As spacecraft for manned and planetary missions get larger, so do their heat shields – which are becoming very big indeed. To avoid the day when the shield becomes too large for any existing or planned launcher, NASA’s Ames Research Center in California is developing the Adaptive Deployable Entry and Placement Technology (ADEPT) heat shield, which uses carbon-fiber cloth and can be folded up like an umbrella. The cloth heat shield recently completed tests that simulated entering the Martian atmosphere.
Until now, heat shields have consisted mainly of a special phenolic plastics that protect spacecraft entering an atmosphere by ablation. As the shield heats, layers of plastic burn off and carry away the heat before it can reach the payload. Its dish-like shape also acts as a brake to slow the spacecraft down from hypersonic speeds, and since the Apollo program many shields have had aerodynamic properties, so they can be partly steered.
It's an effective system, but such shields are hard, rigid, and heavy. They also work best when the spacecraft is deep in the atmosphere, so they tend to generate extremely high deceleration forces of up to 450 Gs unless special trajectories are used. Since humans can only tolerate forces of less than 10 Gs, this makes ablative shields less than ideal.
The most pressing problem is that such rigid shields need to be made in ever larger diameters to accommodate ever larger spacecraft. This makes it increasingly difficult to fit such shields inside of current or planned rockets. In addition, such shields are expensive to use on a regular basis and place heavy burdens on engineers to handle the design factors.
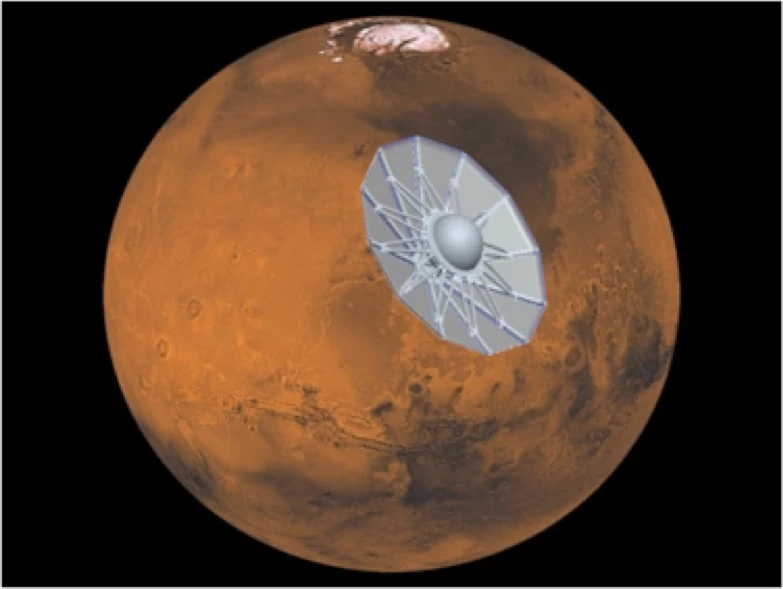
In development in one form or another since the 1970s, ADEPT replaces the hard plastic shield with one made of woven carbon-fiber cloth held rigid by deployable ridges and stays. This shield folds up during launch and then deploys when needed. NASA says that though the cloth shield is thinner and lighter than the plastic version, it protects the spacecraft by re-radiating the heat away before it can conduct to the craft.
Another feature of ADEPT is that its lighter design means that, compared to a conventional plastic shield, it operates effectively at much higher altitudes and can enter the atmosphere at a shallower angle. The ADEPT shield does most of the deceleration with less heating and forces of only 30 Gs, which in turn causes less stress, eliminates the need for a supersonic parachute, and means the probe can land at sites of any elevation. There's even one design that inverts after landing and turns into a tent for future travelers.
The current version of the concept shield can handle a 1,000 kg (453 lb) payload and is undergoing tests at Ames that include vibration, acoustic, and vacuum-thermal testing.
The most spectacular recent test used a blast of hot air from a 21-in (53 cm) diameter nozzle to simulate a bow shock wave in front of a 2-m (6.5 ft) wide ADEPT shield, which was attached to a water-cooled support arm. During the tests, temperatures on the shield reached 3,100º F (1,700º C) while bluish streaks streamed away as a special resin-infused protective coating ablated from the stitching.
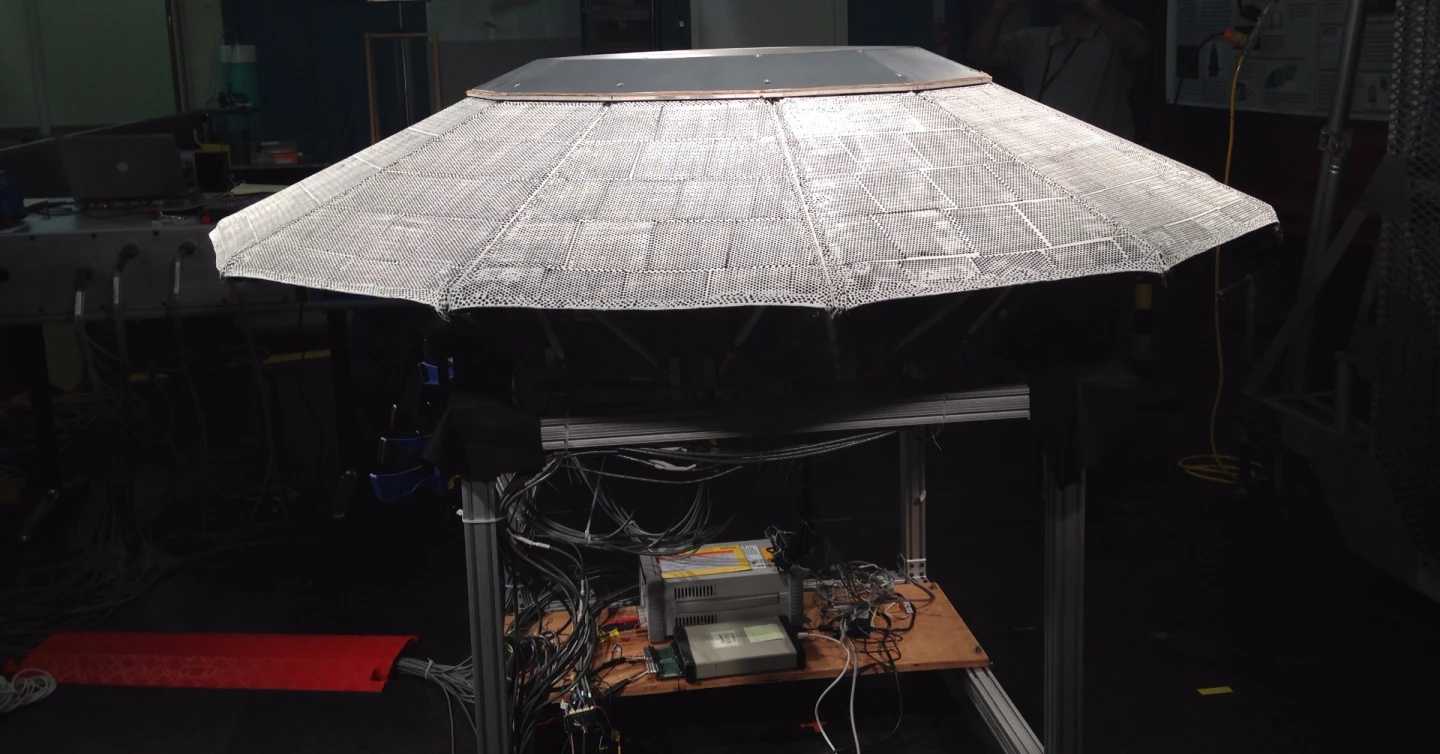
NASA says that more extensive ground and flight testing of the concept shield is scheduled and that an operational version could be ready for a Venus landing by 2017, and perhaps for a manned Mars mission by 2035. When perfected, the technology could also be used for cargo resupply missions as well as the exploration of Saturn, Uranus, or Neptune.
Source: NASA