It sounds like a scene from Ant-Man, but this is very much real life: scientists at MIT have devised a super shrinking system that can produce 3D nanoscale versions of much larger, custom-made objects, reducing them to around one thousandth the size of the originals.
First, polymer scaffolds of the absorbent polyacrylate material are created using a laser, in a special type of hydrogel. Then, using a technique the scientists are calling implosion fabrication, the whole structure gets shrunk down by adding an acidic mixture. It causes the gel to contract, up to 10 times in each direction (so up to 1,000 times in total).
It's similar to a technique known as expansion microscopy, but working in reverse: rather than expanding the gel so it can be viewed under a microscope, it's resized in the other direction to make the structure it contains much smaller.
Along the way, scientists can fix other types of molecules to the structure, giving them more control over their creations and the materials they're made from. The researchers say the technique could be useful in robotics, medicine, optics and other fields – giving scientists a way of making nanoscale objects more easily.
One of the first uses of the technology could be in creating objects to further analyze the properties of light, for example. Further down the line the process might be used to build more advanced lenses for smartphone cameras or medical equipment.
"You attach the [molecule] anchors where you want with light, and later you can attach whatever you want to the anchors," says Edward Boyden at MIT. "It could be a quantum dot, it could be a piece of DNA, it could be a gold nanoparticle."
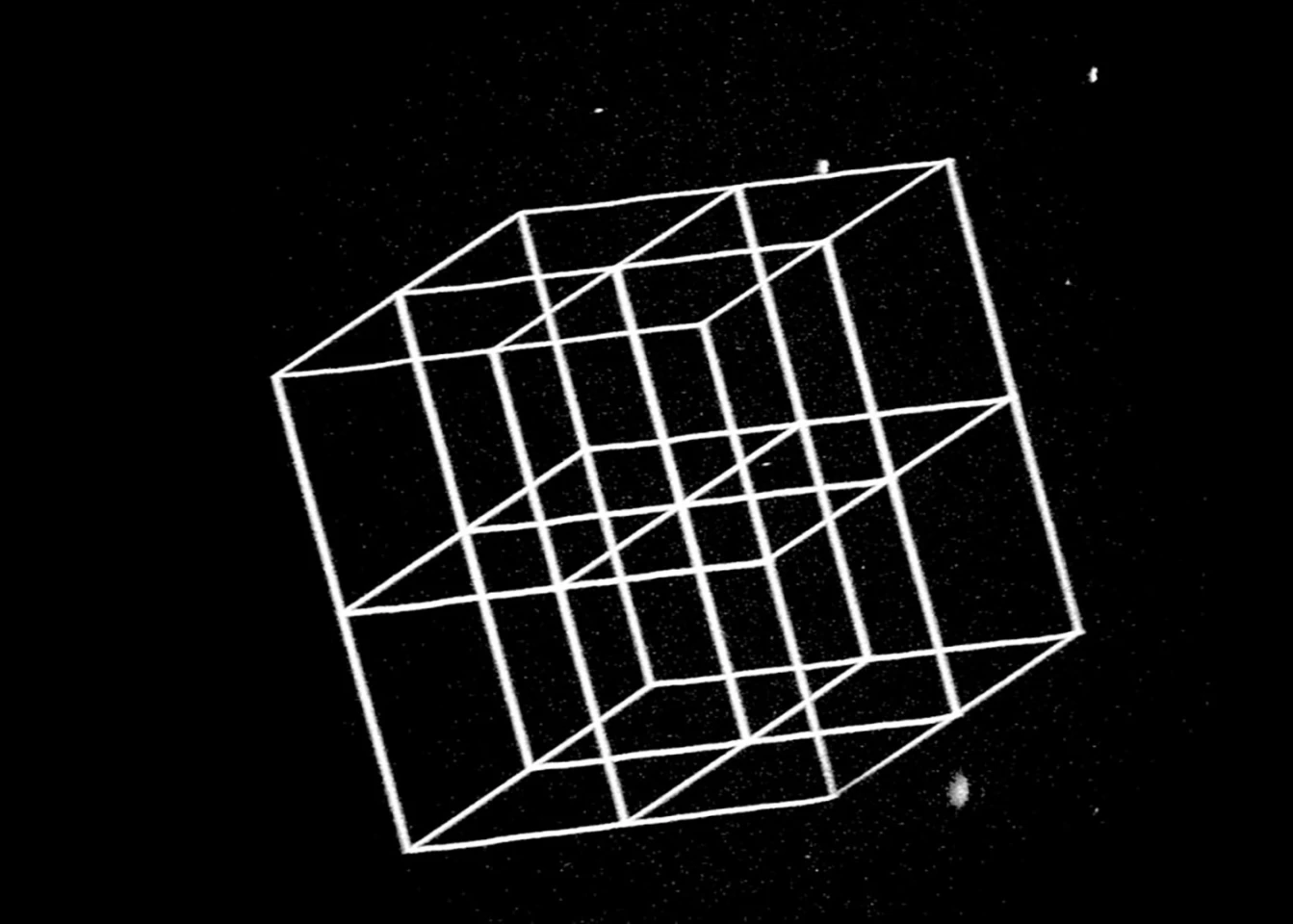
"It's a bit like film photography – a latent image is formed by exposing a sensitive material in a gel to light. Then, you can develop that latent image into a real image by attaching another material, silver, afterwards. In this way implosion fabrication can create all sorts of structures, including gradients, unconnected structures, and multi-material patterns," adds Daniel Oran, another of the MIT team.
The new methodology improves on existing techniques for creating nanostructures in a number of ways: it's faster and simpler than what's been seen before, and it works in three dimensions, which is an added bonus. It can also be used with a variety of materials.
At the moment the scientists are seeing a trade-off between size and resolution. They're able to create objects about 1 cubic millimeter in size, with a resolution of 50 nanometers; up the size to 1 cubic centimeter, and the resolution goes up to about 500 nanometers.
With further refinement though, the team says it should be possible to create objects that are larger and more detailed in their resolution. The good news is that a lot of the equipment needed is already found in science labs.
"People have been trying to invent better equipment to make smaller nanomaterials for years, but we realized that if you just use existing systems and embed your materials in this gel, you can shrink them down to the nanoscale, without distorting the patterns," says MIT's Samuel Rodriques.
The research was published in the journal Science.
Source: MIT