Of all the things that we regularly dispose of, you would think that shoes would be one of the most difficult to recycle. Not only are well-used shoes kind of ... gross, but they're also made of a variety of different materials, all of which are joined together. Nonetheless, scientists at Loughborough University in the UK announced last week that they have created and trialled "the world’s first comprehensive system for separating and recovering useful materials from old footwear."
The recycling system was developed at the university's Innovative Manufacturing and Construction Research Centre, and is the end result of a 10-year research program.
The process begins with shoes being manually sorted into broad categories (such as "trainers"), and having metal components such as eyelets removed. They are then automatically shredded and granulated, ending up as tiny fragments. Those fragments are sorted according to material, using three main methods – cyclonic separation, zigzag separation, and vibrating tables.
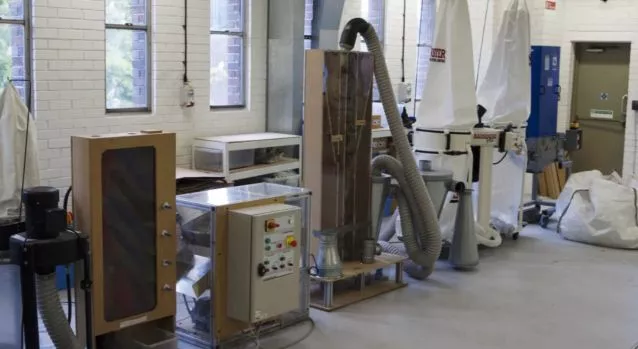
In the cyclonic separation process, a tornado-like vortex of air is created within an enclosed cylindrical chamber. The lightest fragments are picked up by that vortex and carried out of the chamber through an outlet tube in the top, while heavier fragments remain behind on the bottom.
Next, in the zigzag separation process, fragments are fed into the top of an enclosed column, and fall to the bottom by "zig-zagging" back and forth between alternating sloping platforms. Along the way, jets of air blowing in from the sides push the lighter fragments off to other receptacles, allowing only the heavier ones to reach the bottom.
Finally, when mixed fragments are placed on a sieve-like screen built into a vibrating table, the vibrations cause the smaller fragments to fall through the gaps in the screen, with the larger ones remaining on top.
By the time they get to the end of the line, the shoe fragments are sorted into four material types: leather, foam, rubber and other materials. The leather fragments could then be used to create sheets of bonded leather (real leather mixed with synthetic); the foam could go into items such as carpet underlays; the rubber could be used either in playground-surfacing materials or even in the soles of new shoes; and the mixed materials might find use as building insulation.
The university is now working with "major footwear manufacturers" to develop methods of designing footwear that would make it as recycling-friendly as possible. This could include using materials of very different densities, as doing so would make the separation process quicker and thus cheaper.
Alternatively, shoes can also be kept from sitting in landfills for millennia by making them out of compostable materials.
More information on the Loughborough system is available in the slide show below.
Source: Engineering and Physical Sciences Research Council