Soft-bodied robots have numerous desirable qualities, such as the ability to squeeze through gaps, or survive being stepped on. And so far, they've typically been manually assembled on a one-off basis. That could be about to change, though, thanks to a new manufacturing method.
Developed by scientists at the University of California San Diego, the technique is inspired by the exoskeletons of insects. Although we may think of those exoskeletons as being like unyielding suites of armor, they are in fact rigid in some places (for structural support) while being flexible in others (for resilience and mobility).
The UC San Diego system likewise produces so-called "flexoskeletons," that combine rigidity and flexibility. This is achieved by 3D-printing a polymer layer onto a thin, flexible sheet of polycarbonate. By tweaking the printing process, it's possible to make the polymer flexible where needed – so it bends with the polycarbonate base – but to exhibit varying degrees of rigidity elsewhere.
A small flexoskeleton can reportedly be produced using an ordinary 3D printer, "for a small fraction of the cost" that it would take to otherwise create such a structure. That skeletal base can then be paired up with Lego-like electronic components, to form a complete robot.
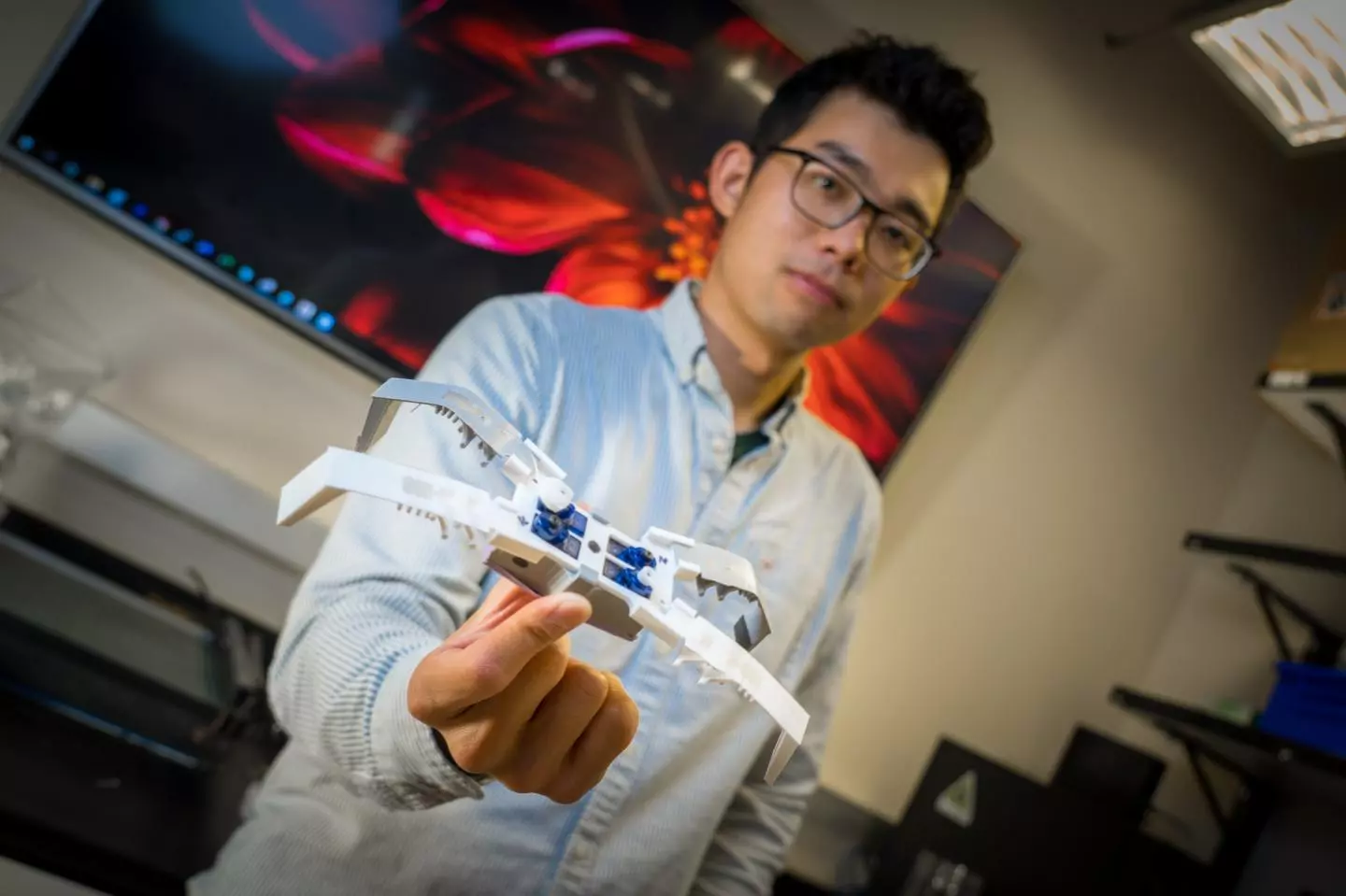
Printing and assembling such a bot currently takes less than two hours. That said, the scientists are now developing a completely automated assembly line for creating whole "swarms" of robots, that would work together on tasks such as searching for survivors at disaster sites.
"We hope that these flexoskeletons will lead to the creation of a new class of soft, bioinspired robots," says Prof. Nick Gravish, senior author of a paper on the research. "We want to make soft robots easier to build for researchers all over the world."
The paper was recently published in the journal Soft Robotics. One of the robots can be seen in motion, in the following video.
Source: University of California San Diego via EurekAlert