German outdoor gear specialist Vaude has taken the next logical steps in "Leave No Trace" backpacking, simplifying a backpack down to a single material and 3D-printed components. Still just a prototype for now, the Novum 3D backpack lays the groundwork for a more eco-friendly breed of gear that can be completely recycled at the end of its useful life.
"Ideally, a product should be returned completely back to the production process at the end of its life cycle," Vaude said in introducing the Novum 3D last month. "This is true recycling, but it is still a big challenge for the textile industry at the moment. Many products consist of at least five to 10 different materials or mixed fabrics and, therefore, cannot be separated by type."
So Vaude turned to a simple concept we've been seeing more and more of lately, including inside the recent Polestar O2 concept car: mono-material construction. The Novum 3D pack, straps and back padding are made from 100-percent thermoplastic polyurethane (TPU), so there's no mixed materials to complicate recycling efforts. All non-TPU components, such as the buckles, are easily removable so that they can be stripped off ahead of recycling.
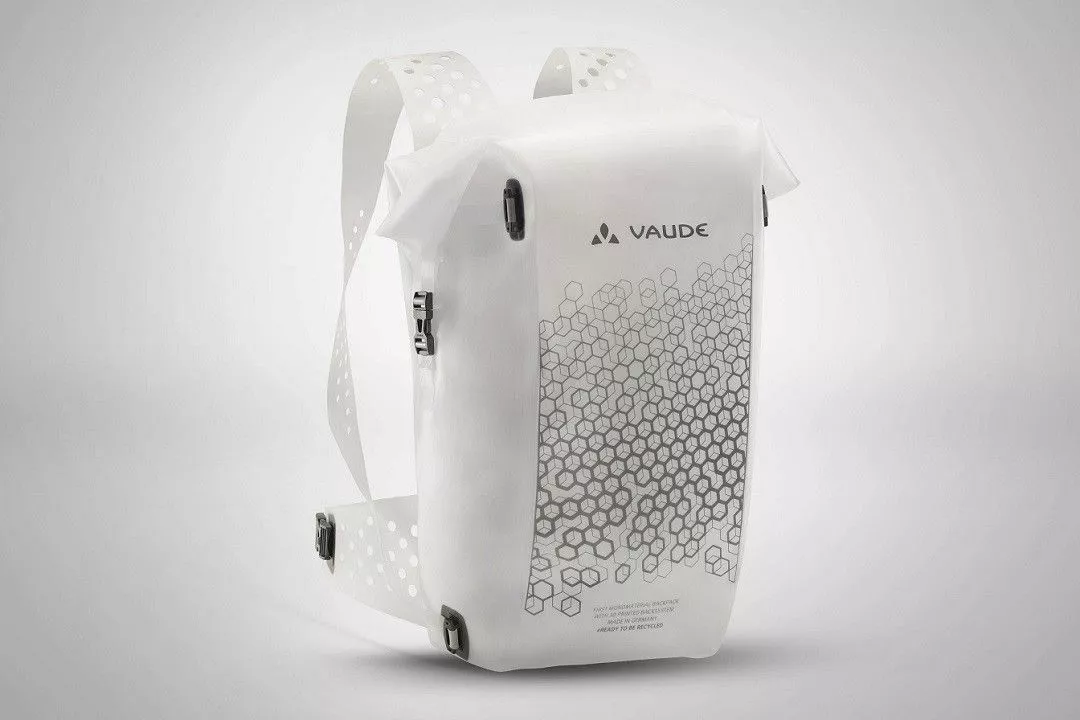
Welded seams, which Vaude already uses in production backpacks and bags, also feature in the recyclability of the Novum 3D. The welds eliminate the need for thread that would otherwise secure various components and pieces of material together, maintaining the integrity of the mono-material construction. Welded seams are also valued because they eliminate needle perforations and thereby improve waterproofing.
A substandard product that sits on store shelves or makes a quick trip to retirement would undermine Vaude's eco-friendly intentions, so the company has worked hard to make the Novum 3D a highly comfortable, functional backpack that also happens to be recyclable. To this end, it teamed with German plastics and additive manufacturing specialist Oechsler to 3D-print a TPU honeycomb panel in place of the typical foam back panel. The honeycomb structure was chosen for optimal stability with the least amount of material and weight, as well as the natural ventilation it provides by way of an open design. Vaude and Oechsler use additive manufacturing to vary lattice structures and alter hardness levels throughout different back panel zones, ensuring better pressure distribution and damping for improved overall comfort and on-trail performance.
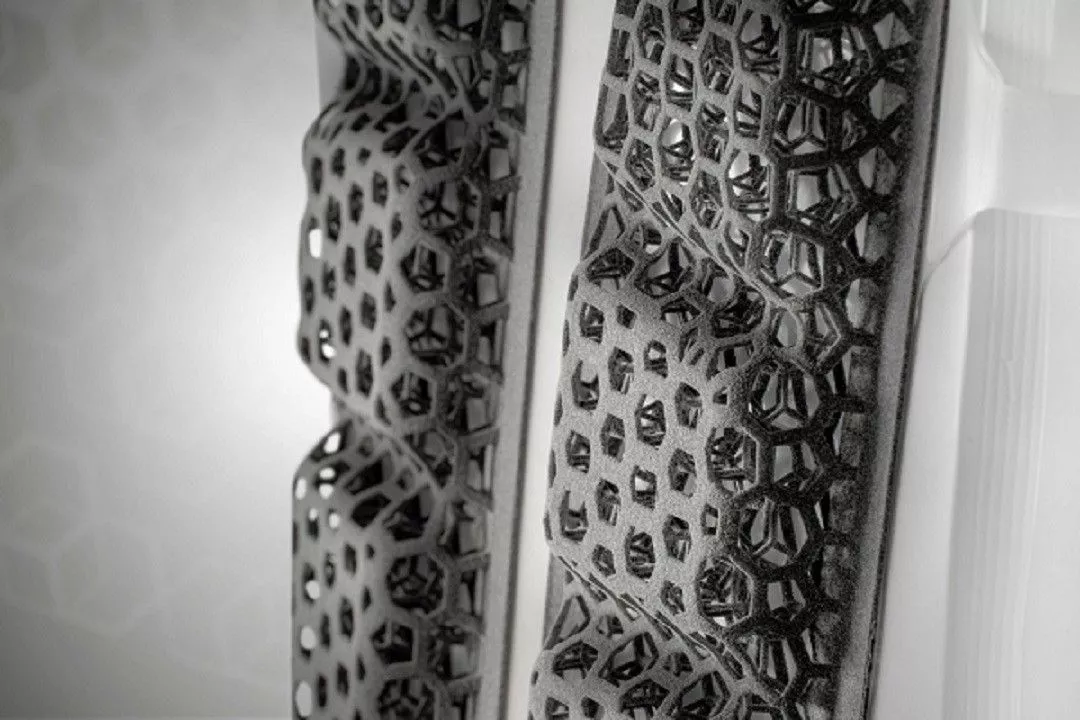
Vaude also stressed that the all-German collaboration with Oechsler contributes to the overall sustainability of the Novum 3D design, being designed, developed and produced at Vaude's climate-neutral headquarters and cutting out the need for long-distance shipping. And while that might seem like bluster that only relates to the prototype, Vaude has long held "Made in Germany" as a tenet of its corporate mission, building backpacks and other products at its own German plant since its inception in 1980. In fact, after a 2015 lightning strike severely damaged its original plant, the company doubled down on domestic manufacturing by building a larger plant at its Tettnang-Obereisenbach headquarters.
Vaude will show the Novum 3D backpack prototype at the 2022 OutDoor by ISPO show this June, where it's certain to draw lots of interest and feedback.