A new 3D-printed robot called Poppy is helping a team of French researchers study bipedal walking and human-robot interaction. They were able to design, fabricate, and assemble a relatively large robot for around €8,000 (US$11,000) including servo motors and electronics. That's about a third the cost of commercial robots in the same size category like the RQ-TITAN, and is still cheaper than smaller humanoids like the Aldebaran Robotics NAO. And best of all, they plan to make their design open source.
One of the ways they managed to keep the cost down is by using lightweight materials, which means the robot requires less powerful (and cheaper) servo motors. Standing 84 cm (33 in) tall, Poppy weighs in at just 3.5 kg (7.7 lb). The Sony QRIO, by comparison, was 26 cm (10 in) shorter yet it weighed twice as much. Still, most of the cost lies in the robot's 25 servo motors: it utilizes 21 high-end Robotis Dynamixel MX-28s, two MX-64s, and two AX-12s. It's powered by a Raspberry Pi, and is equipped with 16 force-sensing resistors, two HD cameras, a stereo microphone, and an inertial measurement unit. Poppy's "face" is an LCD screen which can be used to show emotions (or to debug).
Making a more human robot
One of the main reasons the INRIA Flowers (FLOWing Epigenetic Robots and Systems) team opted to build its own robot is because none of the available commercial kits are truly biologically inspired. By rapidly-prototyping their own robot, Poppy could challenge some of the usual robot design conventions.
To begin with, it has an articulated spine with five motors – almost unheard of in robots of this size, but one of the ongoing topics at INRIA Flowers since its first humanoid, ACROBAN, from several years ago. The spine not only allows Poppy to move more naturally, but helps to balance the robot by adjusting its posture. The added flexibility also helps when physically interacting with the robot, such as guiding it by its hands, which is currently required to help the robot walk.
Looking at the knees, you'll see some springs spanning the upper and lower leg joints. The tension in the springs helps to keep the supporting leg straight during each step without motorization. And farther down, its feet are smaller than most robots of Poppy's size, and its toes are thin, allowing them to bend. Rather than planting each foot parallel to the ground, which is how most robots this size walk, the toes help the robot achieve "heel to toe" walking. And as for those children's shoes Poppy wears? They're equipped with five pressure sensors on each sole, which provide useful data.
One of the more obvious deviations in design can be seen in its upper legs, which bend inwards at an angle of six degrees. Despite the fact that this more closely models the human femur, most humanoid robot designs have opted for straight leg linkages. By bending the thighs in, the distance between the two feet is shortened, moving the supporting leg's foot closer to the robot's center of gravity. And that makes it more stable when standing on one leg and when walking.
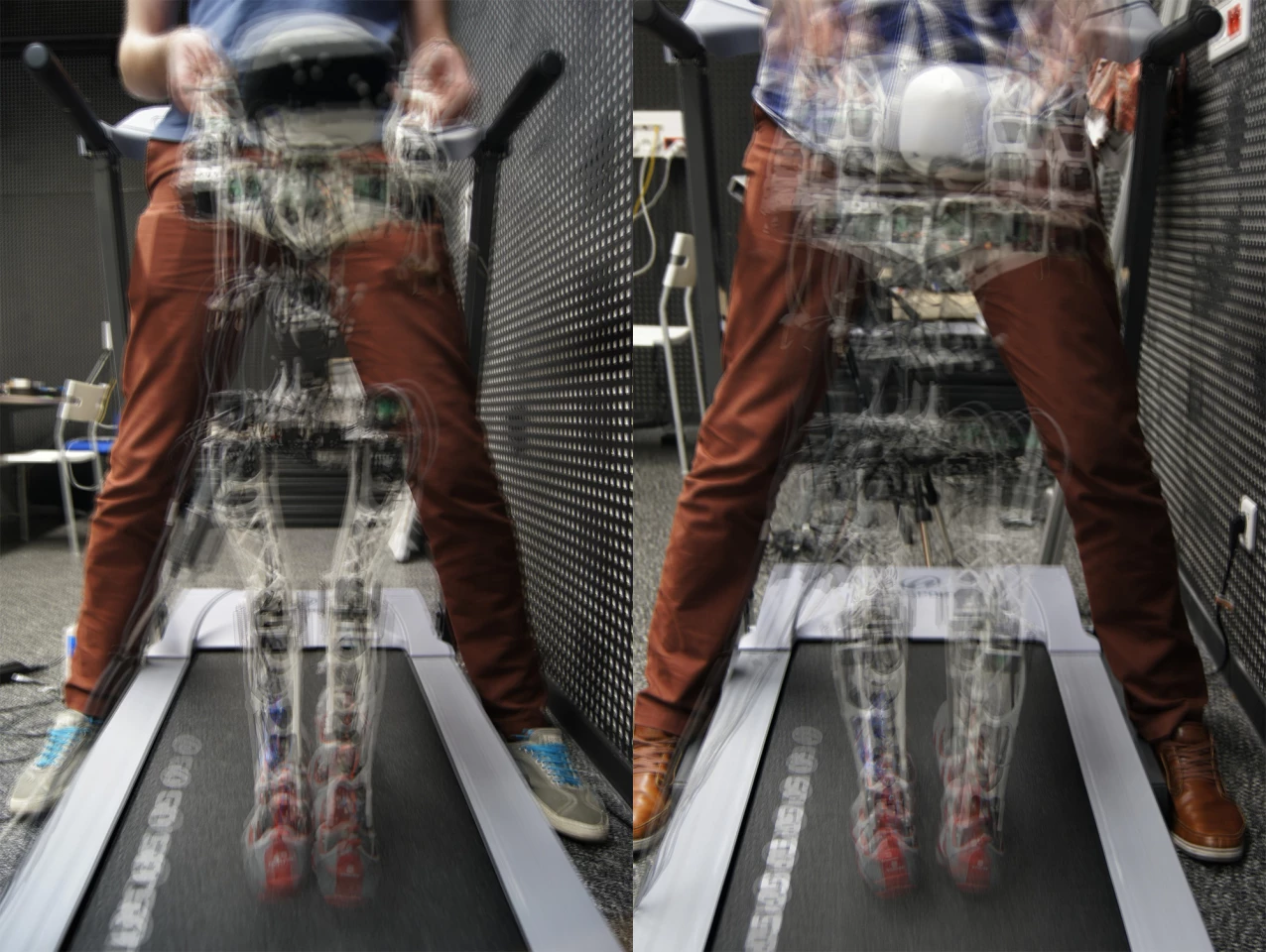
The INRIA team produced two versions of Poppy: one with straight thighs and another with the bent ones. Experiments showed that the robot with bent thighs swayed far less during its walking gait, making it much more stable. However, the robot still can't balance on its own, so for now it needs a human trainer.
In the future, the team hopes to get Poppy walking on its own, and plans to share its designs with other labs to promote more biologically-inspired humanoid robot designs.
You can see Poppy in the following video.
Sources: INRIA Flowers, Poppy Project via 3ders