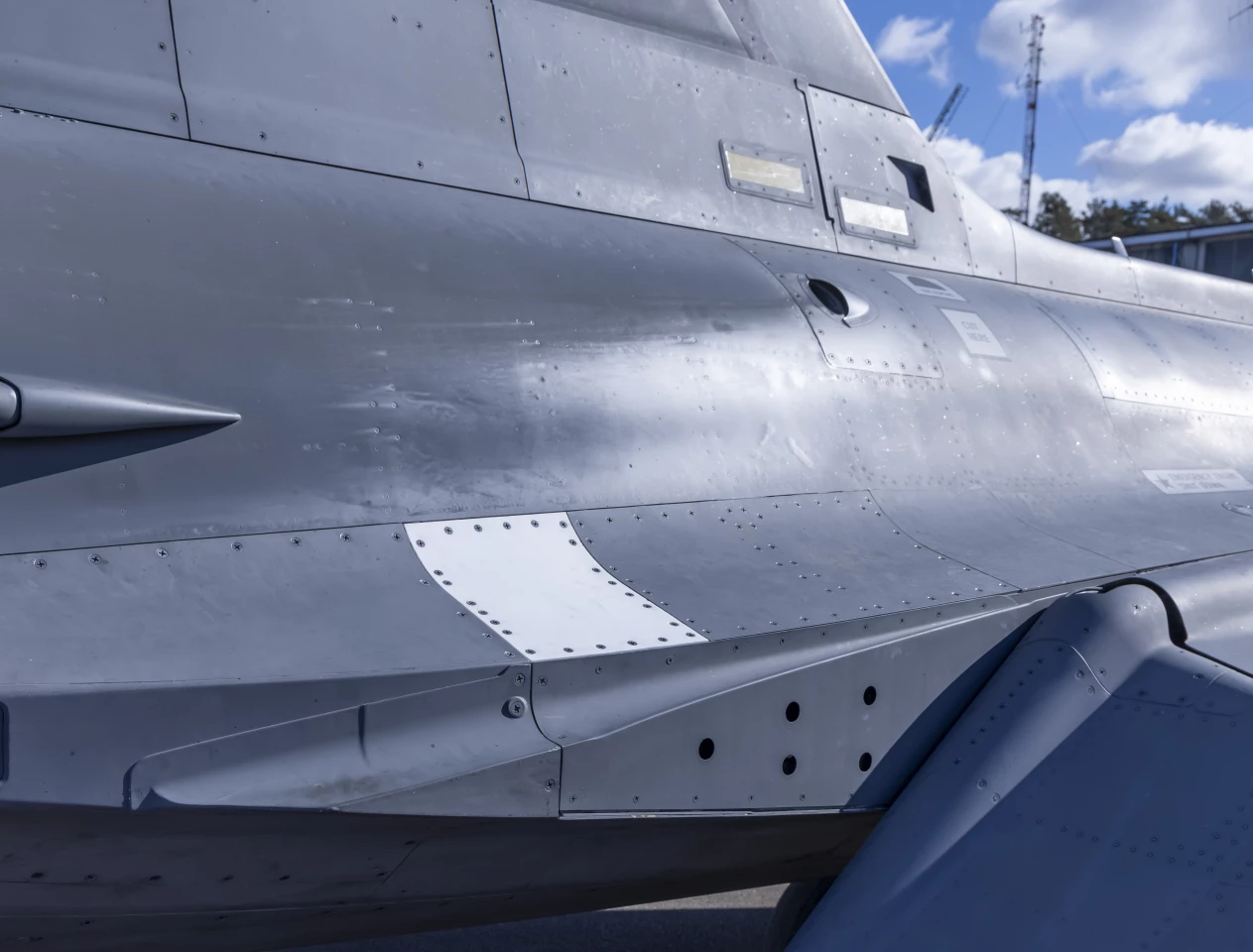
For the recent test, a maintenance hatch on the exterior of the fuselage was replaced with a 3D-printed version. Because there wasn't a digital model for the component, a bespoke scan had to be made before the part was printed out of PA2200 nylon, which is a high-end, high-strength polymer that is not only inexpensive, but chemical and UV resistant. By scanning the part, it was possible to produce a copy that fit exactly like the original for that individual airframe.
The next step in the testing program will be to make sure the 3D-printed spare meets airworthiness requirements as well as finding alternatives to PA2200 that are more flexible and can better withstand the freezing cold of high-altitude flights. Along with this, the development team is working on producing a 3D printing system that can be fitted into a container for deployment to forward bases.
"Post-flight initial inspection of the hatch was very positive and showed no visual structural changes had occurred from the flight," says Håkan Stake, contract manager for support to Gripen C/D, and manager of the development project. "The potential of this approach means that maintenance personnel in the field can get access to individually fitted spare parts and you no longer have to resort to emergency fixes nor cannibalize other broken-down aircraft for their parts, while also further reducing the small number of parts brought on a deployment. This also reduces the operational time lost in repairs."
Source: Saab