A team of ETH Zurich students has come up with a unique design for a wind-proof camping stove. Its shape, only made possible by additive manufacture, shields the burner from harsh winds and allows the device to boil water with high efficiency.
Led by doctoral student Julian Ferchow, the team designed the PeakBoil stove to fit inside a special kettle jug, which allows a gas tube to feed fuel through the bottom. A series of Venturi nozzles use localized pressure differentials to feed the flames inside the combustion chamber, which is protected from wind by high sides and a narrow top chimney.
The rippled walls of the chamber increase the amount of contact they have with the water in the kettle, and they're as thin as possible to encourage heat transfer.
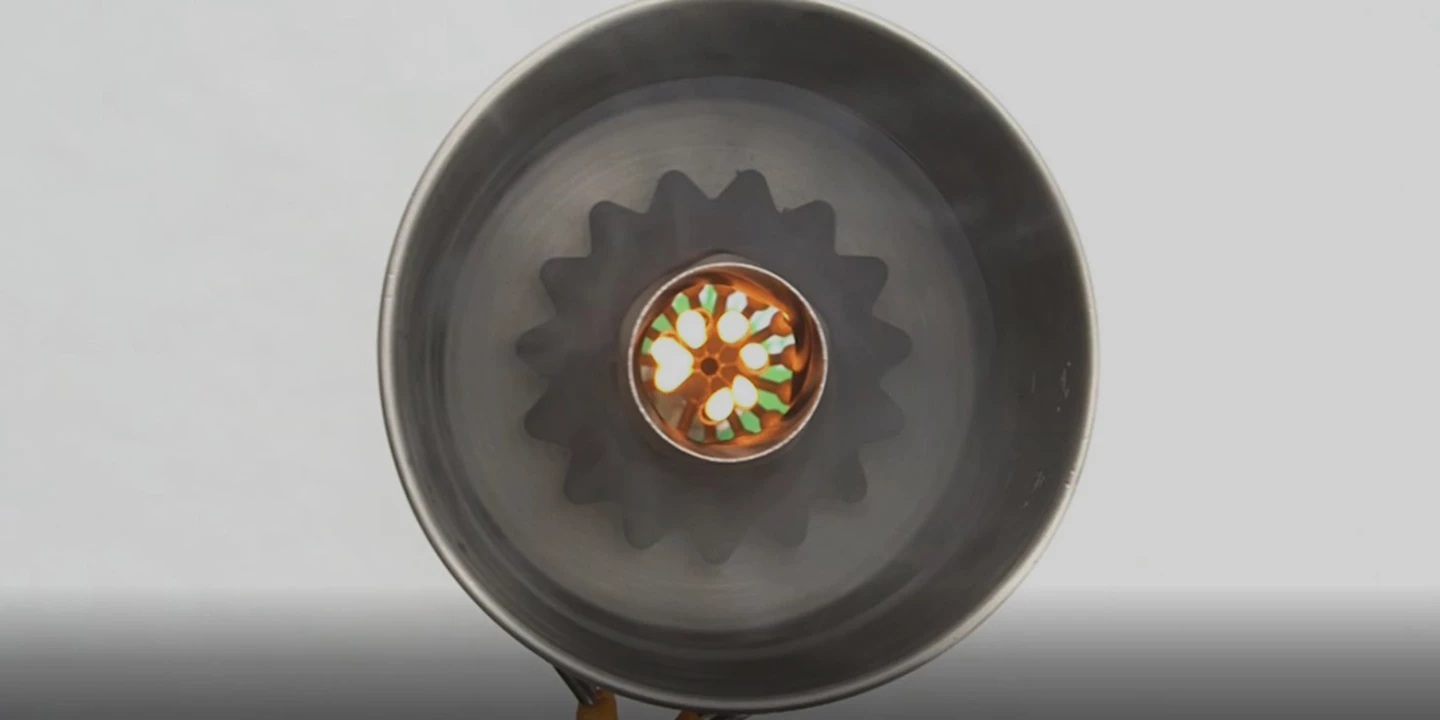
This complex, single-piece combustion chamber couldn't be manufactured using conventional techniques, and is only possible thanks to additive manufacture. In this case, selective laser melting was used to fuse metal powder together in layers just 1/30th of a millimeter thick.
The PeakBoil team tested a prototype during a ski tour of the Swiss Alps, and found it easy to get the thing lit and water boiled even in strong winds. They also won a prize in the 3D Pioneers Challenge contest, and plan to use the proceeds to refine the design and seek manufacturing partners. The design could also be used, according to the team, in tankless, gas-fired water heaters or gas turbines.
The production process of the PeakBoil can be seen in the video below.
Source: ETH Zurich