Orbital Technologies Corporation (ORBITEC) successfully flight tested its patented vortex liquid fuel rocket engine on October 25. The engine was installed in a Prospector-class Garvey Spacecraft Corporation launch vehicle, and the resulting rocket was launched at the Friends of Amateur Rocketry facility near Edwards Air Force Base in California. The flight established substantial progress toward ORBITEC's development of a 30,000-lb (13,600-kg) thrust vortex engine for the US Air Force Advanced Upper Stage Engine Program and for NASA's Space Launch System.
Gizmag asked ORBITEC for more details of the launch, but very few were made available. Fortunately, a fair bit of information can be extracted from the photographs and video of the launch. The launch vehicle was the Garvey P-15 Prospector, about 22 feet (6.7 m) in length and two feet (61 cm) in diameter. The propellants used were not revealed, but most of ORBITEC's static testing of vortex engines has used liquid oxygen and propane. Likewise, neither the weight of the rocket nor that of the propellant were disclosed.
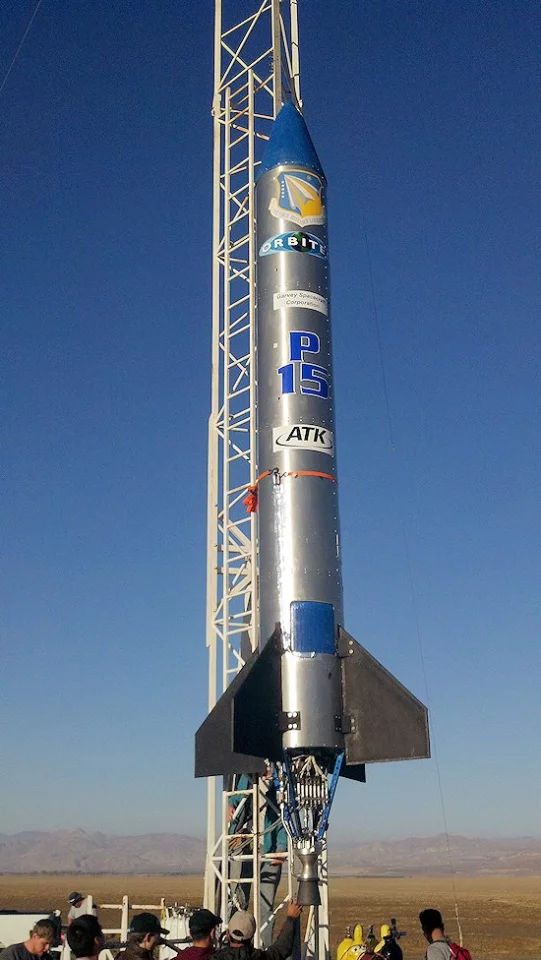
The video shows the vortex engine supplying what appeared to be full thrust for about 10 seconds, after which the rocket reached apogee (its highest altitude) in another 20 seconds. This is sufficient data to estimate the flight history of the rocket, if air drag is ignored, using Newton's equations of motion. The acceleration of the rocket was about 2 g, as it took twice as long for gravity to slow the rocket as the engine accelerated it skyward. This requires a thrust of three times the weight of the rocket, owing to the need to counter gravitational pull. The peak speed of the rocket was about 450 mph (200 m/s), and the peak altitude was a little under 2 miles (3.2 km). These numbers do not change greatly if air drag is included, owing to the weight and size of the rocket. If anything, including drag effects would suggest that the acceleration of the rocket was somewhat in excess of 2 g.
A rocket engine develops a great deal of heat, often reaching temperatures capable of melting the combustion chamber, if not for some form of cooling. Large conventional rocket engines usually use some form of regenerative cooling, where a portion of the fuel is passed through the wall of the combustion chamber, which it cools by evaporation.
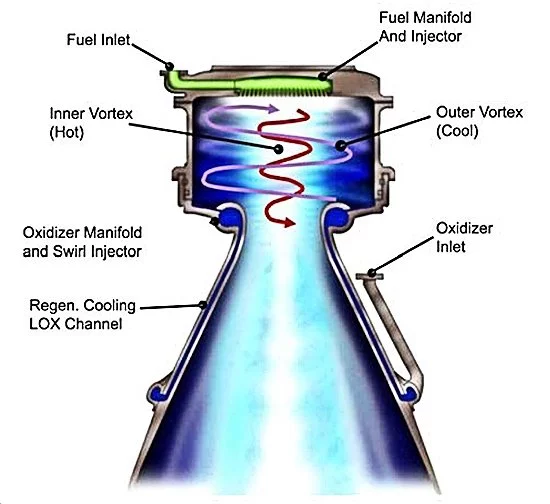
The vortex rocket combustion chamber uses a different approach. Liquid oxygen is fed in from the base of the chamber and is directed into a swirling flow adjacent to the walls of the chamber. When the oxygen reaches the top of the chamber, it spirals inward to form a second swirling vortex flowing toward the exit nozzle. The fuel is injected into the inner vortex where it mixes with the oxygen and burns. Combustion occurs only in the inner vortex, so that the combustion products are isolated from the outer wall by the outer vortex. The chamber wall is exposed only to radiant heat and is kept cooled by the flow of oxygen along the wall.
Among the innovations tested in this flight was a carbon-carbon composite nozzle and cylindrical extension supplied by Alliant Techsystems. The nozzle extension, which is not protected by the vortex cooling of the engine, is seen glowing white-hot in the video below. ORBITEC now stands ready to expand its vortex engine capabilities to support future commercial and military launch systems.
UPDATE (11/02/2012) We have just received more information from ORBITEC. The P-15 length was 25 feet, and the weight at launch was 800 lbs (360 kg). The peak velocity was 600 mph (270 m/s), consistent with minor drag effects and an average acceleration of 2.75 g.
Source: ORBITEC