Smartphones have come a long way in a few short years, but two things have remained constant; most sport a "slab of glass" form factor, and dropping one makes you wish you’d had it insured. Designers have used new materials, such as Gorilla glass and sapphire to make phone displays lighter and more durable, but these have introduced their own problems – especially when it comes to manufacturing. Gizmag spoke with Raydiance, a company specializing in cutting-edge laser fabrication methods, about its new R-Cut femtosecond laser system that promises a “new paradigm" in high-tech glass fabrication.
According to Raydiance, the R-Cut combines an ultra-short pulse laser and micromachining processes to cut very hard and brittle materials very quickly and with less chance of their chiping or shattering. It’s based on a femtosecond laser, which is generated by a technique called chirped pulse amplification that produces a burst of laser light that lasts one quadrillionth of a second. This is so short that during its pulse, the laser will only travel 1/100th the width of a human hair.
What’s important about this laser is that these very tiny pulses of light can concentrate so much power in such a small space of time that they can destroy anything they touch, and the laser can fire these pulses many times a second. The R-Cut uses these pulses in "cold ablation" for drilling very precise holes or shaping materials. The femtosecond laser vaporizes matter so fast that the surrounding materials have no time to heat up and there’s much less of a shock wave than with longer-duration lasers. The trick is to apply enough power in a short enough time to remove material without stressing the surrounding area.
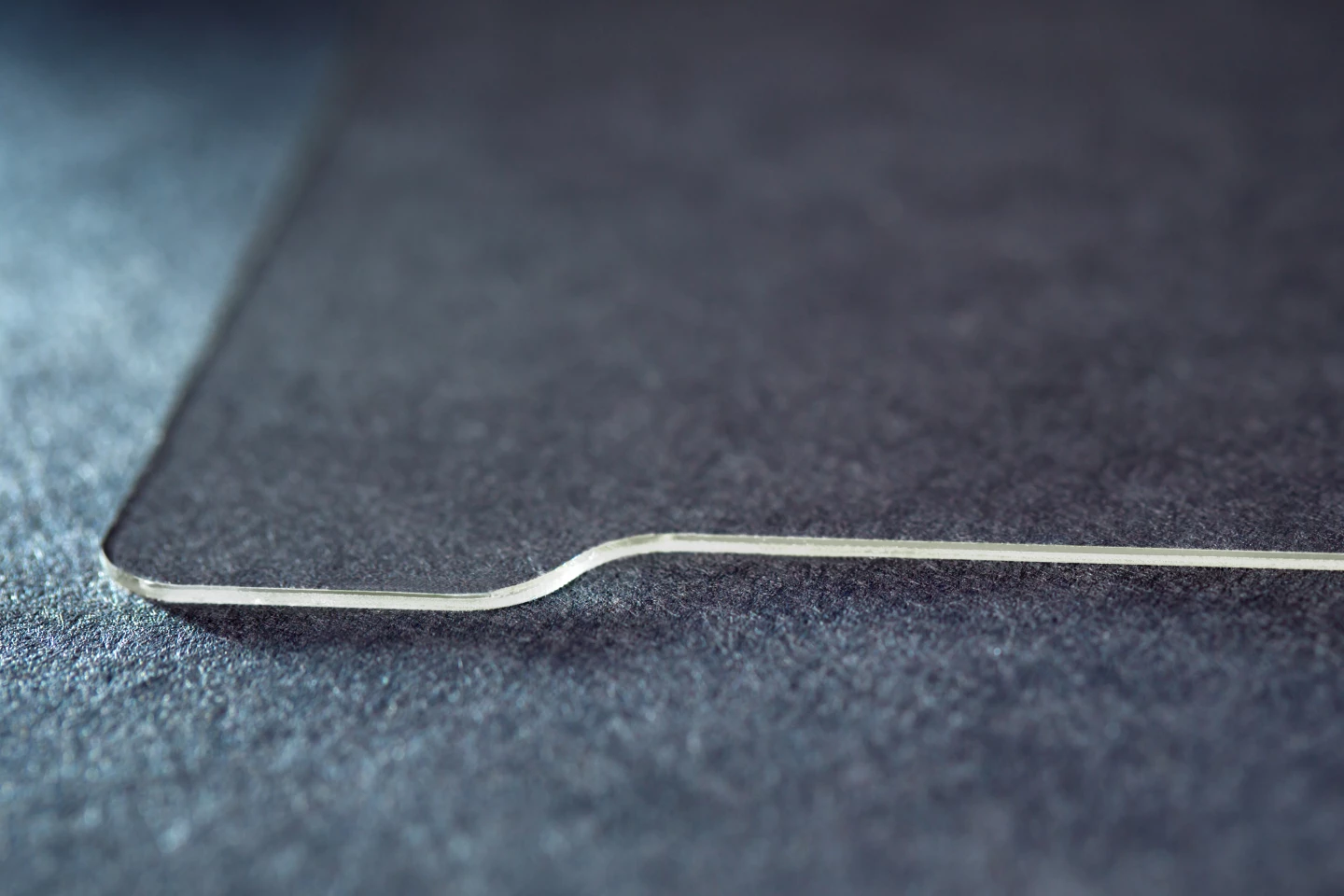
Michael Mielke, Chief Scientist at Raydiance told Gizmag that the company has used fiber optics and developed algorithms that allow the R-Cut to take the femtosecond laser from being a laboratory curiosity and make it into an industrial tool that can quickly cut brittle materials in a matter of seconds instead of minutes or hours.
Aimed at high-volume manufacturers, the R-Cut can handle Gorilla glass, sapphire crystals, and similar hard and brittle materials. It can work on thinner materials than previously possible and form them into complex shapes, such as curves, chamfers, and holes on a micron scale, with less waste and at lower costs providing savings of more than 50 percent. The company also says that it can work on both strengthened and unstrengthened glass while doubling efficiency.
"The laser is fully programmable, which eliminates a lot of the hard-tooling with the mechanical approaches," says Stefan Zschiegner, Senior Vice President of Marketing at Raydiance. "You can basically take a design drawing and in 24 hours you have a fully functioning prototype."
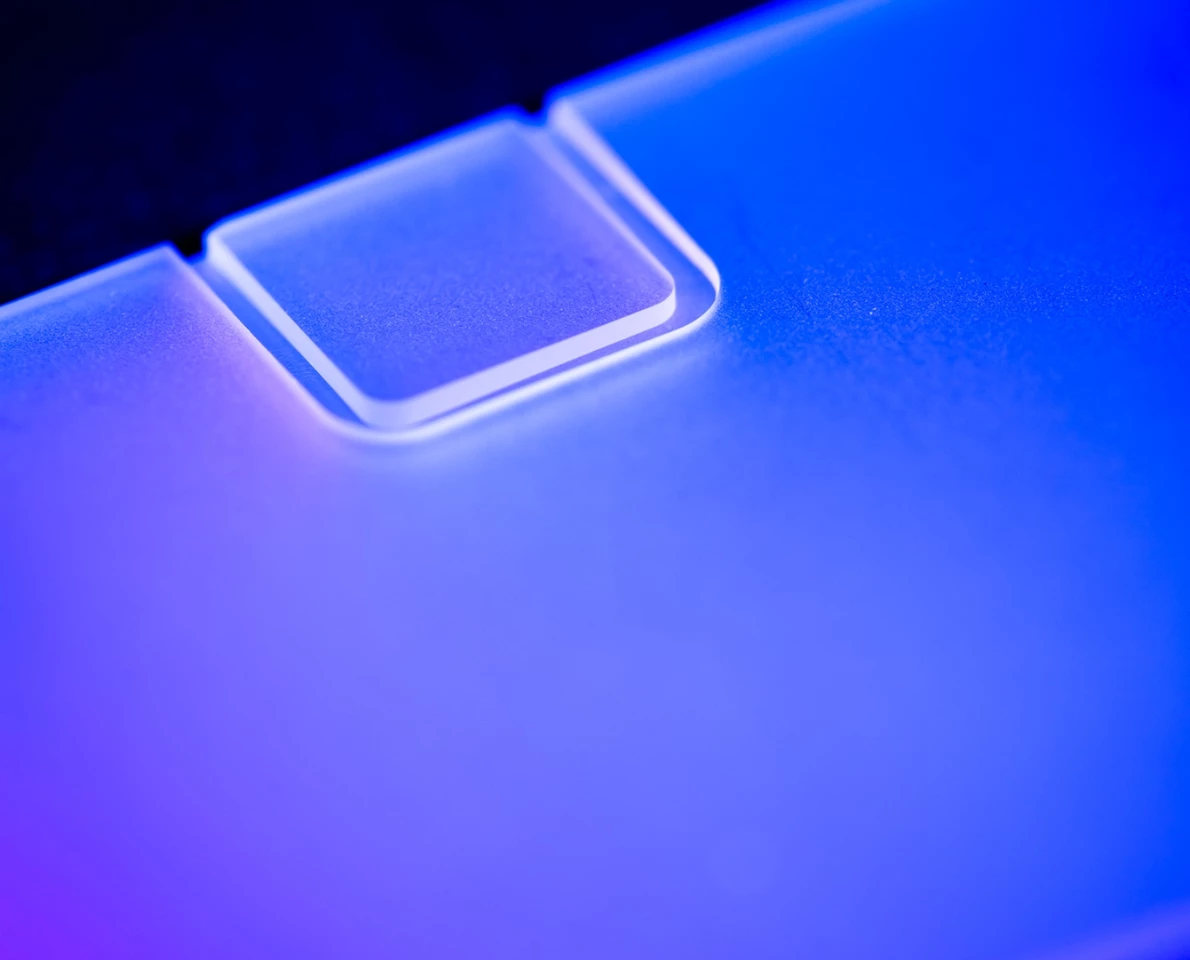
Zschiegner went on to say that the R-Cut represents a new paradigm that will allow manufacturers to rethink their production methods. He sees the laser technique as a way to allow for mobile phones of more organic shapes, the use of microholes replacing the conventional slots used for microphones and speakers in phones for better sound quality, and glass covers for phones with a more rounded shape instead of flat, which could also be applied to car dashboard instruments.
According to Zschiegner the R-Cut technology will be moving into the manufacturing arena within the next year.
Source: Raydiance